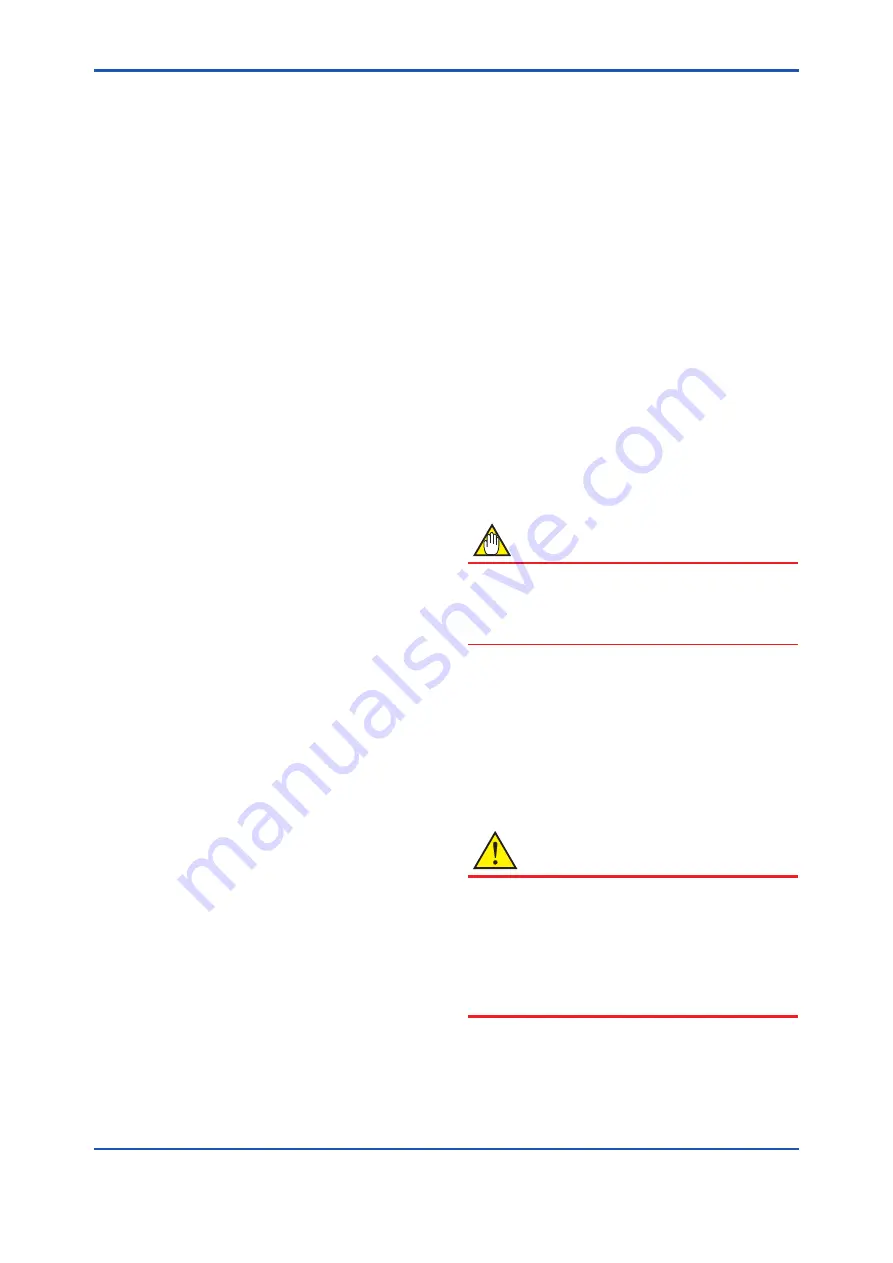
<2. Handling Cautions>
2-3
IM 01C25B01-01E
2.8 Insulation Resistance and
Dielectric Strength Test
Since the transmitter has undergone insulation
resistance and dielectric strength tests at the factory
before shipment, normally these tests are not
required. If the need arises to conduct these tests,
heed the following:
(a) Do not perform such tests more frequently than
is absolutely necessary. Even test voltages that
do not cause visible damage to the insulation
may degrade the insulation and reduce safety
margins.
(b) Never apply a voltage exceeding 500 V DC
(100 V DC with an internal lightning protector)
for the insulation resistance test, nor a voltage
exceeding 500 V AC (100 V AC with an internal
lightning protector) for the dielectric strength
test.
(c) Before conducting these tests, disconnect
all signal lines from the transmitter terminals.
The procedure for conducting these tests is as
follows:
• Insulation Resistance Test
1) Short-circuit the + and – SUPPLY terminals
in the terminal box. In case of 1 to 5 V output,
short-circuit the , SUPPLY – and A
(VOUT +) terminals.
2) Turn OFF the insulation tester. Then connect
the insulation tester plus (+) lead wire to the
shorted SUPPLY terminals and the minus (–)
leadwire to the grounding terminal.
3) Turn ON the insulation tester power and
measure the insulation resistance. The voltage
should be applied as briefly as possible to verify
that the insulation resistance is at least 20 MΩ.
4) After completing the test and being very careful
not to touch exposed conductors disconnect the
insulation tester and connect a 100 kΩ resistor
between the grounding terminal and the short-
circuiting SUPPLY terminals. Leave this resistor
connected at least one second to discharge any
static potential. Do not touch the terminals while
it is discharging.
• Dielectric Strength Test
1) Short-circuit the + and – SUPPLY terminals
in the terminal box. In case of 1 to 5 V output,
short-circuit the , SUPPLY – and A
(VOUT +) terminals.
2) Turn OFF the dielectric strength tester. Then
connect the tester between the shorted
SUPPLY terminals and the grounding terminal.
Be sure to connect the grounding lead of the
dielectric strength tester to the ground terminal.
3) Set the current limit on the dielectric strength
tester to 25 mA, then turn ON the power and
gradually increase the test voltage from ‘0’ to
the specified voltage.
4) When the specified voltage is reached, hold it
for one minute.
5) After completing this test, slowly decrease the
voltage to avoid any voltage surges.
2.9 Installation of an Explosion-
Protected Instrument
NOTE
For F
OUNDATION
Fieldbus explosion protected
type, please refer to IM 01C25T02-01E.
For PROFIBUS PA explosion protected type,
please refer to IM 01C25T04-01EN.
If a customer makes a repair or modification to
an intrinsically safe or explosionproof instrument
and the instrument is not restored to its original
condition, its intrinsically safe or explosionproof
construction may be compromised and the
instrument may be hazardous to operate. Please
contact Yokogawa before making any repair or
modification to an instrument.
CAUTION
This instrument has been tested and certified
as being intrinsically safe or explosionproof.
Please note that severe restrictions apply to this
instrument’s construction, installation, external
wiring, maintenance and repair. A failure to abide
by these restrictions could make the instrument a
hazard to operate.