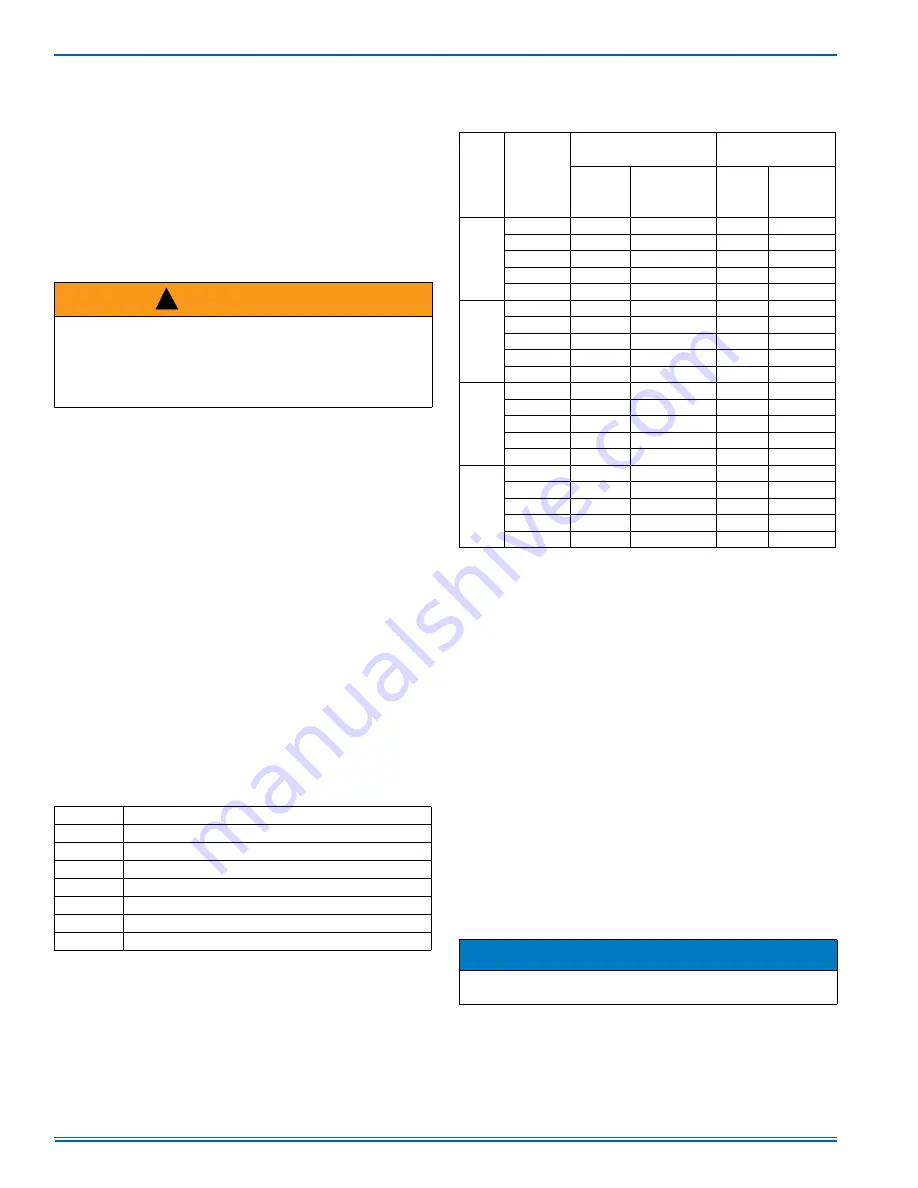
5285477-UIM-A-1016
14
Johnson Controls Unitary Products
Dehumidification/Humidity Switch Input
This model unit features a built in de-humidification feature for
advanced dehumidification during cooling operation. The unit indoor
blower control is designed to work with a humidity control that closes
when the humidity is below the set-point. The control is open when the
humidity is above the set-point. This humidity control may be referred to
as a humidistat or dehumidistat.
To use this feature, the control HUM STAT jumper must be set to YES
and a humidistat is connected from the low voltage R and HUM color
coded leads. During cooling operation if the humidity level is above the
humidistat set point, the indoor blower speed is reduced by approxi-
mately 15%.
Safety Controls
The control circuit includes the following safety controls:
High Pressure Switch (HPS) -
The switch protects against excessive
discharge pressures and the defrost control locks out compressor oper-
ation.
Loss of Charge Switch (LCS) -
The switch protects against loss of
charge due to a leak in the system.
The above pressure switch is specifically designed to operate with R-
410A systems. R-22 pressure switches must not be used as replace-
ments for the R-410A pressure switches.
Indoor Circulating Blower
When the thermostat calls for “FAN,” the thermostat terminal “G” is
energized signaling the indoor blower control board to operate the cir-
culating blower to run continuously.
If a call for “COOL” occurs on “Y1,” the indoor blower runs at the “LOW
COOL” speed based on the “COOL” jumper setting. If a call for cool is
present on “Y1”+”Y2,” the indoor blower runs at the “HIGH COOL”
speed based on the “COOL” jumper setting.
If a call for “HEAT” occurs “W1” or “W1”+“W2”, the circulating blower
runs at the heat speed based on the “HEAT” jumper setting.
When the thermostat ends the call for “FAN,” the thermostat terminal
“G” is de-energized, and the indoor blower control board stops the cir-
culating blower operation.
Delay Profiles
The Delay Profiles for each Delay jumper setting are shown in Table 16.
The levels shown in the Pre-Run, Short-Run, and Run Periods are a
percentage of the fan speed corresponding to the thermostat call. The
Post-Run and Off Delay levels are derived from the level of the previous
state, not the fan speed corresponding to the thermostat call. If in Delay
Profile B and in the Short-Run Period (82% of capacity) and the thermo-
stat call is removed, this causes control to enter the Post-Run state.
The Post-Run state level for Delay Profile B is 100% of the previous
level, so the level during the Post-Run state is 82%.
HEATING SEQUENCE OF OPERATION
1.
On a call for heating, the thermostat sends 24 volts to “Y1” or
“Y1”+“Y2” on the defrost control board. After the anti-short cycle
period is complete, the 24 volt signal from “Y1” energizes contactor
coil “M” to supply power for the compressor and outdoor fan motor.
The indoor blower control operates the indoor blower motor at the
“LOW COOL” speed. If the 24 volt signal from “Y2” is present, the
defrost control board energizes the 2nd stage compressor solenoid
and signals the indoor blower control to operate the indoor blower
motor at the “HIGH COOL” speed. The reversing valve remains in
the heating position. Indoor blower speeds are selected by the
“COOL” jumper on the indoor blower control board.
2.
If the heat pump cannot meet the heating demand using mechanical
(compressor) heating, the indoor thermostat may energize axillary
(electric) heating to supplement the mechanical heating if an electric
heat kit was field installed. The room thermostat sends a 24 VAC sig-
nal on “W1” or “W1”+“W2.” The “W1” signal is received by the indoor
blower control board which then energizes the “HT1” output for elec-
tric heat. When a call for mechanical heating and supplemental heat-
ing is present, the indoor blower control operates the indoor blower at
either the “Y1”+”Y2” or the “W1” speed whichever is higher based on
the “COOL” and “HEAT” jumper selection.
A 2
nd
stage auxiliary electric heating “W2” from the thermostat is to
be wired directly to the second stage heat kit input.
WARNING
The ability to properly perform maintenance on this equipment
requires certain expertise, mechanical skills, tools and equipment. If
you do not possess these, do not attempt to perform any mainte-
nance other than those procedures recommended in this Installation
Manual. Failure to heed this warning could result in serious injury
and possible damage to this equipment.
Table 15:
Indoor Blower Control Fault Codes
Flashes
Fault Condition
LAMP OFF No Power to control
LAMP ON Internal control failure
SLOW RED Control normal operation
RAPID RED Test Mode
7 RED
Call for heat and cool at the same time
8 RED
Model ID plug not inserted
9 RED
Internal fault self corrected, attempting normal operation
!
TABLE 16 : Delay Profile Descriptions
Delay
Profile
Period
Cooling
Heat Pump
Heating
Level%
Time in State
(Minutes)
Level%
Time in
State
(Minutes)
A
Pre-Run
Bypass
Bypass
Bypass
Bypass
Short-Run
Bypass
Bypass
Bypass
Bypass
Run
100
No Limit
100
No Limit
Post-Run*
100
1
100
.5
Off Delay*
Bypass
Bypass
Bypass
Bypass
B
Pre-Run
50
2
Bypass
Bypass
Short-Run
82
5
Bypass
Bypass
Run
100
No Limit
100
No Limit
Post-Run*
100
1
100
.5
Off Delay*
Bypass
Bypass
Bypass
Bypass
C
Pre-Run
Bypass
Bypass
Bypass
Bypass
Short-Run
Bypass
Bypass
Bypass
Bypass
Run
100
No Limit
100
No Limit
Post-Run*
100
1
100
.5
Off Delay*
50
1
Bypass
Bypass
D
Pre-Run
Bypass
Bypass
Bypass
Bypass
Short-Run
63
1.55
Bypass
Bypass
Run
100
No Limit
100
No Limit
Post-Run*
100
1
100
.5
Off Delay*
63
0.5
Bypass
Bypass
*The Post-Run and Off Delay levels are derived from the level of the
previous state, not the fan speed corresponding to the thermostat
call.
NOTICE
The “W1” must be energized with “W2” in order to enable indoor air
flow.