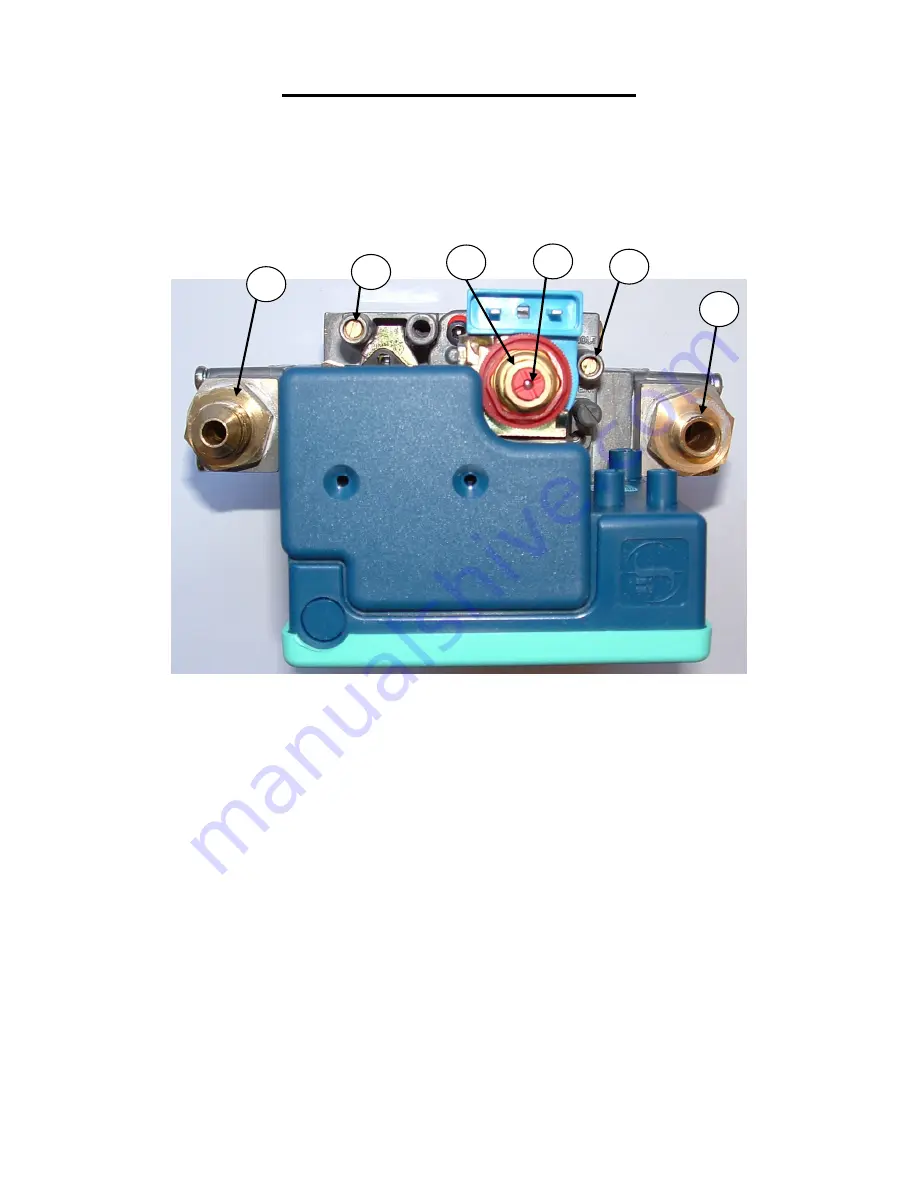
Revised 26/05/10
ALLURE ELECTRONIC Install Ops May2010
Page 10 of 23
GAS PRESSURE TESTING
Use pressure test point (Fig 1) on manifold
.
A manometer is required to check the gas supply and operating pressures.
To attach manometer, remove hearth, rear tray and baffle.
This will expose the control valve so manometer tubes can be attached to the
pressure taps
as
shown below.
(Fig 4.)
Important
: Ensure Pressure Tap is tightened and checked for leaks after testing.
Control Valve, Parts (Fig 4 and Fig 5)
1.
Main Gas Inlet.
2.
Inlet Pressure Tap Point. Tighten to torque 1.0Nm
3.
High Pressure Adjust (10mm Brass Nut)
4.
Low Pressure Adjust (Red Plastic X Screw)
5.
Outlet Pressure Tap Point. Tighten to Torque 1.0Nm
6.
Main Gas Outlet.
1
6
5
4
2
3