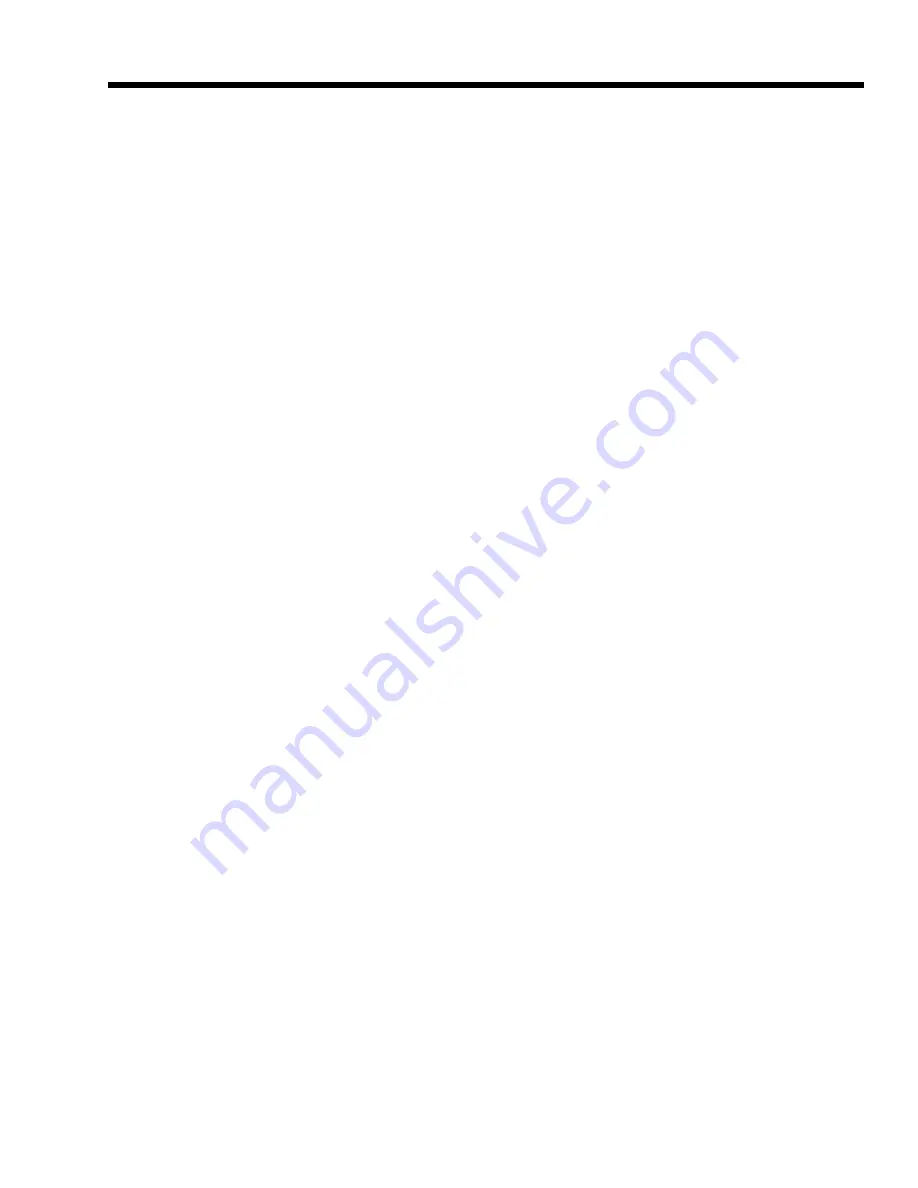
13
YORK INTERNATIONAL
FORM 160.81-EG1
Mechanical Specifications
GENERAL
Each YORK M
AX
E YR Screw Chiller will be completely
factory-packaged including evaporator, condenser, com-
pressor, motor, OptiView control center and all inter-
connecting unit piping and wiring. The chiller will be
painted prior to shipment and will be packaged to pro-
tect the unit during shipment.
Performance will be certified in accordance with ARI
Standard 550/590.
The initial charge of refrigerant and oil will be supplied
for each unit.
DRIVELINE
The compressor will be twin-screw, rotary-screw type.
The compressor housing will be of cast iron, precision
machined to provide minimal clearance for the rotors.
The rotors will be manufactured from forged steel and
use asymmetric profiles operating at a maximum speed
of 3570 RPM (60 Hz) or 2975 RPM (50 Hz). The com-
pressor will incorporate a complete anti-friction bearing
design to reduce power and increase reliability; cylin-
drical roller bearings to handle radial loads; and 4 point
angular contact ball bearings to handle axial loads. The
compressor will have an internal oil reservoir to assure
a constant supply of oil to the bearings at all times. A
check valve will be incorporated in the compressor hous-
ing to prevent rotor backspin during shutdown.
Capacity control will be achieved by use of a slide valve
to provide fully modulating control from 100% to 20%
of full-load. The slide valve will be actuated by system
differential pressure, controlled by external solenoid
valves through the OptiView control center. The unit
will be capable of operating with off-design cooling tower
water during part-load operation in accordance with ARI
Standard 550/590.
The motor will be 2-pole, continuous-duty, cage-induc-
tion type, and will utilize suction gas cooling (semi-her-
metic design). Motor full-load amperes at design condi-
tions will not exceed chiller nameplate (FLA). Motor will
be designed for use with the type starter specified.
LUBRICATION SYSTEM
An adequate supply of oil will be available to the com-
pressor at all times. During operation, oil will be deliv-
ered by positive system pressure differential.
An immersion oil heater will be provided, (temperature
actuated), to effectively remove refrigerant from the oil
during the chiller off-cycle. An external, replaceable car-
tridge, oil filter will be provided, along with manual isola-
tion stop valves for ease of servicing. An oil eductor will
be provided to automatically remove oil which may have
migrated to the evaporator, and return it to the compres-
sor. The oil separator will be of a vertical design with no
moving parts, and will provide high-efficiency oil separa-
tion before the refrigerant enters the heat exchangers.
The oil separator will be designed, tested, and stamped
in accordance with the ASME Boiler and Pressure Ves-
sel Code, Section VIII Division 1. Liquid refrigerant in-
jection will be provided to maintain satisfactory oil tem-
peratures and allow operation of the chiller over the full
range of conditions.
EVAPORATOR
Evaporator will be of the shell-and-tube, flooded type
designed for 235 PSIG (1620 kPa) working pressure on
the refrigerant side, and will be tested in accordance with
ASME code. The shell will be fabricated from rolled car-
bon steel plate with fusion welded seams or carbon steel
pipe; have carbon steel tube sheets, drilled and reamed
to accommodate the tubes; and intermediate tube sup-
ports spaced no more than four feet apart. The refriger-
ant side will be designed, tested and stamped in accor-
dance with the ASME Boiler and Pressure Vessel Code,
Section VIII Division 1. Tubes shall be high-efficiency,
internally and externally enhanced type having plain cop-
per lands at all intermediate tube supports to provide
maximum tube wall thickness at the support area. Each
tube will be roller expanded into the tube sheets provid-
ing a leak-proof seal, and be individually replaceable.
Water velocity through the tubes will not exceed 12 fps.
A liquid level sight glass will be located on the side of the
shell to aid in determining proper refrigerant charge. The
evaporator will have a refrigerant relief device to meet
the requirements of the ASHRAE 15 Safety Code for
Mechanical Refrigeration.
Water boxes will be removable to permit tube cleaning
and replacement. Stubout water connections having
victaulic grooves
will be provided. Vent and drain con-
nections with plugs will be provided on each water box.
CONDENSER
Condenser will be of the shell-and-tube type, designed
for 235 psig (1620 kPa) working pressure on the refrig-
erant side, and be tested in accordance with ASME code.
The shell will be fabricated from rolled carbon steel plate
with fusion welded seams or carbon steel pipe; have
carbon steel tube sheets, drilled and reamed to accom-
modate the tubes; and intermediate tube supports
spaced no more than four feet apart. A refrigerant
subcooler will be provided for improved cycle efficiency.
The refrigerant side will be designed, tested and
stamped in accordance with the ASME Boiler and Pres-