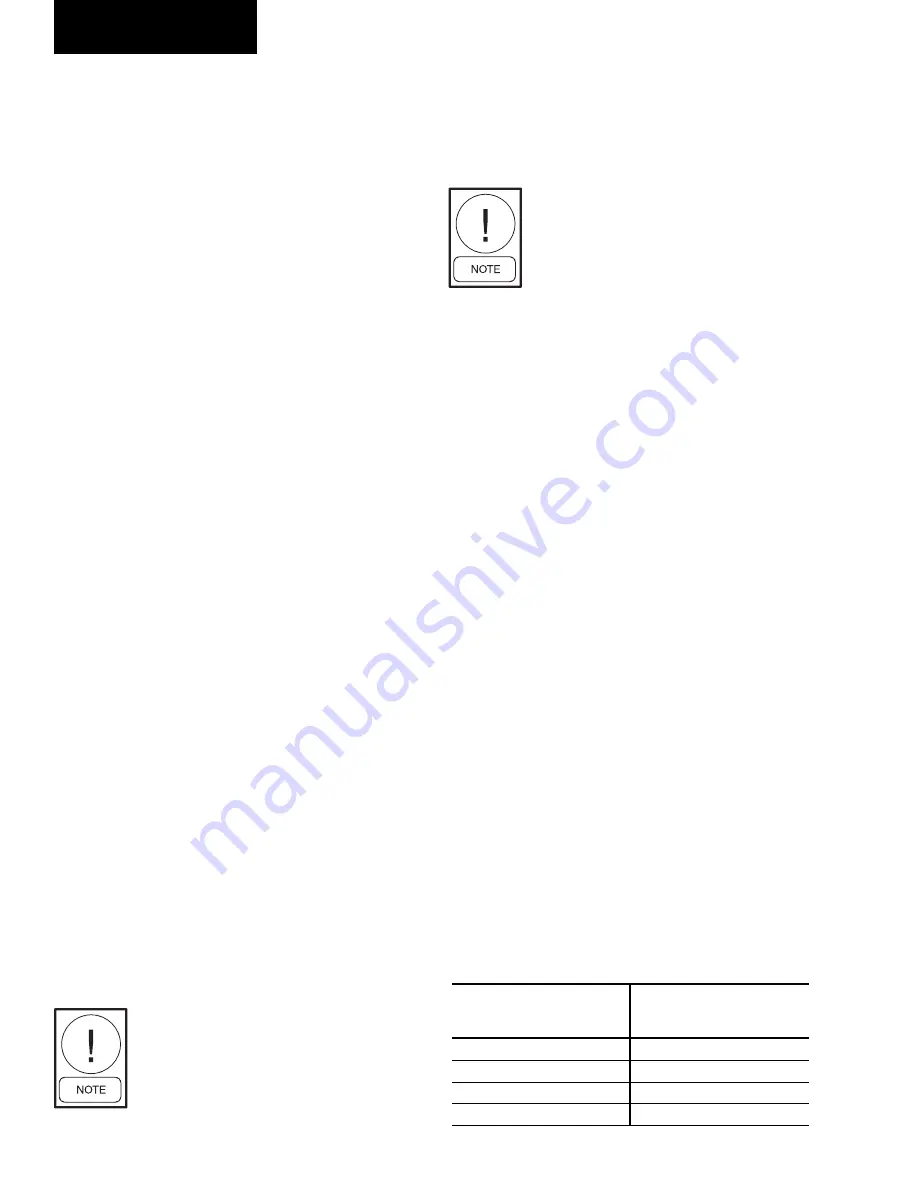
172
YORK INTERNATIONAL
FORM 201.19-NM8 (804)
Micro Panel Contents
Compressor Loading
The micro loads and unloads individual compressors
by varying voltage to the Slide Valve solenoid which
con trols oil fl ow to the slide valve. The slide valve load
solenoid applies oil pressure to the slide valve to over-
come spring pressure from an internal spring, in creas ing
ca pac i ty. The in ter nal spring moves the slide valve in
the op po site di rec tion against oil pres sure to de crease
ca pac i ty.
Whenever chilled liquid leaving temperature is above
the Setpoint plus the control range, loading voltage will
increase to allow oil pressure to push against the internal
slide valve return spring and move the slide valve to
increase capacity. Every 10 seconds, when the load timer
decrements to 0, the micro will increment the slide valve
step from 1 to 10 steps according to error (de vi a tion from
setpoint) and rate of change of chilled liquid.
The micro will always choose the compressor with the
lowest slide valve position to load on increasing de mand,
provided the compressor is not pumping down, has run at
least 15 seconds, and is not in a “Limiting” condition.
Compressor Unloading and Shutdown Sequence
Whenever temperature is below the Setpoint, minus the
control range, the voltage to the slide valve solenoid
will decrease, which bypasses oil pressure to the slide
valve allowing the slide valve return spring to move the
slide valve forward to the fully unloaded position on the
compressor with highest slide valve step. Ev ery 5 sec-
onds, the micro will dec re ment the compressor with the
highest slide valve po si tion by 1 - 10 steps ac cord ing to
the error (de vi a tion from Setpoint) and the rate of change
of chilled liquid tem per a ture until the temperature falls
within the control range.
As load drops, the micro will continue to unload the
com pres sor with the highest slide valve step until all
com pres sor slide valves are at “0.” At this point, the
last lag com pres sor will pump down and cycle off, if
chilled liq uid tem per a ture drops below “Setpoint - Con-
trol Range/2”. When the lag compressor cycles off,
the lead compressor slide valve will increment to step
30. As load con tin ues to decrease, the lead com pres sor
will con tin ue to unload to a slide valve po si tion of “0”
and will pump down and cy cle off if the chilled liq uid
tem per a ture drops below “Setpoint – Con trol Range.”
A lag compressor may be shut down
be fore it is fully unloaded to avoid a
Chill er fault on a Low Wa ter Tem-
per a ture cut-out under the fol low ing
conditions: a) if chilled liq uid tem-
per a ture falls below the low end of the
Con trol Range (CR) for more than 37
sec onds, b) if chilled liq uid tem per a-
ture drops more than CR/4 be low the
low lim it of the Con trol Range.
The lead compressor may be shut down
be fore it is fully unloaded to avoid a
Chill er Fault on Low Wa ter Tem per a-
ture un der the fol low ing con di tions:
a) if chilled liquid tem per a ture drops
2°F below the low lim it of the Con trol
Range (CR), b) if chilled liq uid tem-
per a ture drops more than CR/2 be low
the low lim it of the Con trol Range.
ANTICIPATORY LOAD LIMITING CONTROLS
The purpose of the Anticipatory Load Limiting controls
is to prevent the system from ever reaching a point where
the micro would be forced to unload a system to prevent
the system from reaching a safety threshold. This in
turn prevents cycling of the slide valve as the micro
would load and unload the system as system operating
pressures and temperatures move above and below the
forced unload point.
Anticipatory load limiting controls monitor motor cur-
rent, discharge pressure, and saturated suction tempera-
ture. When the system is called to load in an attempt
to satisfy chilled liquid temperature, the micro looks at
these three operating parameters and determines if any
are nearing the user programmed or internal micropro-
cessor unload threshold points programmed into the
micro panel. If the micro determines that the unload
points could be exceeded, it limits the steps of loading
or may decide not to provide any further loading of the
specifi c system, even though there is a need for addi-
tional cooling. No status display will be present when
anticipatory load limiting occurs.
In the case of both Motor Current and Discharge Pres-
sure, the micro limits loading as follows based on the
programmed unload point. These thresholds are out-
lined in the following table:
Percentage of Motor
Current or Discharge
Pressure Unload Point
Maximum Steps of
Loading After Load
Timer Counts to "0"
> 70 %
3
> 80 %
2
> 90 %
1
> 95 %
0
Summary of Contents for YCAS Series
Page 43: ...43 YORK INTERNATIONAL FORM 201 19 NM8 804 5 This page intentionally left blank...
Page 45: ...45 YORK INTERNATIONAL FORM 201 19 NM8 804 6 This page intentionally left blank...
Page 77: ...77 YORK INTERNATIONAL FORM 201 19 NM8 804 This page intentionally left blank...
Page 81: ...81 YORK INTERNATIONAL FORM 201 19 NM8 804 LD10047 035 16253 104 Rev D Power Panel...
Page 93: ...93 YORK INTERNATIONAL FORM 201 19 NM8 804 This page intentionally left blank...
Page 147: ...147 YORK INTERNATIONAL FORM 201 19 NM8 804 8 This page intentionally left blank...
Page 205: ...205 YORK INTERNATIONAL FORM 201 19 NM8 804 8 This page intentionally left blank...