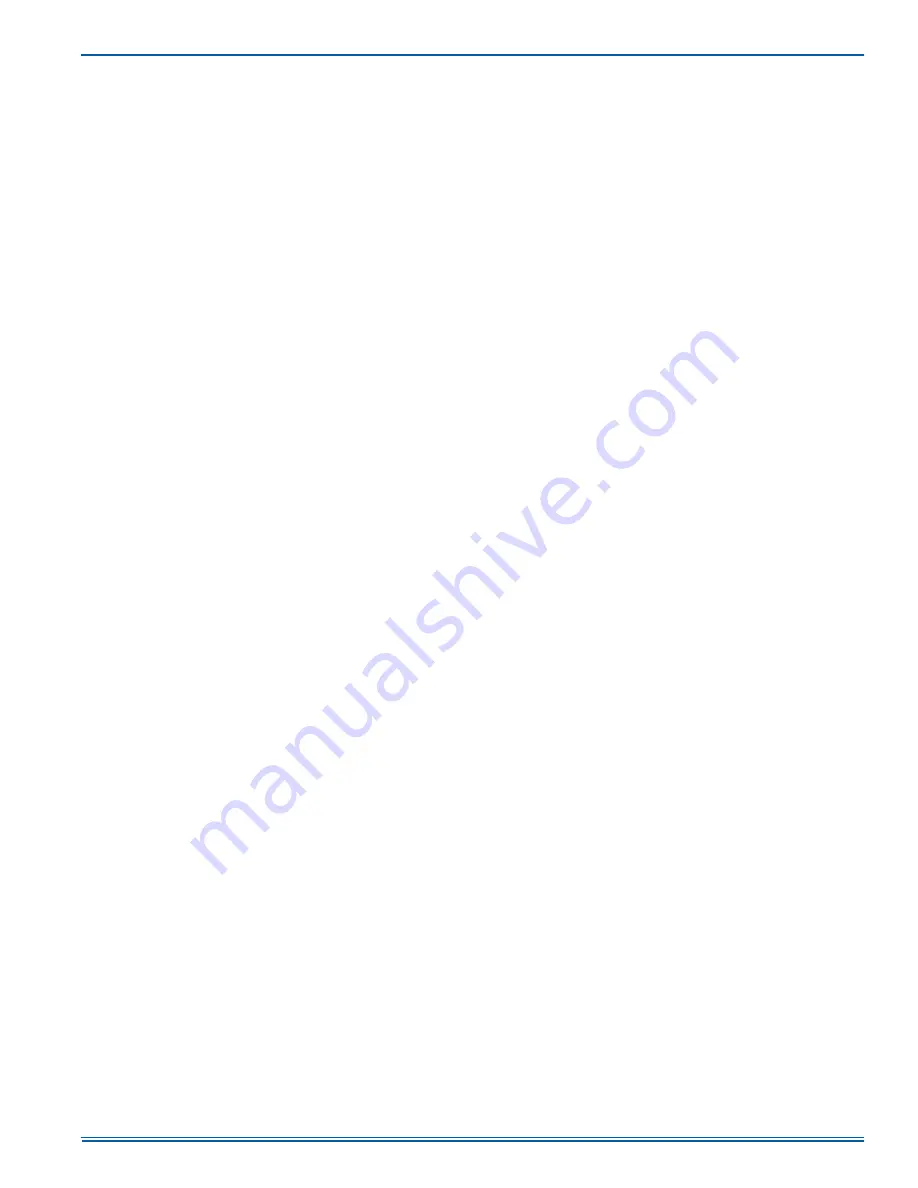
5322625-UIM-A-0417
Johnson Controls Unitary Products
21
Pre-purge
The control board monitors the pressure switch and ensures it remains
closed during pre-purge. If the pressure switch opens, the control goes
back to pressure switch proving mode. The control waits for a 15 sec-
ond pre-purge period, then begins the ignition trial.
Ignition Trial Period
The control board energizes the gas valve and spark outputs for a 5
second Ignition trial. The control de-energizes the spark when flame is
sensed and enters a flame stabilization period.
The unit control establishes flame in “HI HEAT” mode. If a call for heat-
ing is only present on the first stage heating (W1) input, the control
switches to first stage heat after 10 seconds of flame. If there is a heat
call on the first and second stage input (W1 + W2), the control remains
in high heat mode.
If flame is not established within the ignition trial period, the control de-
energizes the spark and gas valve and begins an inter-purge period
before attempting another ignition trial.
If the call for heat is removed during an ignition trial period, the control
immediately de-energizes spark and gas. The control runs the inducer
motor through a post purge period before de-energizing.
If the pressure switch opens during an ignition trial period, the control
immediately de-energizes spark and gas. The control begins pressure
switch proving before an inter-purge and reignition attempt.
Heat Blower On Delay
The control board waits for 30 seconds and then energizes the indoor
blower heat speed. The indoor blower heat speed is based on the
“HEAT” airflow selection jumper, and the low heating (W1) or the high
heating (W1 + W2) input.
Blower on delay time begins at the start of flame proving period in the
trial for ignition.
If the thermostat demand for heat is removed, the control de-energizes
the gas valve, energizes the blower on heat speed and initiates a post
purge and heat blower off delay.
Main Burner Operation
The control board keeps the main gas valve and induced draft motor
energized while continuously monitoring the call for heat, pressure
switch and flame status.
If the call for heat (W1) is removed, the control de-energizes the gas
valve and begins the post purge and heat blower off delay.
If a call for low fire heat (W1) is present and a call for high stage heat
(W2) is removed, the control is staged down to low fire heat. The control
is staged back up to high fire heat if the high stage heat (W2) call is re-
applied to the control. During normal operation if the control is operating
the unit in low stage heat, the control is switched to high fire heat any
time a call for high stage heat (W2) is applied to the control regardless
of the setting on the “HI HEAT DELAY” jumper.
If the pressure switch opens, the control de-energizes the gas valve
and begins pressure switch proving mode.
If flame is removed, the control de-energizes the gas valve within 2 sec-
onds and counts the flame loss. If flame has been lost less than 5 times,
the control attempts re-ignition after a 15 second inter-purge period. If
flame has been lost more than 5 times within the same call for heat, the
control board locks out, and flashes a sequence of “8” times on the
LED.
Post Purge
The control board runs the induced draft motor for a 15 second post
purge period and then de-energizes the inducer. If a call for heat occurs
during post purge, the control finishes the post purge and immediately
begins the next ignition sequence.
Heat Blower Off Delay
After a heating sequence, the control board de-energizes the indoor
blower motor after a delay time as selected by a movable shunt (60, 90,
120 or 180 seconds). Blower off timing begins when the thermostat is
satisfied and removes the (W1) call for heat. The control returns to
standby when the blower off delay is complete.
If the thermostat call for heat returns before the blower off delay is com-
plete, the control begins an ignition sequence with pre-purge while the
blower off delay continues.
Lockout
While in lockout, the control board keeps the main gas valve and
induced draft motor de-energized.
Lockouts due to failed ignition or flame losses may be reset by remov-
ing the call for heat (W1) for more than 1 second, or by removing power
from the control for over 0.25 second. The control automatically resets
from lockout after 60 minutes.
Lockouts due to detected internal control faults reset after 60 minutes or
power interruption. Cooling operations are available during a heating
lockout.
High Temperature Limit Switch
Any time the high temperature limit switch is open less than 5 minutes,
the control board runs the indoor blower motor on high heat speed, runs
the inducer, de-energizes the gas valve, and flashes a sequence of “4”
times on the LED. When the high temperature switch closes, the control
restarts the ignition sequence beginning with pre-purge.
If the limit switch has been open more than 5 minutes the control de-
energizes the inducer, continues to operate the indoor blower motor on
heat speed, and flashes a sequence of “11” times on the LED.
Rollout Switch
If the limit circuit is open for more than 15 minutes, the control board
flashes a sequence of “5” times on the LED. The blower output ener-
gizes on high heat speed during an open rollout condition.
The rollout switch used is a manual reset switch.
If the rollout switch is reset, the control remains locked out until power is
removed or a call for heat (W) is removed.
Rollout switch lockout does not reset automatically.
Power Interruptions
Power interruptions of any duration do not cause lockout or any opera-
tion requiring manual intervention.
Flame present with Gas off
If flame is sensed for longer than 4 seconds during a period when the
gas valve should be closed, the control enters a lockout flashing a
sequence of “1” time on the LED. The control energizes the inducer
blower while the flame is sensed.