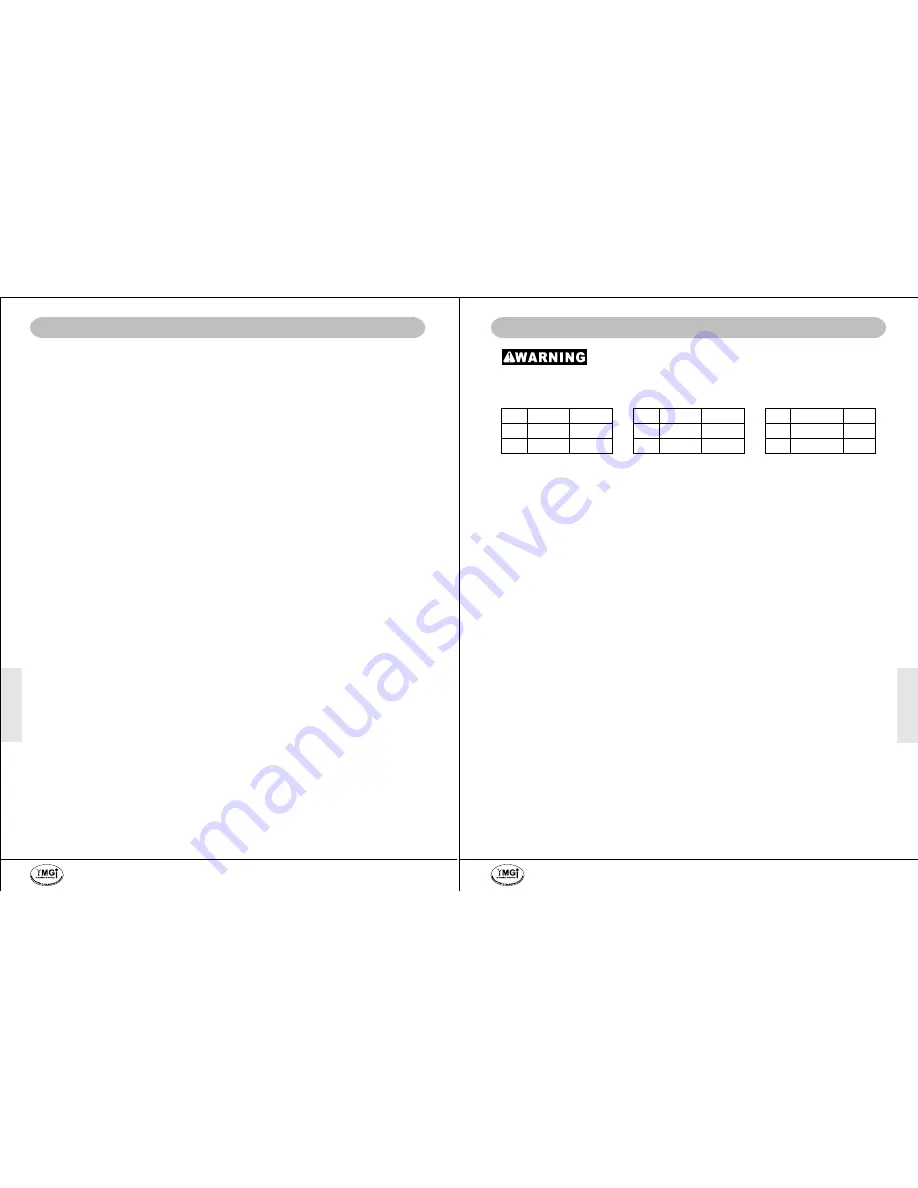
W
ARRANTY
POLICIES
AND REGISTRA
TION
CARD/FORM
WARRANTY AND TECHNICAL SUPPORT
YMGI warrants to the purchaser/owner(s) that YMGI products be free from defects in
workmanship under the normal use and maintenance, with the standard Limited Product Warranty
Policies that comes with the unit or sales package.
material and
YMGI IS NOT RESPONSIBLE FOR
CONTACT FOR FIELD SERVICE OR REPAIR
The following people, in a prioritized sequence, will take care of your request or issue:
1) The original installer; otherwise,
2) Your current service contractor; otherwise,
3) Authorized contractor in YMGI list that is close to you; otherwise,
4) Authorized Distributor in YMGI Distributor list; otherwise,
5) Contractor/Distributor you prefer who is close to you.
CONTACT FOR GENERAL TECHNICAL QUESTIONS OR SUPPORT, IN A SEQUENCE:
1) The original installer; otherwise,
2) The current service contractor; otherwise,
3) The distributor; where the unit is purchased from otherwise,
4) YMGI Technical Support:
Tel: (866) 833-3138*703 Email: [email protected]
* Regular equipment maintenance or field service or field inspection.
* Damage or repairs required as a consequence Customer do-it-yoursely(DIY) installation and/or any other faulty
installation or improper application.
* Failure to start due to voltage conditions, blown fuses, open circuit breakers, or other damages due to the
inadequacy or interruption of electrical service.
* Damage or repairs needed as a consequence of any misapplication, abuse, improper servicing, unauthorized
alteration, or improper operation.
* Damage as a result of floods, winds, fires, lightening, accidents, corrosive atmosphere, or other conditions
beyond the control of YMGI.
* Parts not supplied or designated by YMGI.
* Products installed outside USA or Canada.
* Any damages to person or property of whatever kind, direct or indirect, special or consequential, whether
resulting from use or loss of use of the product.
The original licensed installer or current service contractor should be contacted first of all, since they installed
the unit and/or know more details than anybody else.
They will check the unit and find out the problems with the professional knowledge about HVAC and electric
product installation by using special tools or instrument.
They can contact YMGI technical support for technical help during unit installation or inspection.
Product model and serial numbers needed, which can be found on unit nameplate sticker, so that our
technician can quickly identify the unit, parts and wiring diagrams, among our many products and models.
* Any problems due to improper cooling and heating load calcuation of the room/building the air conditioner/heat
pump system is to be installed. Equipment users can get the calculation schedule from your room/building
architect or your installation or related service HVAC contractor, who should have the knowledge and the tools
to do these calculations correctly.
* Any problems due to improper sizing and selecting air conditioner/heat pump system. These equipment sizing
and selection work should be conducted by either your room/building architect or your installation or related
service HVAC contractor, who should have the knowledge and the tools to do these calculations correctly, and
get your approval, before purchasing the air conditioner or heat pump equipment.
* Any problems due to improper installing of the air conditioner/heat pump system. Installation should be
conducted by currently licensed HVAC technician, following manufacturer installation instructions, all governing
safety codes, with care and professionalism.
* Any problems due to improper operation of the air conditioner/heat pump system. Users shall keep the manual
and refer to it for the correct understanding of how the unit will work and how to operate the unit correctly.
* Any problems due to improper maintenance of the air conditioner/heat pump system. Like a car, regular
maintenance or yearly checking is necessary for the unit to work properly for you, before the season comes. For
example, air filter shall be checked for cleaness from time to time. Remote control batteries shall be checked for
enough power, before judging the unit is not working...
P7 OF 36
YMGI, Engineered Comfort Products for A Sustainable and Efficient Green World !
P8 OF 36
YMGI, Engineered Comfort Products for A Sustainable and Efficient Green World !
NA
o
o
65 F to 115 F
o
o
5 F to 86 F
Mode
Cooling
Heating
Dry Bulb-High
o
86 F
o
86 F
Dry Bulb-Low
o
61 F
o
61 F
o
o
61 F to 105 F
o
o
47 F to 86 F
Wet Bulb
NA
NA
Mode
Cooling
Heating
Dry Bulb
Wet Bulb
NA
Mode
Cooling
Heating
Dry Bulb
Recommended Temperature
Ranges-Indoor Side (Capacity
& Efficiency Varies)
Recommended Temperature
Ranges-Outdoor Side (Capacity
& Efficiency Varies)
OPERATING TEMPERATURE RANGES
Temperature
Ranges of
Remote/Line Control
Operate the unit in the temperature ranges shown below. It is not recommended
to operate the unit out of these ranges, otherwise warranty will be voided.
IMPORTANT NOTES FOR INSTALLING CONTRACTOR / TECHNICIAN, AND UNIT OWNER / USERS:
Load Calculation, Unit Sizing and Selection, Capacity and Efficiency, Heat Pump:
2) Load calculation must be done carefully and correctly by experienced technician, for each room that needs to be conditioned, before
sizing unit and selecting correct model. Not to undersize or oversize the unit.
3) It is strongly recommended to have the units work within the recommended temperature ranges.
4) Units may still work fine, even if the outdoor temperatures go out of the recommended ranges shown above. But, this is not guaranteed
and performance varies upon many different factors such as unit type, model, size, location, installation, unit conditions and weather, etc.
5) Unit performance and its lifetime count on unit installation quality and maintenance level.
6) Standard capacity and efficiency are rated at AHRI 210/240 standard indoor and outdoor unit temperatures, indoor unit is hung 7 feet
above outdoor unit with 25' linear interconnection copper tubes being well insulated and nameplate refrigerant charge. If any of these
conditions change, capacity or efficiency will change too.
7) When outdoor temperature is too high in cooling mode, or too low in heating mode, system capacity and efficiency will decrease (this is
true for all brands of similar product).
8) Units (13SEER) built with fixed speed compressors are designed for where cooling applications in high & mild ambient temperatures. If you
want to use these units to cool spaces such as server rooms or interior rooms, even when outdoor temperatures go to low ranges (such as
lower than 15F) at night time or winter time, you will need to install a
Low Ambient Control
kit at outdoor unit to control fan the speed
and/or its cycling. Be sure to inform your installer of the units application and requirements, before the unit is selected or installed, so that
the Low Ambient Control can be installed at the very beginning. This will help to keep the coil from freezing up during cooling in low
ambient temperatures.
9) Heat pump systems are not supposed to be used as the only source of heating, especially for areas where ambient temperatures
drop below 35F for most of heating season.
10) 13SEER units are built with fixed speed compressor, unlike DC inverter type, and are only designed for heating applications in mild
ambient temperatures. The lowest temperatures that the 13SEER units have been tested to is 17F. But the units can still generate a pretty
good amount of heat, even when ambient temperatures go to lower ranges. When ambient temperatures drop to lower ranges, heat pump
units generate less capacity at lower efficiency. If you want to use these units to heat spaces in northern regions where yearly heating
hours are more than yearly cooling hours, an indoor unit that has the backup electric heat should be installed along with the heat pump
units. This way, the back-up heater can make up heat when the heat pump unit doesn't generate enough heat, or take its place to heat up
your space when the heat pump efficiency HSPF drops close to or below 1.0. You can ask the installer to set up the control or switch to
be either manual, or automatic.
11) In heat pump mode, the suction (bigger) valve/pipe at the condensing unit should be hot. The discharge (smaller) valve/pipe should be
also hot or at least warm. The higher the ambient temperature is, the hotter the valve/pipes will be.
12) In heat pump mode, if the refrigerant leaks or pipe kinks or there is other type of restriction somewhere in the pipe, the valve/pipes are
not as hot as it should be. Must avoid any of these installation problems.
13) In cooling mode, if the refrigerant leaks or pipe kinks or there is other type of restriction somewhere, the valve/pipes could be either too
cold (frost or even ice up) or too warm. It varies upon the level of refrigerant left in the system. Must avoid any of these installation problems.
14) To protect against unit/part damage due to many reasons, including but not limited to too high or too low ambient temperatures, too hot
or too cold indoor coil, refrigerant leakage, mixed with air, etc., system may stop working and may show error codes. Need to call your
installer/technician to check the system, before units can resume normal operaton.
15) Suggest your HVAC contractor/technician to check for leakage and refrigerant leakage and refrigerant level, before cooling or heating
season comes.
16) Optional component
Wind Baffle
can be added/installed at the fan discharge side on the heat pump outdoor condensing unit cabinet,
to keep from cold wind blowing against air discharge (headwind will drop heating capacity and efficiency at same ambient temperatures).
1) It is the current installing HVAC technician/contractors responsibility to calculate the cooling load and/or heating load of the room to be
conditioned by using a commercial cooling and heating load program. There are many details to be considered when performing a load
calculation including but not limited to: a.Room structure details; b. Annual cooling hours; c. Annual heating hours; d. The highest annual
ambient temperature; e. The lowest annual ambient temperature; f. Time frame of unit use during summer and winter times; g. Is cooling
needed during times of low ambient temperatures? h.Is heating needed during times of high ambient temperatures? i. Rooms ventilation;
j. Will back up electric heat be needed during heating?
BRIEF UNIT INFO