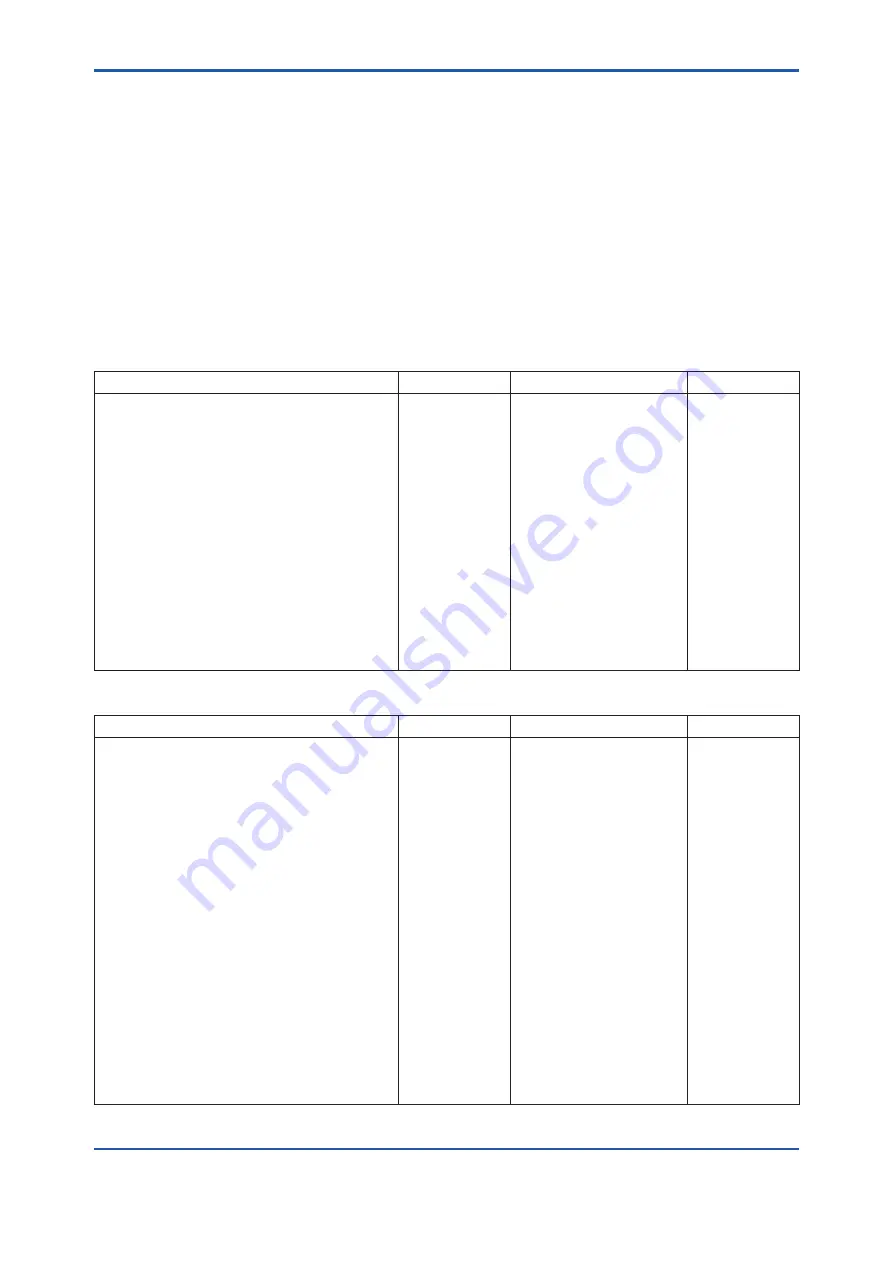
IM 01E21A21-02EN
<2. Safety Instrumented Systems Installation>
6
2.2.6 Proof Test
A proof test is a periodic test to verify that the Safety Instrumented Function work without fails.
It is mandatory to have a proof test in order to detect any failure which is not detected by the diagnostic of the
product, which prevents any action of the Safety Instrumented Function (SIF) from its intention.
The frequency of the proof tests (or the proof test interval) is to be determined in the reliability calculations for
the SIFs for which this product is applied. The actual proof tests must be carried out “more frequently” or “as
frequently as specified” in the calculation in order to preserve required safety integrity of the SIF.
Proof test results are required to be documented. And this documentation should be a part of the plant safety
management system. Failures that are detected should be reported to YOKOGAWA.
The personnel carrying out the proof test of products should be trained in SIS operations including bypass
procedures, maintenance of this product, and company management of change procedures.
Disable the write protect function before proof test. After the proof test, enable the write protect function.
Table 2.2.5 Abbreviated Proof Test
Testing method
Tool required
Expected outcome
Remarks
Loop test for “Analog output”
1. Bypass the safety PLC or take other
appropriate action to avoid a false trip.
2. Make a note of the “AO1 alarm out” when the
proof test is carrying out.
3. After setting the “AO1 alarm out” to “>21.6 mA”
via BRAIN or HART communication, actually
generate an alarm and verify that the current
value is above 21.6 mA.
4. After setting the “AO1 alarm out” to “<2.4 mA”
via BRAIN or HART communication, actually
generate an alarm and verify that the current
value is less than 2.4 mA.
5. Clear the all alarm.
6. Return the setting of “AO1 Alarm out” to the
value you noted in Step 2.
7. Remove the bypass and otherwise restore
normal operation.
For BRAIN:
BRAIN
configuration tool
For HART:
HART
configuration tool
Proof Test Coverage;
ADMAG TI Multi (Non-IS)
Option = 68.6%
ADMAG TI IS Option =
69.5%
The output
needs to be
monitored to
assure that
this product
communicates
the correct signal
Table 2.2.6 Extended Proof Test
Testing method
Tool required
Expected outcome
Remarks
Loop test for “Analog output”
1. Bypass the safety PLC or take other
appropriate action to avoid a false trip.
2. Make a note of the “AO1 alarm out” when the
proof test is carrying out.
3. After setting the “AO1 alarm out” to “>21.6 mA”
via BRAIN or HART communication, actually
generate an alarm and verify that the current
value is above 21.6 mA.
4. After setting the “AO1 alarm out” to “<2.4 mA”
via BRAIN or HART communication, actually
generate an alarm and verify that the current
value is less than 2.4 mA.
5. Clear the all alarm.
6. Return the setting of “AO1 Alarm out” to the
value you noted in Step 2.
7. Perform a two-point calibration in the
maximum and minimum flow ranges.
8. Check current output when there is no flow in
the meter.
9. Check current output when there is typical flow
in the meter.
10. Remove the bypass and otherwise restore
normal operation.
For BRAIN:
BRAIN
configuration tool
For HART:
HART
configuration tool
Proof Test Coverage;
ADMAG TI Multi (Non-IS)
Option = 83.0%
ADMAG TI IS Option =
83.7%
The output
needs to be
monitored to
assure that
this product
communicates
the correct signal