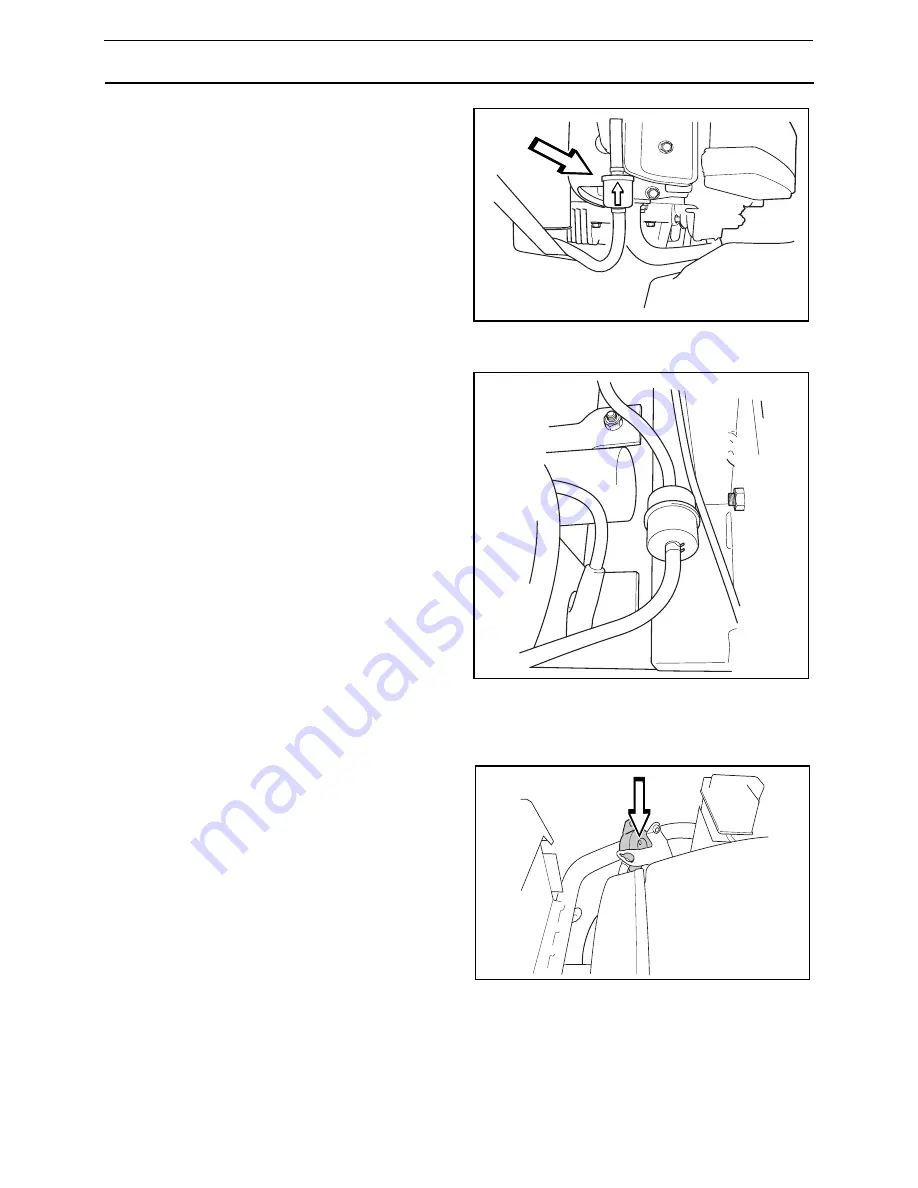
English-
44
MAINTENANCE
Replacing the Fuel Filter
Replace the line-mounted fuel filter every
100 hours (once per season) or more often if
it becomes clogged.
Replace the filter as follows:
1. Move the hose clamps away from the
filter. Use flat-nosed pliers.
2. Pull the filter loose from the hose ends.
3. Push the new filter into the hose ends.
Position the filter with the “FLOW” arrow
pointing up toward the fuel pump. If
necessary, a soap solution can be
applied to the filter ends to ease
mounting.
4. Move the hose clamps back toward the
filter.
Checking the Fuel Pump’s Air Filter
Regularly check that the fuel pump’s air filter
is free from dirt.
On Kohler engine, removal of the pump
screws is not needed, due to the filter facing
outwards.
Remove the screws and open the pump, no
hoses need be removed.
The filter can be cleaned with a brush if
necessary.
Replace the filter on the console.
8009-146
Fuel filter Kawasaki
8011-468
Fuel filter Kohler
8009-147
The fuel pump’s air filter
Summary of Contents for ZVKH61273
Page 2: ......
Page 42: ...English 40 MAINTENANCE 8011 553 Safety system Start motor Works Does not work Ignition system...
Page 80: ...English 78 SERVICE JOURNAL Action Date mtr reading stamp sign...
Page 81: ...SERVICE JOURNAL Action Date mtr reading stamp sign...
Page 82: ...SERVICE JOURNAL Action Date mtr reading stamp sign...
Page 83: ......
Page 84: ...539 131260 IR 07 07...