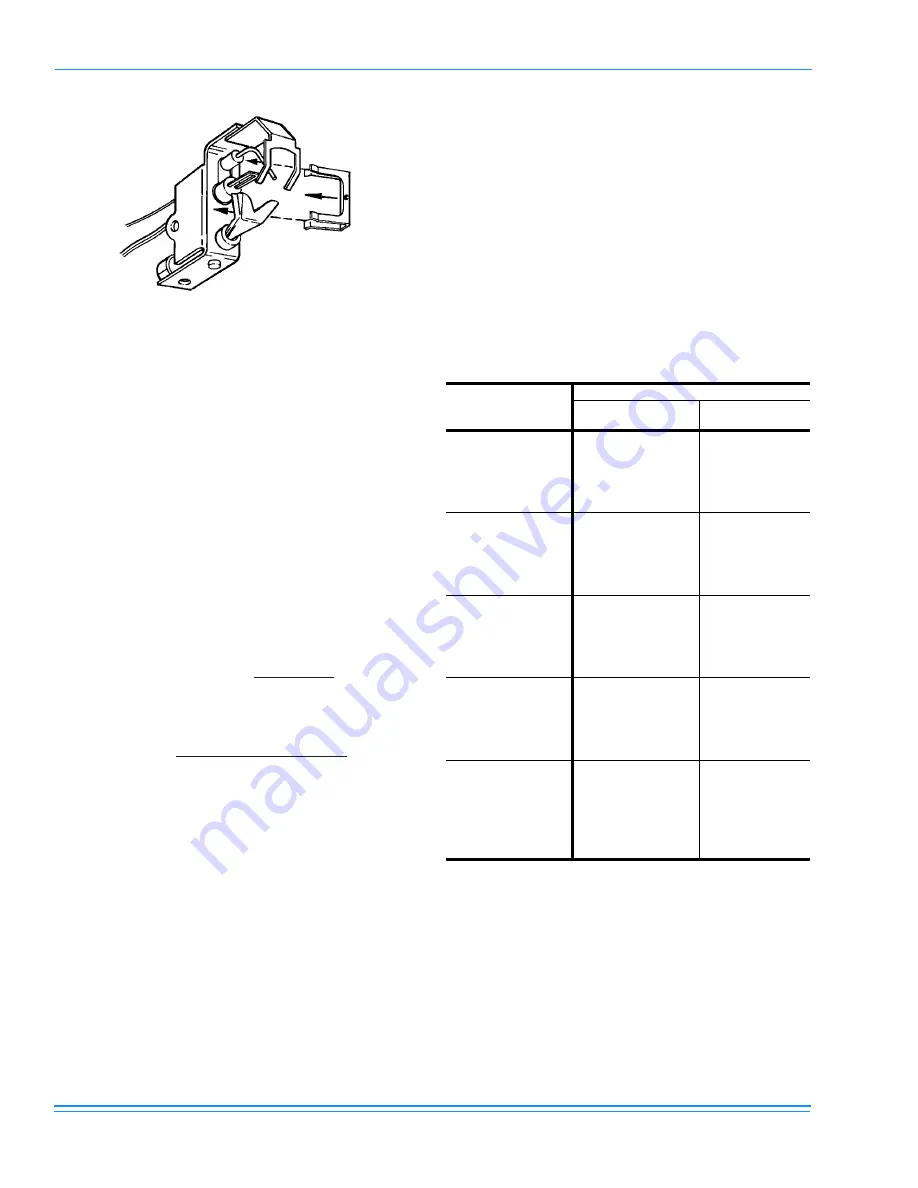
66433-YIM-B-1004
18
Unitary Products Group
2.
Lift the pilot and sensor from the assembly. Care must be
taken not to damage the pilot or sensor when removing
this assembly.
ADJUSTMENT OF TEMPERATURE RISE
After about 20 minutes of operation, determine the furnace
temperature rise. Take readings of both the return air and the
heated air in the ducts about six feet from the furnace where
they will not be affected by radiant heat.
The temperature rise (or temperature difference between the
return air and the heated air from the furnace) must lie within
the range shown on the rating plate and the data in Tables 3
and 4.
After the temperature rise has been determined, the CFM can
be calculated as follows:
DIRECT DRIVE BLOWER
All units have direct drive, constant CFM blower motors.
Refer to the Unit Wiring Diagram Table 1 for the desired cool-
ing CFM. Heating CFM is preset at the factory.
CHECKING GAS INPUT
NATURAL GAS
1.
Turn off all other gas appliances connected to the gas
meter.
2.
With the furnace turned on, measure the time needed for
one revolution of the hand on the smallest dial on the
meter. A typical gas meter usually has a 1/2 or a 1 cubic
foot test dial.
3.
Using the number of seconds for each revolution and the
size of the test dial increment, find the cubic feet of gas
consumed per hour from Table 11.
If the actual input is not within 5% of the furnace rating with
allowance being made for the permissible range of the regu-
lator setting, replace the orifice spuds with spuds of the
proper size.
NOTE:
To find the BTU input, multiply the number of cubic
feet of gas consumed per hour by the BTU content
of the gas in your particular locality. (Contact your
gas company for this information since it varies
widely from city to city.)
FIGURE 12 - IGNITOR AND FLAME SENSOR
ASSEMBLY
Degrees F Temp Rise =
BTUH Output
1.08 x CFM
OR
CFM =
BTUH Output
1.08 x Degrees F Temp Rise
TABLE 11: GAS RATE - CUBIC FEET PER HOUR
1
1.
EXAMPLE
: By actual measurement, it takes 38 sec-
onds for the hand on the 1-cubic foot dial to make a
revolution with just a 100,000 BTUH furnace running.
Using this information, locate 38 seconds in the first
column of Table 11. Read across to the column headed
“1 Cubic Foot,” where you will see that 95 cubic feet of
gas per hour are consumed by the furnace at that rate.
Multiply 95 x 1050 (the BTU rating of the gas obtained
from the local gas company). The result is 99,750
BTUH, which is close to the 100,000 BTUH rating of
the furnace.
SECONDS
FOR ONE
REV.
SIZE OF TEST DIAL
1/2 CU. FT.
1 CU. FT.
10
180
360
12
150
300
14
129
257
16
113
225
18
100
200
20
90
180
22
82
164
24
75
150
26
69
138
28
64
129
30
60
120
32
56
113
34
53
106
36
50
100
38
47
95
40
45
90
42
43
86
44
41
82
46
39
78
48
37
75
50
36
72
52
35
69
54
34
67
56
32
64
58
31
62
60
30
60
Summary of Contents for DNZ 060
Page 20: ...66433 YIM B 1004 20 Unitary Products Group FIGURE 13 TYPICAL WIRING DIAGRAM DNZ 208 230 1 60...
Page 21: ...66433 YIM B 1004 Unitary Products Group 21 FIGURE 14 TYPICAL WIRING DIAGRAM DNZ 208 230 3 60...
Page 22: ...66433 YIM B 1004 22 Unitary Products Group FIGURE 15 TYPICAL WIRING DIAGRAM DNZ 460 3 60...