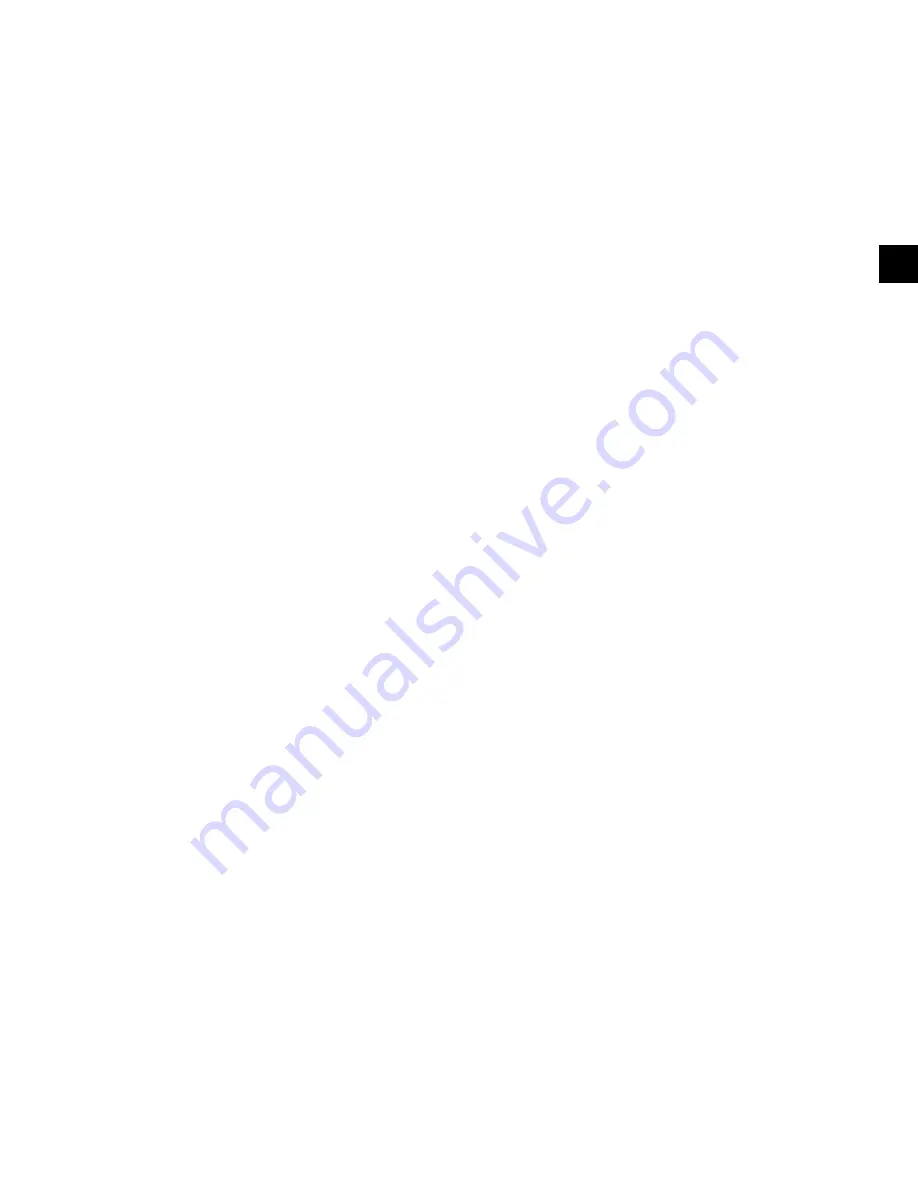
JOHNSON CONTROLS
67
SECTION 4 - OPERATIONAL MAINTENANCE
FORM 160.67-O2
ISSUE DATE: 10/9/2020
4
Establish an oil change frequency based on oil tests.
Otherwise, oil in bearing housings should be changed
monthly; or earlier, if there is reason to believe that the
oil has been contaminated with water, dirt, or by over-
heating. The basic turbine oil for new units is a #68
which has an average viscosity of 319 SSU @ 100°F.
If there are any doubts about the particular oil for tur-
bine use, consult the YORK Service Department.
Pressure Lubrication
Turbines supplied with pressure lubrication consist of
a main oil pump powered by the turbine shaft and a
motor driven auxiliary oil pump. Both pumps draw oil
from the oil reservoir that is an integral part of the tur-
bine base. Pressure relief valves are used in the pres-
sure lubricating system to control pressures through
the oil filter, oil cooler, piping, and auxiliary oil pump.
Always keep the proper oil level in the sight gauge.
The system must supply continuous lubrication to all
contact surfaces. THE OIL LEVEL SHOULD BE
CHECKED AT LEAST ONCE A DAY OR EVERY 8
HOURS IF THE TURBINE OPERATES 24 HOURS
A DAY. Normally, a small amount of oil (of the recom-
mended type and viscosity) should be added between
oil changes to maintain the proper oil level. Always use
a strainer when adding oil to the systems and cover the
fill connection when finished.
If an elevation in the oil level is observed in the sight
gauge when no oil has been added, water is probably
collecting in the oil. If an abnormal decrease is ob-
served, there are oil leaks in the system. If an unex-
plained rise or drop in oil level is observed in the sight
gauge, investigate immediately and stop the chiller if
necessary.
The tendency of oil to oxidize and deteriorate increases
with temperature. A rise in oil temperature also de-
creases viscosity, which progressively lowers the abil-
ity of oil to lubricate the turbine properly.
The operator should frequently observe the tempera-
tures at the inlet and outlet of the oil cooler. Any dras-
tic change should be investigated. Keeping a record of
temperatures is advisable since it provides a good base
for comparison.
Take readings from the pressure gauges every one
or two hours and investigate any change (gradual or
sudden). The most frequently encountered difficulty
is pressure drop, and the most common causes are
clogged oil filter, worn pump, faulty relief valves, in-
sufficient oil in the reservoir, clogged piping, entrained
air, and temperature elevation.
The most common sources of oil contamination are im-
purities picked up during storage, shipping, or adding
of the lubricant, dirt in the entrained air, water in the
oil reservoirs, leaks in the oil cooler, or condensation
of gland leakage.
Always use a strainer when adding oil to the systems
and cover the fill connection when finished. Make
sure the gland system works properly. For details, see
Turbine Gland Seal System on page 55
Water gives oil a milky appearance, and it has a ten-
dency to settle at the bottom of the reservoir when the
turbine is not running. If there is any reason to suspect
water in the oil, open the reservoir drain slightly. If
water is present, it will be the first thing to come out
of the drain.
The oil in the turbine should be inspected while the
equipment is standing idle. If the turbine operates con-
stantly, take a small sample of oil from the reservoir
and let it sit a few hours. If any water is present it will
settle to the bottom of the container.
The probability of oil contamination will increase if:
•
Gland seals are allowed to become excessively
worn, if obstructions are allowed to develop in
leak-off piping
• If the turbine is allowed to stand idle with back
pressure in the casing of a non-condensing tur-
bine.
• If there is too much sealing pressure on a condens-
ing turbine.
Care should be taken to avoid these conditions.
When oil is agitated it mixes with air and produces
foam. Foam inhibits the ability of oil to lubricate prop-
erly by reducing the oil pressure and causing excessive
wear of moving parts, rapid oil deterioration and oxi-
dation, and loss of oil through seepage. The problem is
usually solved with oil additives, lowering water flow
to the cooler and circulating the oil at a slightly higher
(not to exceed 120
°
) temperature, lowering the oil cir-
culation pressure (not less than 13 PSIG), and main
-
taining the proper oil level.
Sludge impairs oil circulation and causes oil tempera-
ture elevation, which accelerates oxidation and reduces
lubricant life. Any sludge should be removed as soon
as it is found. Using high quality oil and keeping the
system free of impurities can minimize sludge forma-
tion.