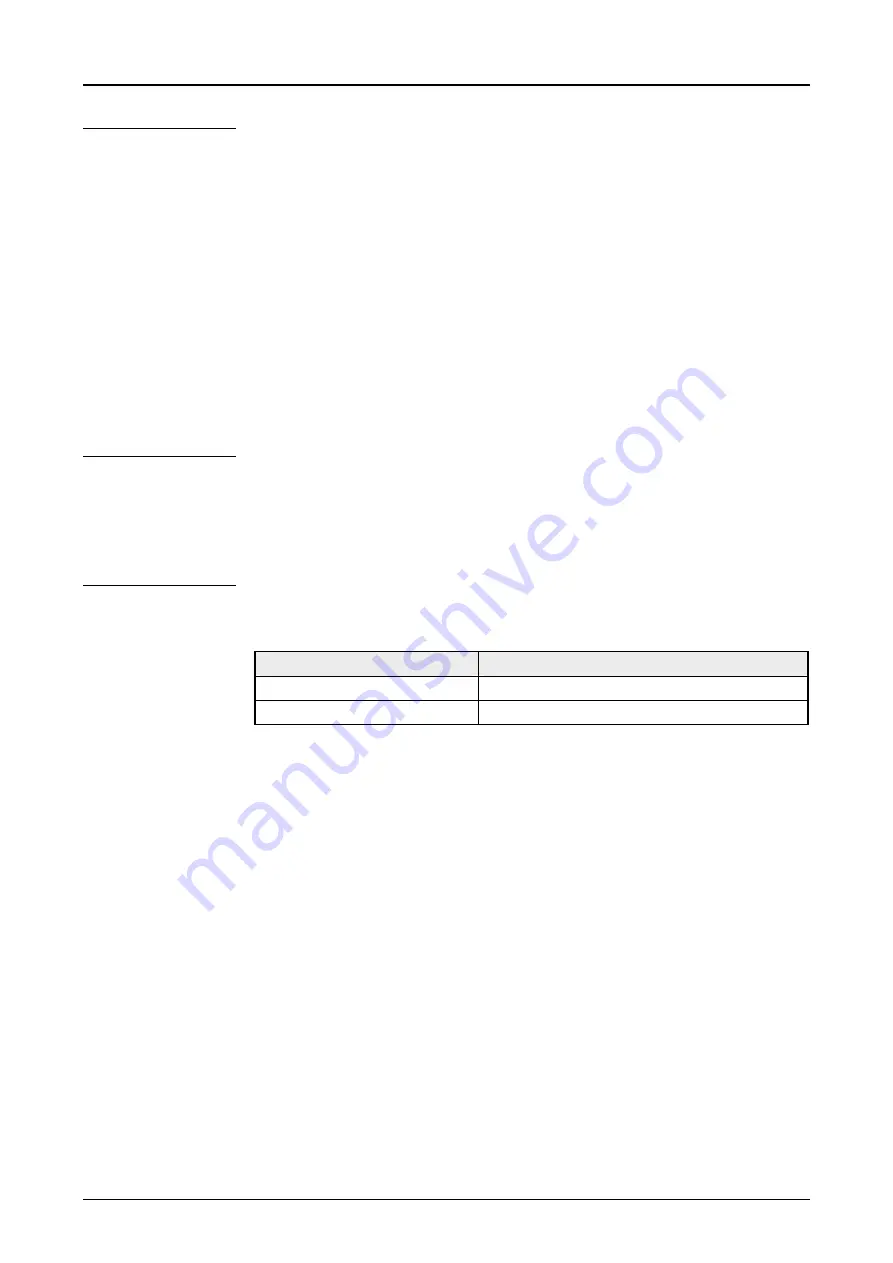
Chapter 3 Deployment
Manual VIPA System 300S
3-10
HB140E - IM - RE_353-1DP01 - Rev. 14/47
PROFIBUS employs screened twisted pair cable on the basis of the RS485
interface. The data transfer rate of the system is limited to a max. of
12MBaud.
The RS485 interface uses differential voltages. For this reason this kind of
interface is less susceptible to interference than a plain voltage or current
based interface. The network may be configured as linear or as tree
structure. Your PROFIBUS coupler carries a 9pin socket. This socket is
used to connect the PROFIBUS coupler to the PROFIBUS network as a
slave.
Due to the bus structure of RS485, any station may be connected or
disconnected without interruptions and a system can be commissioned in
different stages. Extensions to the system do not affect stations that have
already been commissioned. Any failures of stations or new devices are
detected automatically.
Every device on the PROFIBUS is identified by an address. This address
must be an unique number in the bus system between 1 and 99. The
address of the VIPA PROFIBUS coupler is set by the addressing switch
located on the front of the module.
The GSD files may be found at www.vipa.com at the "Service" part.
The assignment of the GSD-file to your slave is shown in the following
table:
Order number
GSD-file
VIPA 353-1DP01(DP-V0)
VI0009AF.gsd
*
VIPA 353-1DP01(DP-V1)
VI0109AF.gsd
*)
This GSD-file is used for PROFIBUS master that don't support DP-V1.
Please install the required files from your disc into your configuration tool.
Details on the installation of the GSD and/or type files are available from
the manual supplied with your configuration tool.
After the installation of the GSD-file you will find this entry e.g. in the
hardware catalog under:
PROFIBUS DP>Additional field devices>I/O>VIPA_System_300V>
VIPA 353-1DP01.
Data transfer
medium as
RS485 interface
Addressing
GSD- file