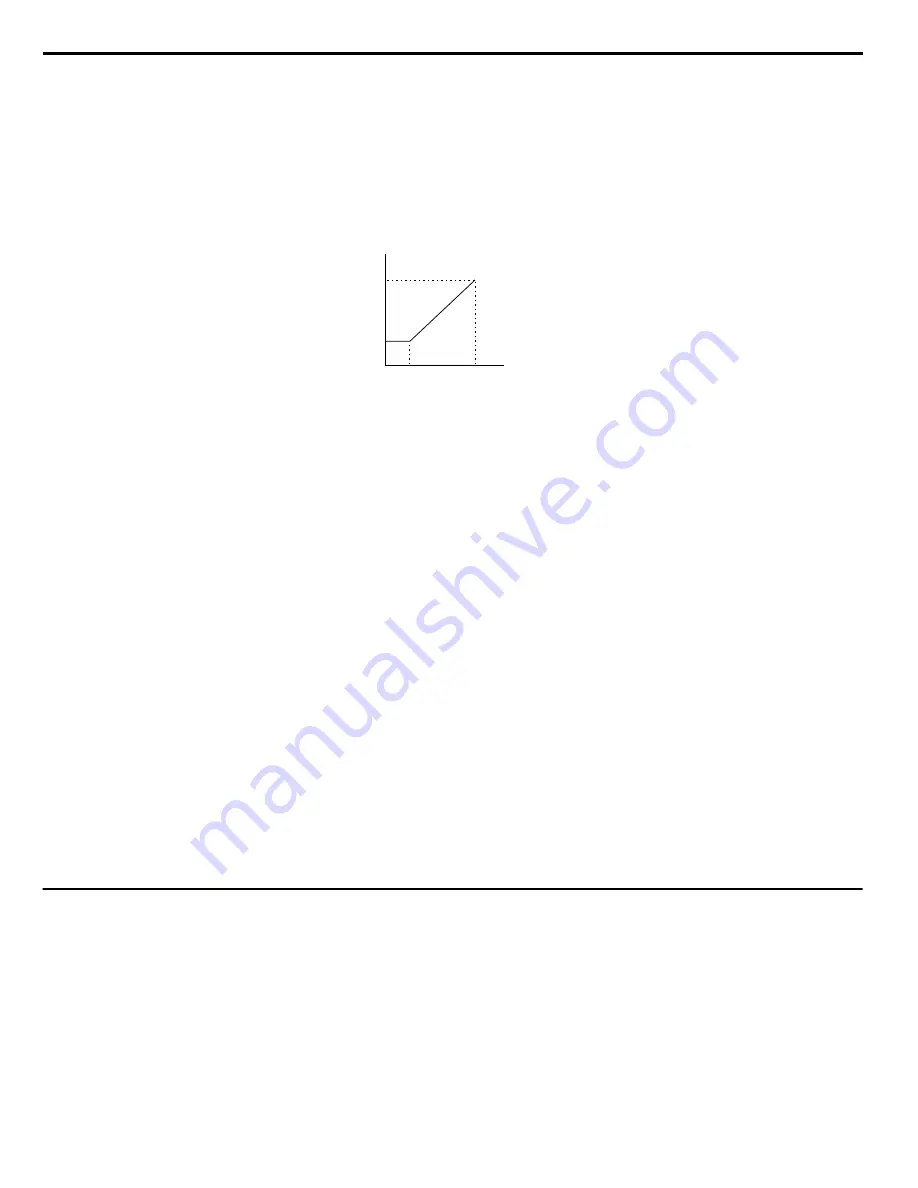
Setting 7: Torque Detection Level
Using this setting, the overtorque/undertorque detection level for torque detection 1 (L6-01) can be set by an analog input.
The analog input replaces the level set to L6-02. An analog input of 100% (10 V or 20 mA) sets a torque detection level equal
to 100% drive rated current/motor rated torque. Adjust the analog input gain if higher detection level settings are required.
Refer to L6: Torque Detection on page 114
for details on torque detection.
Setting 8: Stall Prevention Level
Allows an analog input signal to adjust the Stall Prevention level.
shows the setting characteristics. The drive will
use the lower value of the Stall Prevention level set to L3-06 or the level coming from the selected analog input terminal.
Stall Prevention Level during Run
30%
100%
Analog Input Level
30%
100%
0
Figure 1.54 Stall Prevention During Run Using an Analog Input Terminal
Setting 9: Output Frequency Lower Limit Level
The user can adjust the lower limit of the output frequency using an analog input signal.
Setting B: PI Feedback
Supplies the PI feedback value. This setting requires PI operation to be enabled in b5-01.
Setting C: PI Setpoint
Supplies the PI setpoint value and makes the frequency reference selected in parameter b1-01 no longer the PI setpoint. PI
operation to be enabled in b5-01 to use this setting.
Refer to PI Setpoint Input Methods on page 37
.
Setting D: Frequency Bias
The input value of an analog input set to this function will be added to the frequency reference. This function can be used with
any frequency reference source.
Setting E: Motor Temperature
In addition to motor overload fault detection oL1, it is possible to use a PTC (Positive Temperature Coefficient) thermistor
for motor insulation protection.
Setting F: Through Mode
When set to F, an input does not affect any drive function, but the input level can still be read out by a PLC via APOGEE
FLN, BACnet, MEMOBUS/Modbus, or Metasys N2 communications.
Setting 16: Differential PI Feedback
If an analog value is set for this function, the PI controller is set for differential feedback. The difference of the PI feedback
Feedback Input Methods on page 38
.
u
H4: Multi-Function Analog Outputs
These parameters assign functions to analog output terminals FM and AM for monitoring a specific aspect of drive
performance.
n
H4-01, H4-04: Multi-Function Analog Output Terminal FM, AM Monitor Selection
Sets the desired drive monitor parameter U
o
-
oo
to output as an analog value via terminal FM and AM.
for a list of all monitors. The “Analog Output Level” column indicates whether a monitor can be
used for analog output.
Example: Enter “103” for U1-03.
1.7 H: Terminal Functions
96
YASKAWA SIEP YAIZ1U 03B YASKAWA AC Drive – Z1000 Programming Manual
Summary of Contents for Z1000 CIMR-ZU*A Series
Page 339: ......