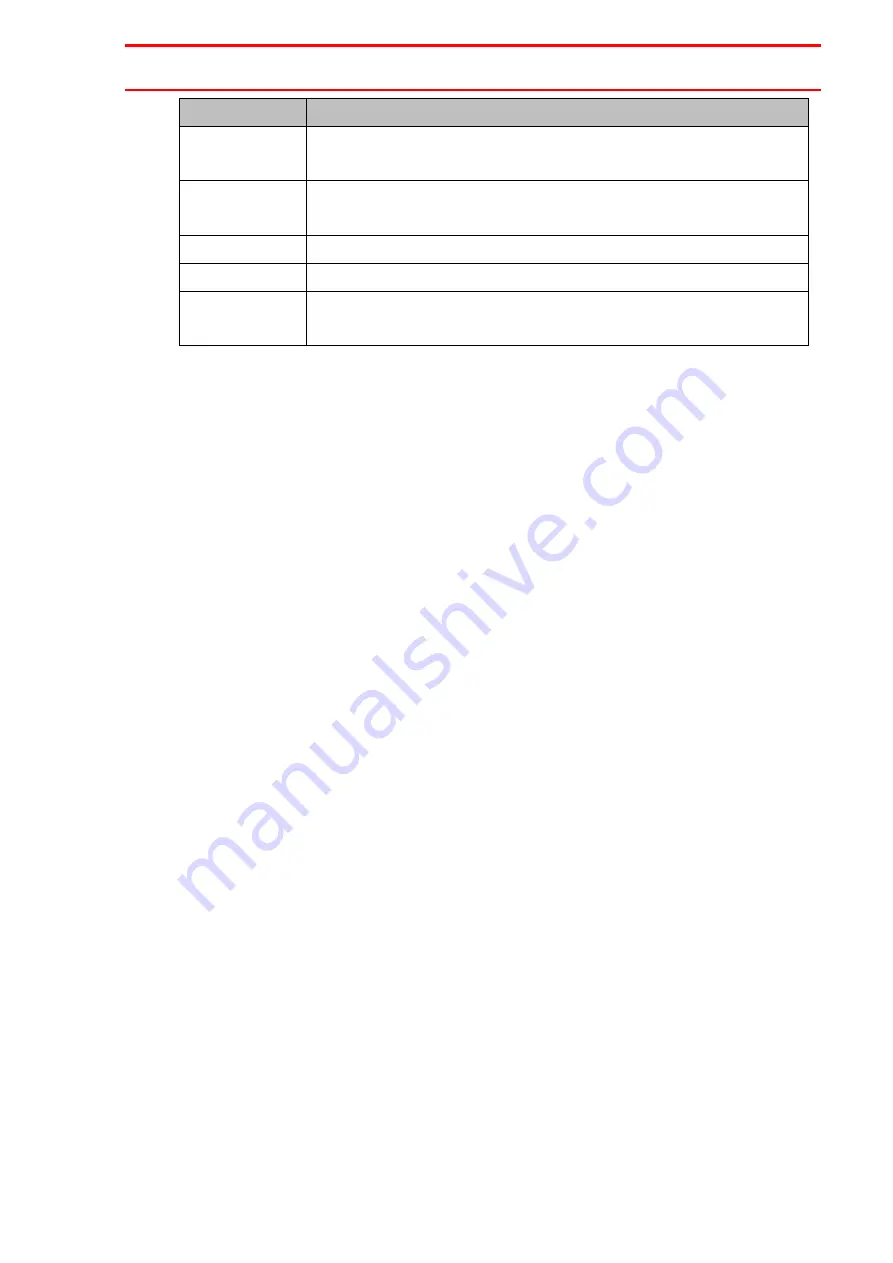
HW1484764
Default Settings of Function Safety General-Purpose I/O Signals
11-2
HW1484764
Signal
Signal Name
MS-OUT53
Speed limit request during collaborative operation (to be output to
an external safety device)
MS-OUT54
Collaborative operation request (to be input from an external safety
device)
MS-OUT55
Category 0 stop request (to be input from an external safety device)
MS-OUT56
Category 1 stop request (to be input from an external safety device)
MS-OUT57
Operation resumption request (to be input from an external safety
device)
100/105