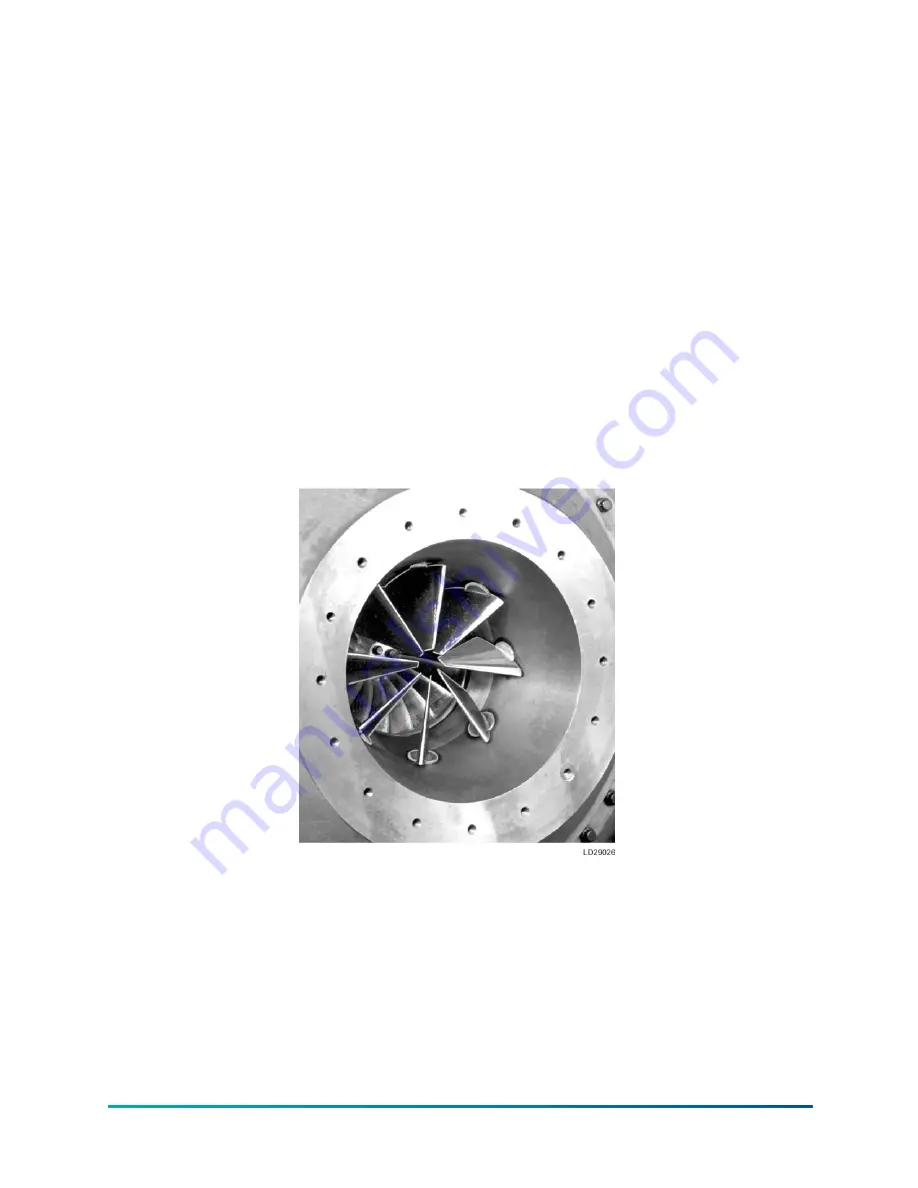
conditioning terminal units, where it flows through finned coils, absorbing heat from the air. The
warmed liquid is then returned to the chiller to complete the chilled liquid circuit.
The refrigerant vapor, which is produced by the boiling action in the cooler, flows to the
compressor where the rotating impeller increases its pressure and temperature and discharges it
into the condenser. Water flowing through the condenser tubes absorbs heat from the refrigerant
vapor, causing it to condense. The condenser water is supplied to the chiller from an external
source, usually a cooling tower. The condensed refrigerant drains from the condenser into the
liquid return line, where the variable orifice meters the flow of liquid refrigerant to the cooler to
complete the refrigerant circuit.
The major components of a chiller are selected to handle the refrigerant, which would be
evaporated at full load design conditions. However, most systems will be called upon to deliver full
load capacity for only a relatively small part of the time the unit is in operation.
Capacity control
The major components of a chiller are selected for full load capacities, therefore capacity must be
controlled to maintain a constant chilled liquid temperature leaving the cooler. Pre-rotation vanes
(PRV), located at the entrance to the compressor impeller, compensate for variation in load. See the
following figure.
Figure 3: Compressor pre-rotation vanes
The position of these vanes is automatically controlled through a lever arm attached to an electric
motor located outside the compressor housing. The automatic adjustment of the vane position in
effect provides the performance of many different compressors to match various load conditions
from full load with vanes wide open to minimum load with vanes completely closed.
13
Model YK Style H Centrifugal Liquid Chillers with OptiView Control Center