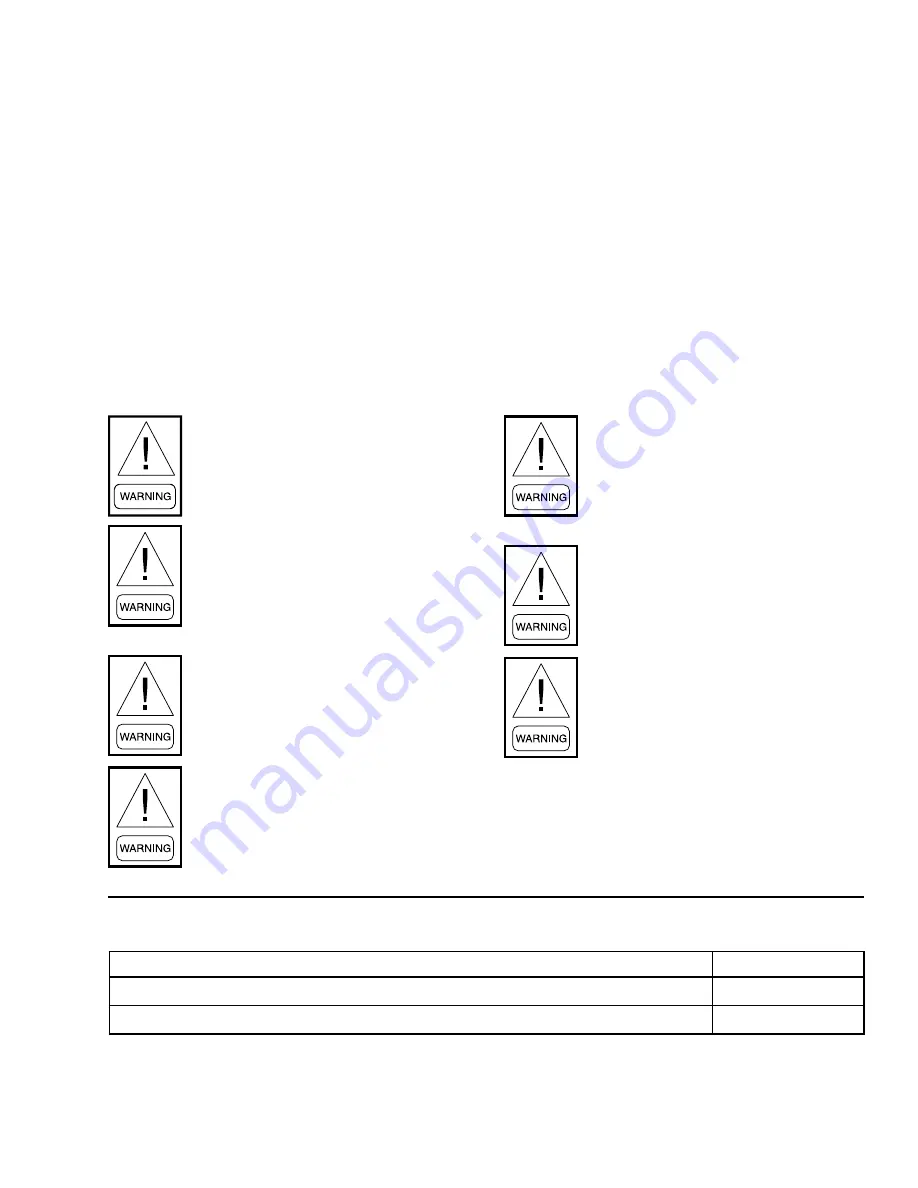
JOHNSON CONTROLS
3
FORM 201.28-N1
ISSUE DATE: 7/25/2017
CHANGEABILITY OF THIS DOCUMENT
In complying with Johnson Controls’ policy for con-
tinuous product improvement, the information con-
tained in this document is subject to change without
notice. Johnson Controls makes no commitment to
update or provide current information automatically
to the manual or product owner. Updated manuals, if
applicable, can be obtained by contacting the nearest
Johnson Controls Service office or accessing the John-
son Controls QuickLIT website at
.
It is the responsibility of rigging, lifting, and operating/
service personnel to verify the applicability of these
documents to the equipment. If there is any question
regarding the applicability of these documents, rig-
ging, lifting, and operating/service personnel should
verify whether the equipment has been modified and
if current literature is available from the owner of the
equipment prior to performing any work on the chiller.
CHANGE BARS
Revisions made to this document are indicated with a
line along the left or right hand column in the area the
revision was made. These revisions are to technical in-
formation and any other changes in spelling, grammar
or formatting are not included.
The Control/VSD Cabinet contains lethal
high AC and DC voltages. Before per-
forming service inside the cabinet, remove
the AC supply feeding the chiller and
verify using a non-contact voltage sensor.
The DC voltage on the VSD DC Bus will
take 5 minutes to bleed off, after AC
power is removed. Always check the DC
Bus Voltage with a Voltmeter to assure
the capacitor charge has bled off before
working on the system.
NEVER short out the DC Bus to dis-
charge the filter capacitors.
NEVER place loose tools, debris, or any
objects inside the Control Panel/VSD
Cabinet.
NEVER allow the Control Panel VSD
Cabinet doors to remain open if there is
a potential for rain to enter the panel.
Keep doors closed and assure all latches
are engaged on each door unless the unit
is being serviced.
ALWAYS lockout the disconnect supply-
ing AC to the chiller.
The 1L Line Inductor will reach operating
temperatures of over 150°C (300°F.) DO
NOT open panel doors during operation.
Assure the inductor is cool whenever
working near the inductor with power
OFF.
ASSOCIATED LITERATURE
MANUAL DESCRIPTION
FORM NUMBER
Equipment Pre-Startup and Startup Checklist
201.28-CL2
Installation, Operation and Maintenance
201.28-NM1.1