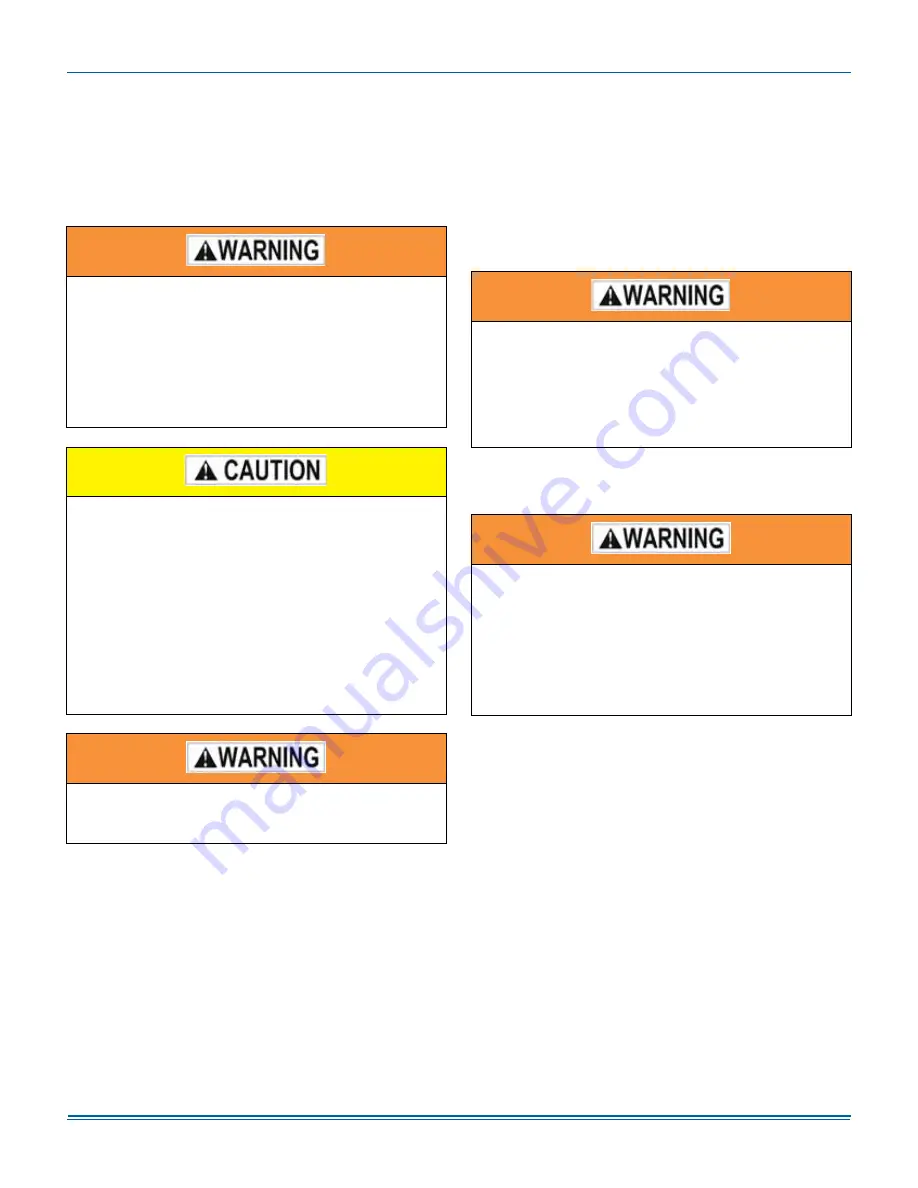
6021980-UIM-A-1120
Johnson Controls Ducted Systems
37
• You must install a 1/8-inch NPT plugged tapping,
accessible for test gage connection, immediately
upstream of the gas supply connection to the unit.
• After the gas connections are complete, open the main
shut-off valve admitting
normal gas pressure
to the mains.
Check all joints for leaks with soap solution or other
material suitable for the purpose.
Never use a flame.
LP units, tanks and piping
All gas heat units are shipped from the factory equipped for
natural gas use only. The unit may be converted in the field for
use with LP gas with accessory kit model numbers 1NP0454 or
1NP0455.
All LP gas equipment must conform to the safety standards of
the National Fire Protection Association.
For satisfactory operation, LP gas pressure must be 10.5 inch
W.C. at the unit under full load. Maintaining proper gas
pressure depends on three main factors:
• The vaporization rate which depends on the temperature
of the liquid and the wetted surface area of the containers.
• The proper pressure regulation. Two-stage regulation is
recommended.
• The pressure drop in the lines between regulators and
between the second stage regulator and the appliance.
The pipe size required depends on the length of the pipe
run and the total load of all appliances.
Complete information regarding tank sizing for vaporization,
recommended regulator settings, and pipe sizing is available
from most regulator manufacturers and LP gas suppliers.
Check all connections for leaks when the piping is completed
using a soap solution.
Never use a flame.
Vent and combustion air
Venting slots in the heating compartment access panel remove
the need for a combustion air hood. The gas heat flue exhaust
is routed through the factory-installed exhaust piping with a
screen. If necessary, a flue exhaust extension may be installed
at the point of installation.
Options and accessories
Electric heat
Electric heaters are available as factory-installed options or
field-installed accessories. Refer to the electric heat instructions
for installation. These heaters mount in the heat compartment
with the heating elements extending into the supply air
chamber. All electric heaters are fused and intended for use
with single point power supply.
Fire or explosion hazard
Failure to follow the safety warning exactly could result
in serious injury, death, or property damage.
Never test for gas leaks with an open flame. Use a
commercially available soap solution made specifically
for the detection of leaks to check all connections. A fire
or explosion may result causing property damage,
personal injury, or loss of life.
The furnace and its individual shut-off valve must be
disconnected from the gas supply piping system during
any pressure testing at pressures greater than 1/2
PSIG.
Pressures greater than 1/2 PSIG cause gas valve
damage resulting in a hazardous condition. If the gas
valve is subjected to a pressure greater than 1/2 PSIG, it
must be replaced.
The furnace must be isolated from the gas supply piping
system by closing its individual manual shut-off valve
during any pressure testing of the gas supply piping
system at test pressures equal to or less than 1/2 PSIG.
Threaded joints must be coated with a sealing
compound that is resistant to the action of liquefied
petroleum gases.
Do not use Teflon tape.
LP gas is an excellent solvent and quickly dissolves white
lead and most standard commercial compounds. A
special pipe dope must be used when assembling
wrought iron or steel pipe for LP. Shellac base
compounds such as Gaskolac or Stalastic, and
compounds such as Rectorseal #5, Clyde’s, or John
Crane may be used.
Fire or explosion hazard
Failure to follow the safety warning exactly could result
in serious injury, death, or property damage.
Never test for gas leaks with an open flame. Use a
commercially available soap solution made specifically
for the detection of leaks to check all connections. A fire
or explosion may result causing property damage,
personal injury, or loss of life.