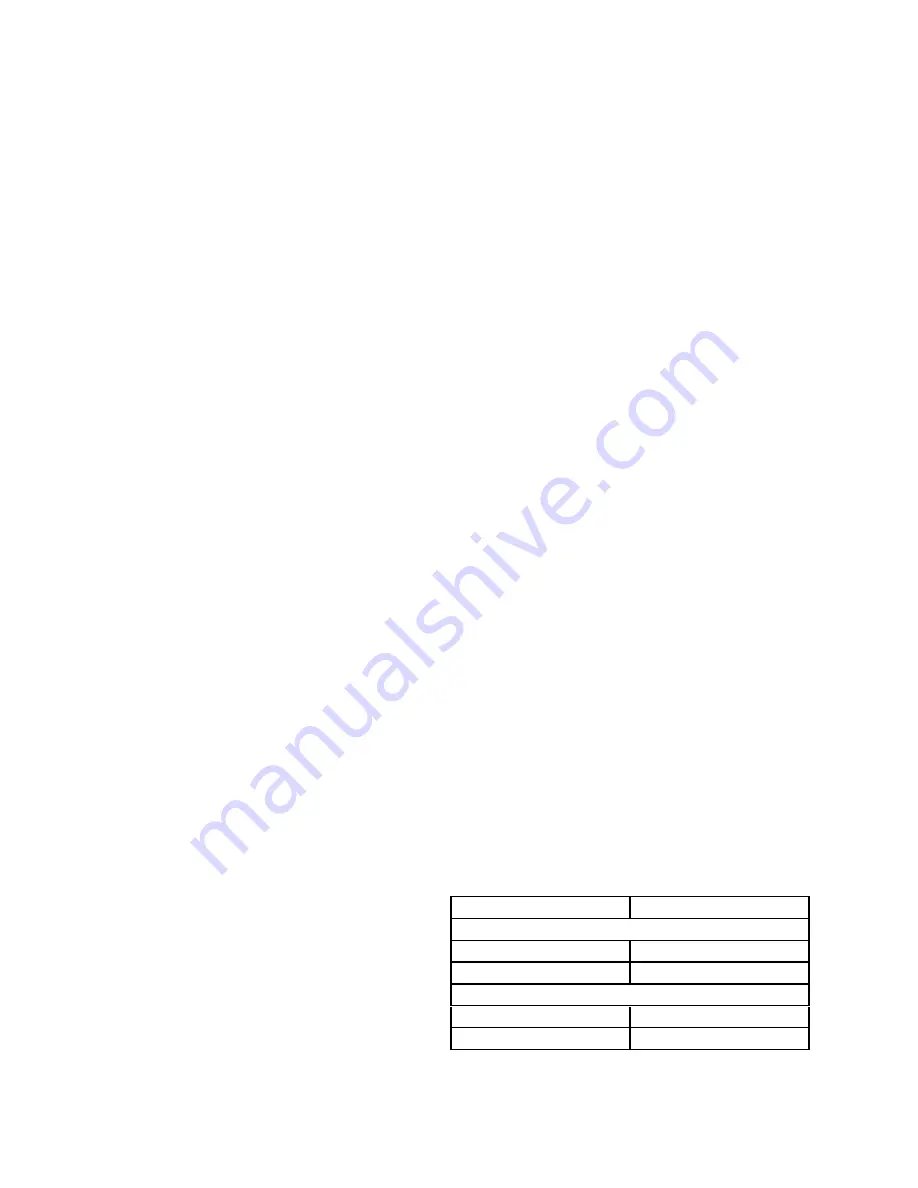
JOHNSON CONTROLS
68
FORM 160.67-O2
ISSUE DATE: 10/9/2020
SECTION 4 - OPERATIONAL MAINTENANCE
Establish an oil change frequency based on oil tests.
Otherwise, the oil reservoir should be drained and
cleaned yearly; or earlier, if there is reason to believe
that the oil has been contaminated with water, dirt, or
by overheating.The basic turbine oil for new units is
a #32 which has an average viscosity of 162 SSU @
100
°
F. If there are any doubts about the particular oil
for turbine use, consult the YORK Service Department.
Lube Oil Flushing
If the lube system has been contaminated, the oil should
be changed and the entire system should be flushed. To
do this, remove the upper half of the bearing housing,
remove the upper half of both bearings to allow for
more volume of oil to flow during the flush. Reseal the
upper bearing housing cover and replace the bolting.
The following steps should be followed:
1.
Install 100 mesh plain weave (.0059 opening)
screen mesh ahead of all bearing cases.
2.
While viewing the TURBINE SCREEN on the
OptiView™ Control Center, use the Manual
Pump key and enable manual operation and allow
it to run for two hours. Using the Manual Pump
key on the TURBINE SCREEN, shut down the
pump and check all screens for particles. Screens
should not have any particles bigger than .01 inch
in diameter and show random distribution. No
metallic particles should be present. Flushing
should continue until screens show no more than
6 non-metallic particles.
3. Replace screens with new ones and continue
flushing in one-hour intervals until no metallic
particles and no more than 6 non-metallic parti
-
cles are present on any of the screens.
4. Once clean screens are present, remove all
screens, service the turbine bearings and replace
them in the bearing housing. Housings must be
cleaned and resealed with Tite-Seal to prevent oil
leaks at the case split line.
5. Check the condition and cleanliness of the oil fil
-
ters furnished on the set and replace them with
new filters if needed before continuing with the
start up.
DETERMINING CORRECT REFRIGERANT
CHARGE LEVEL
The refrigerant charge level is correct when the mea-
sured evaporator approach and discharge refrigerant
gas superheat are within the values listed in
IMPORTANT:
The chiller must be at design operating
conditions and full load operation before the correct re-
frigerant charge level can be properly determined.
Liquid refrigerant will be visible in the evaporator
sight glass. The refrigerant level cannot be properly
determined by viewing the liquid refrigerant level in
the evaporator sight glass.
All YST Chillers shipped Form 1 are charged with the
correct amount of refrigerant. Under some operating
conditions the chiller may appear to be overcharged or
undercharged with refrigerant. Consult with the YORK
Factory prior to removing or adding refrigerant. The
liquid line isolation valve may have to be partially
throttled to prevent overfeeding the evaporator in some
applications and under certain operating conditions.
Definitions:
Evaporator Approach = (S.E.T) - (L.E.L.T)
Discharge Superheat = (C.D.G.T) - (S.C.T)
Where:
S.E.T. = Saturated Evaporator Temperature
L.E.L.T. = Leaving Evaporator Liquid Temp.
C.D.G.T. = Compressor Discharge Gas Temp.
S.C.T. = Saturated Condensing Temperature
These values can be obtained from the OptiView™
Control Center. Refer to OptiView™ Control Center
Operation Manual, Form 160.67-O1.
TABLE 2 -
REFRIGERANT CHARGE LEVEL
CONDITION
R-134A REFRIGERANT
COMFORT COOLING APPLICATIONS
Evaporator Approach
1°F-5°F
Discharge Superheat
12°F-18°F
BRINE (ICE MAKING) APPLICATIONS
Evaporator Approach
4°F-8°F
Discharge Superheat
24°F-36°F