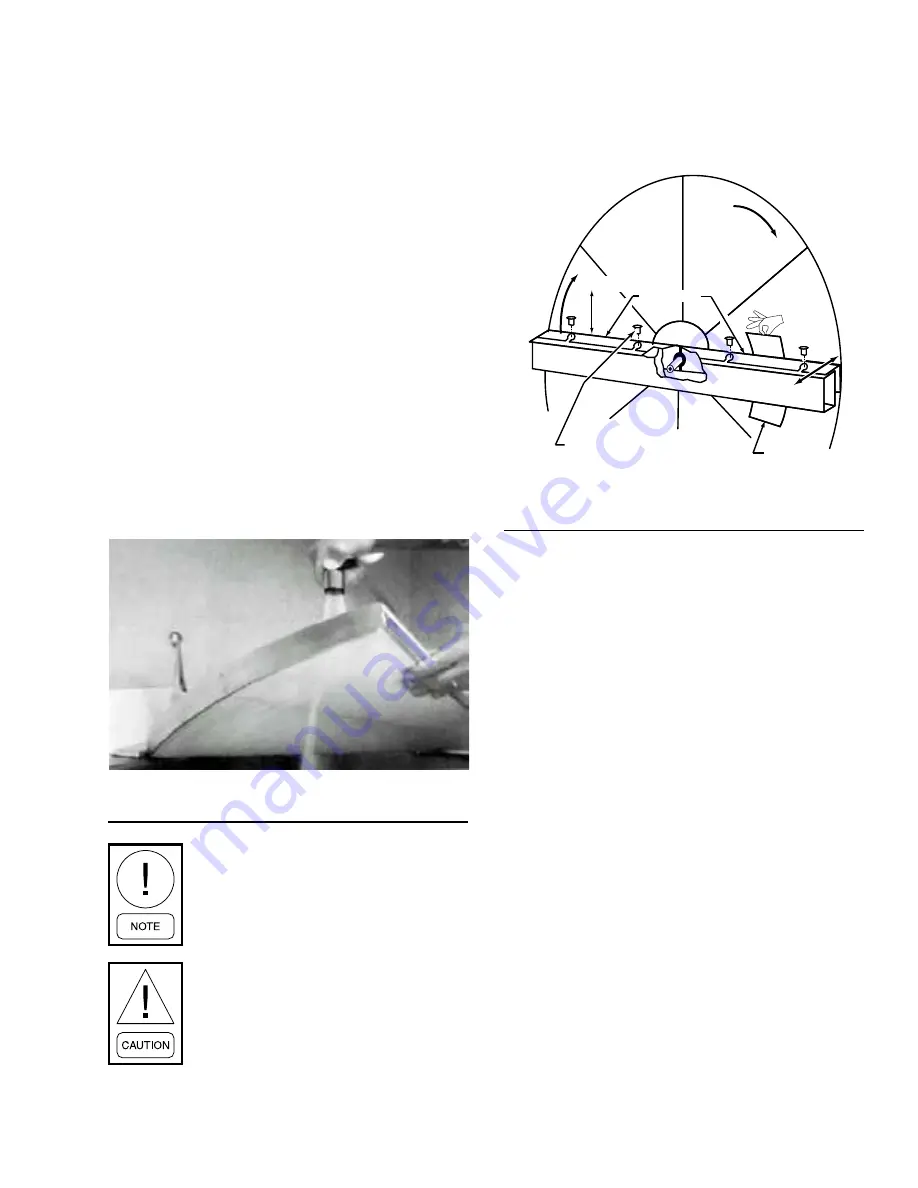
JOHNSON CONTROLS
69
SECTION 3 - MAINTENANCE
FORM 102.20-OM2
ISSUE DATE: 6/01/2015
Cleaning the Wheel
•
To clean, gain access to the energy recovery wheel
and remove the segments as shown in the service
manual.
•
Brush or vacuum foreign material from the face
off the wheel.
•
Wash the segments in a 5% solution of non-acid
based coil cleaner
(see material list)
or alkaline
detergent and warm water.
•
Allow segments to soak in solution until grease
and tar deposits are loosened. An overnight soak
may be required to adequately loosen heavy de-
posits of tar and oil based contaminants. Before
removing from solution, rapidly run finger across
surface of segment to separate polymer strips for
better cleaning action. Rinse dirty solution from
segment with clean water and allow excess water
to drain prior to remounting segments in the wheel
in the service manual as shown in
A small amount of water remaining in
the wheel will be dried out by the airflow.
FIGURE 68 -
RINSE SEGMENTS
LD09659
Some staining of the desiccant may re-
main and is not harmful to performance.
Do not use acid based cleaners, aromatic
solvents, steam or temperatures in excess
of 170°F: damage to wheel may occur!
Adjusting Air Seals
Four adjustable diameter seals are provided on each
cassette to minimize transfer of air between the counter
flowing airstreams.
FIGURE 69 -
DIAMETER SEAL ADJUSTMENT
LD09644
To Remove
Rotation
Diameter
Seal
To Adjust
Feeler
Gauge
Diameter Seal
Adjusting Screws
•
To adjust diameter seals, loosen diameter seal ad-
justing screws and move diameter seal away from
wheel surface.
•
Rotate wheel clockwise until two opposing spokes
are hidden behind the bearing support beam as
shown in
Using a folded piece of paper as a feeler gage, position
paper between the wheel surface and diameter seals.
Adjust seals towards wheel surface until a slight fric-
tion on the feeler gage (paper) is detected when gauge
is moved along the length of the spoke.
•
Retighten adjusting screws and recheck clearance
with feeler gauge.