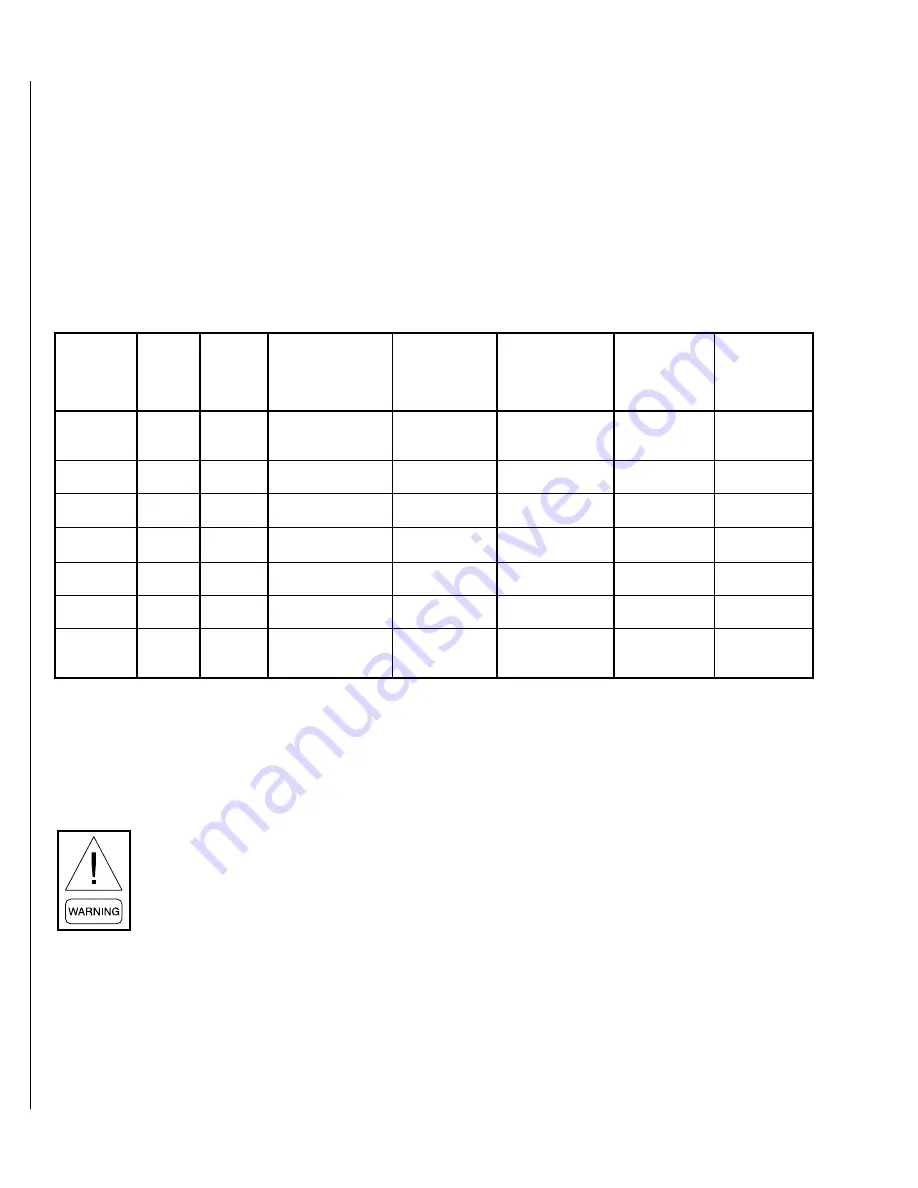
JOHNSON CONTROLS
32
FORM 160.76-O1
ISSUE DATE: 05/22/2019
SECTION 7 - PREVENTIVE MAINTENANCE
MOTOR RE-LUBRICATION INSTRUCTION
General
Johnson Controls supplied electric drive motors have
maintenance requirements for re-lubrication (greasing)
of the drive end (DE) and non-drive end (NDE) ball
bearings.
In recent years the type of grease to be utilized is typi-
cally identified on the motor data plate. Below, in
, we have provided a quick guide. How-
ever, always perform a verification with the motor data
plate - any differences between the quick guide and the
motor data plate must be communicated to the product
technical support (PTS) team prior to completing the
greasing application.
ANTI-
FRICTION/
BALL
BEARING
MOTOR
HOURS
TO
LUBE
MAX
SHAFT
IDLE
TIME
FRAME
PREFERRED
GREASE*
ALTERNATIVE
GREASE*
GREASE
QUANTITY
GREASE
METHOD
PREFERRED**
***ALTERNATE
GREASE
METHOD
WEG
2200
90 Days
Mobil Polyrex EM
N/A
See Manufacturer's
nameplate for ap-
plicable quantity
Operational > 5
mins
Operational
Toshiba
1000
90 Days
Mobil Polyrex EM
N/A
1.5 cubic inches
At rest
Operational
Teco
1000
90 Days
Mobil Polyrex EM
Chevron SRI-2
1.5 cubic inches
At rest
N/A
ABB
Per data
plate
90 Days
Kluberplex BEM41-
132
Mobilith SCH100
1.5 cubic inches
Operational
At rest
Ram
1000
90 Days
Mobil Polyrex EM
Chevron SRI-2
1.5 cubic inches
At rest
Operational
Reliance
1000
90 Days
Shell Alvania RL3
Mobilith SHC100
1.5 cubic inches
At rest
Operational
Siemens
1000
90 Days
See manufacturer's
nameplate for ap-
plicable grease
N/A
See manufacturer's
nameplate for ap-
plicable grease
At rest
N/A
TABLE 3 -
QUICK GUIDE TO MOTOR GREASING AND SHAFT ROTATION INTERVALS
* Never mix grease type or brand. If changing from or to the alternate or preferred, the bearing cavities, housings, and lines must be cleaned
of the old grease.
** Follow all standard lookout tag out procedures prior to greasing motor.
** After greasing motor at rest, run motor for a minimum of 45 minutes before replacing plug if equipped.
*** Motor must be equipped with grease extensions on DE bearing for performance of this task.
Verify with motor nameplate any discrepancy before lubricating - contact technical support for additional information/clarification.
Remove grease plug, if equipped, prior to greasing. Not every grease interval will result in used grease discharge.
Work on this equipment should only be done by properly trained personnel who are qualified to
work on this type of equipment. Failure to comply with this requirement could expose the worker,
the equipment, and the building and its inhabitants to the risk of injury or property damage.
The instructions in this document are written assuming the individual who will perform this work
is a fully trained HVAC and R journeyman or equivalent, certified in refrigerant handling and
recovery techniques, and knowledgeable with regard to electrical lock out/tag out procedures. The
individual performing this work must be aware of and comply with all Johnson Controls, national,
state, and local safety and environmental regulations while carrying out this work. Before attempt-
ing to work on any equipment, the individual should be thoroughly familiar with the equipment
by reading and understanding the associated service literature applicable to the equipment. If
you do not have this literature, you may obtain it by contacting a Johnson Controls service office.
Should there by any question concerning any aspect of the tasks outlined in this bulleti, please consult
a Johnson Controls service office prior to attempting the work. Please be aware that this information
may be time sensitive and that Johnson Controls reserves the right to revise at any time. Be certain
you are working with the latest information.