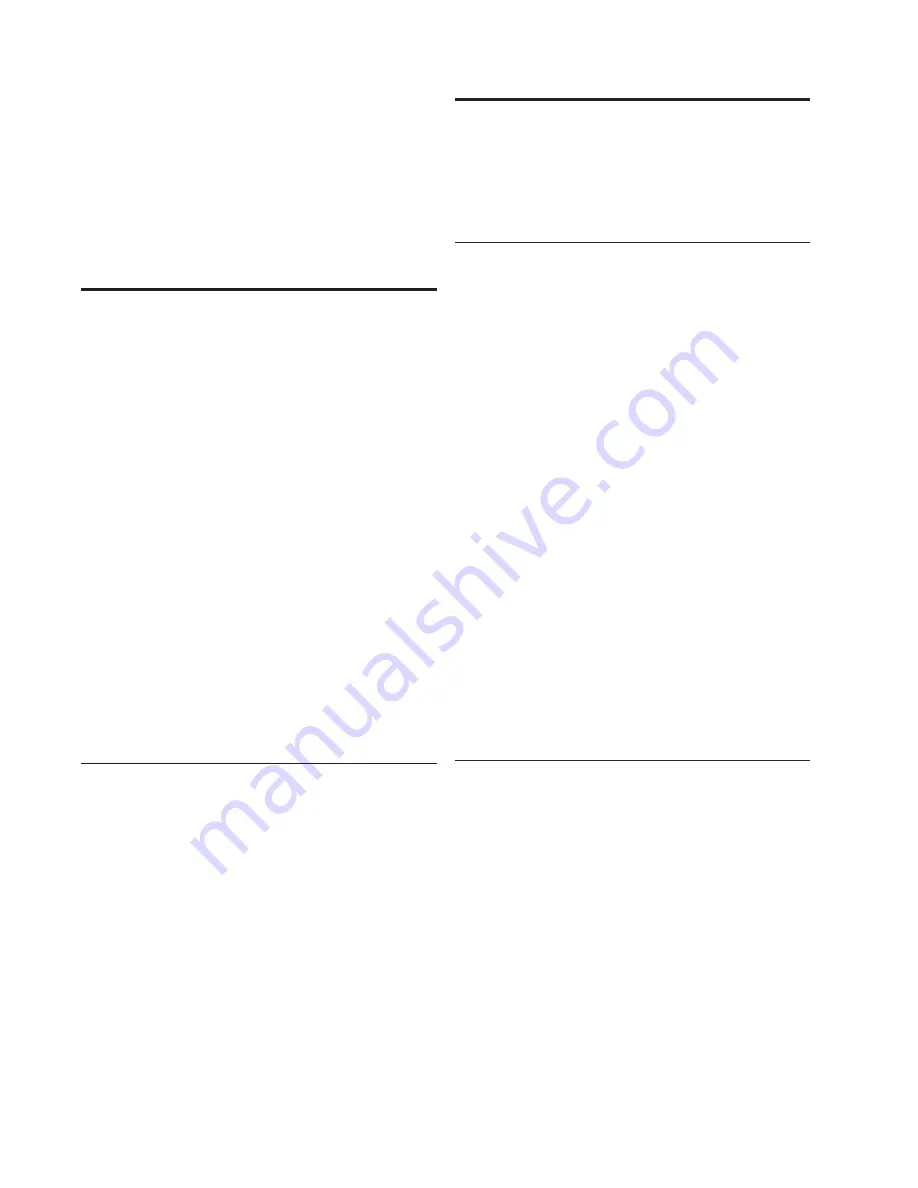
Page 4
09101-90(I)
3. ALIGN VANE
a) Connect instrument to an indicator.
b) Choose a known wind direction reference point on the
horizon.
c) Sighting down instrument centerline, point nose cone at
reference point on horizon.
d) While holding vane in position, slowly turn base until
indicator shows proper value.
e) Tighten mounting post band clamp.
f) Engage orientation ring indexing pin in notch at instrument
base.
g) Tighten orientation ring band clamp.
CALIBRATION
Periodic calibration checks are desirable and may be necessary
where the instrument is used in programs which require auditing of
sensor performance. Recalibration may be necessary after some
maintenance operations.
An accurate wind direction calibration requires a Vane Angle
Fixture (Young Model 18112 or equivalent). Details are listed under
"VERTICAL SHAFT BEARING REPLACEMENT STEP 10. ALIGN
VANE". The sensor nose cone must be removed if any adjustment
is required.
Wind speed calibration is determined by propeller pitch and the
output characteristics of the transducer. Calibration formulas
showing wind speed vs. propeller rpm are shown on the wiring
diagram. Standard accuracy is ± 0.3 m/s (0.6mph). For greater
accuracy, the device must be individually calibrated in comparison
with a wind speed standard. Contact the factory or your YOUNG
supplier to schedule a NIST (National Institute of Standards &
Technology) traceable wind tunnel calibration in our facility.
To check wind calibration using a signal from the instrument,
temporarily remove the propeller and connect an Anemometer
Drive to the propeller shaft. Apply the appropriate calibration
formula to the calibrating motor rpm and check for the proper
value. For example, with the propeller shaft turning at 3600 rpm
adjust an indicator to display 17.6 meters per second (3600 rpm x
0.00490 m/s/rpm = 17.6 m/s).
Details on checking bearing torque, which affects wind speed and
direction threshold, appear in the following section.
CALIBRATION FORMULAS
Model 09101 Wind Monitor-SE w/08234 Propeller
WIND SPEED vs PROPELLER RPM
m/s
= 0.00490 x rpm
knots = 0.00952 x rpm
mph
= 0.01096 x rpm
km/h = 0.01764 x rpm
MAINTENANCE
Given proper care, the Wind Monitor should provide years of
service. The only components likely to need replacement due
to normal wear are the precision ball bearings. Only a qualified
instrument technician should perform the replacement. If service
facilities are not available, return the instrument to the company.
Refer to the drawings to become familiar with part names and
locations. Maximum torque on all set screws is 80 oz-in.
FLANGE BEARING REPLACEMENT
If anemometer bearings become noisy or wind speed threshold
increases above an acceptable level, bearings may need
replacement. Check anemometer bearing condition using a
Model 18310 Propeller Torque Disc. Without it, a rough check
can be performed by adding an ordinary paper clip (0.5 gm) to
the tip of a propeller blade. Turn the blade with the paper clip to
the "three o'clock" or "nine o'clock" position and gently release it.
Failure to rotate due to the weight of the paper clip indicates that
the anemometer bearings need replacement. Repeat this test at
different positions to check full bearing rotation. If needed, bearings
are replaced as follows.
1. REMOVE OLD BEARINGS
a) Unscrew nose cone. Do not lose o-ring seal.
b) Loosen set screw on magnet shaft collar and remove
magnet.
c) Slide propeller shaft out of nose cone assembly.
d) Remove front bearing cap which covers front bearing.
e) Remove front and rear bearings from nose cone assembly.
Insert edge of a pocket knife under bearing flange and lift it
out.
2. INSTALL NEW BEARINGS
a) Insert new front and rear bearings into nose cone.
b) Replace front bearing cap.
c) Carefully slide propeller shaft thru bearings.
d) Place magnet on propeller shaft allowing 0.5 mm (0.020")
clearance from rear bearing.
e) Tighten set screw on magnet shaft collar. Do not overtighten.
f) Screw nose cone into main housing until o-ring seal is
seated. Be certain threads are properly engaged to avoid
cross-threading.
VERTICAL SHAFT BEARING REPLACEMENT
Vertical shaft bearings are much larger than the propeller shaft
bearings. Ordinarily, these bearings will require replacement less
frequently. In many cases, they may last the life of the sensor.
Check bearing condition using a Model 18331 Vane Torque
Gauge. Without it, a rough check can be performed by holding
the instrument with the vane horizontal and placing a 3 gm weight
near the aft edge of the fin. Failure of the vane to rotate downward
indicates the bearings need replacement.
1. REMOVE MAIN HOUSING
a) Unscrew nose cone from main housing. Retain O-ring for
reuse.
b) Gently push main housing latch.
c) While pushing latch, lift main housing up and remove it from
vertical shaft bearing rotor.
2. UNSOLDER TRANSDUCER WIRES
a) Remove junction box cover.
b) Remove 3 screws holding circuit board.
c) Unsolder transducer wires from circuit board. 9 wires
attach at upper edge of board, 1 wire attaches at bottom
near cable terminals.