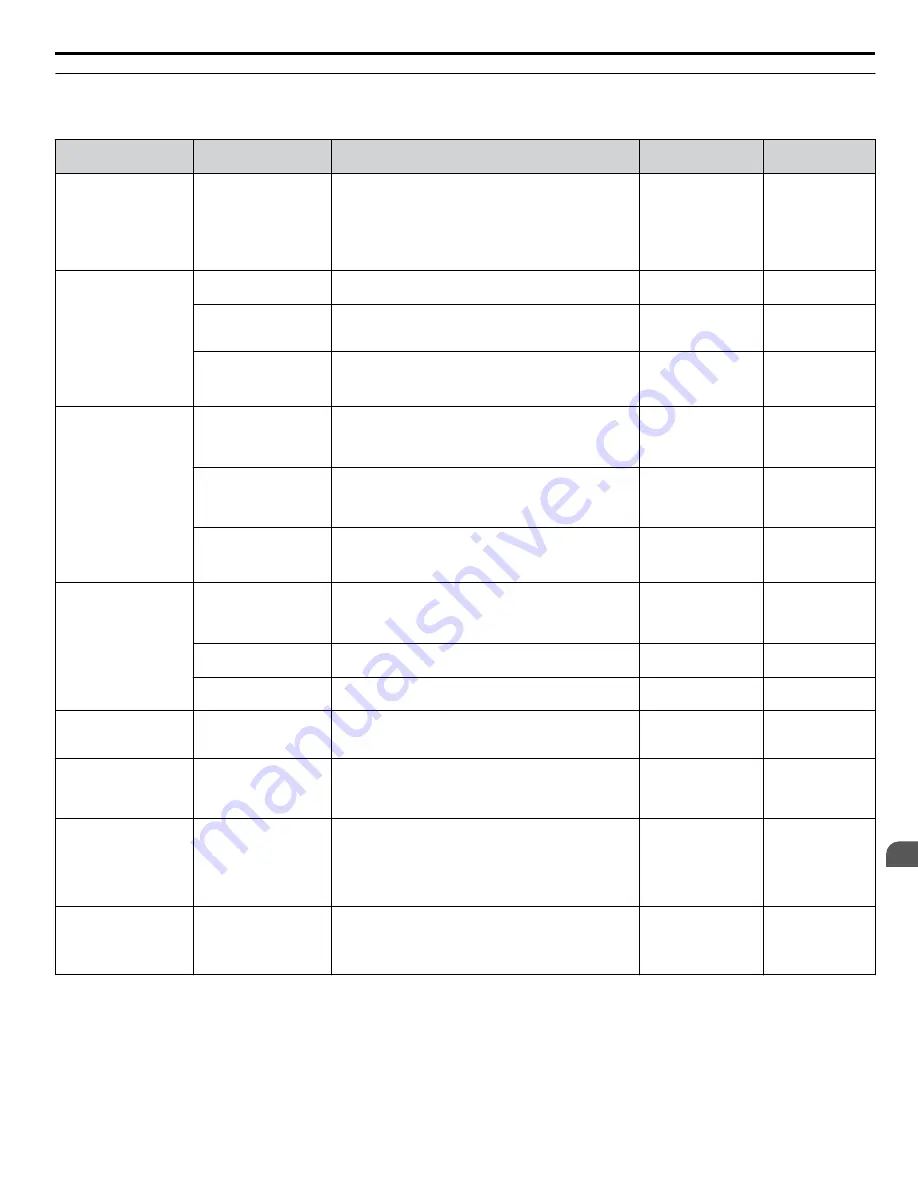
u
Fine-Tuning Open Loop Vector Control for PM Motors
Table 6.4 Parameters for Fine-Tuning Performance in OLV/PM
Problem
Parameter No.
Corrective Action
Default
Suggested
Setting
Undesirable motor
performance
Motor parameters
(E1-
oo
, E5-
oo
)
• Check the settings for base and maximum frequency
in the E1-
oo
parameters.
• Check E5-
oo
parameters and set motor data
correctly. Do not enter line-to-line data where single-
phase data is required, and vice versa.
• Perform Auto-Tuning.
-
-
Poor motor torque and
speed response
Load Inertia (n8-55)
Adjust parameter n8-55 to meet the load inertia ratio of
the machine.
0
Close to the actual
load inertia ratio
Speed Feedback
Detection Control Gain
(for PM Motors) (n8-45)
Increase the speed feedback detection control gain
(n8-45).
0.8
Increase in
increments of 0.05
Torque Compensation
Gain (C4-01)
Enable torque compensation.
Note:
Setting this value too high can cause
overcompensation and motor oscillation.
0
1
Oscillation at start or the
motor stalls
Acceleration/
Deceleration Pull-In
Current (for PM Motors)
(n8-51)
Increase the pull-in current in n8-51
50%
Increase in steps of
5%
DC Injection Braking
Current (b2-02), DC
Injection Time at Start
(b2-03)
Use DC Injection Braking at start to align the rotor. This
may cause a short reverse rotation at start.
b2-02 = 50%
b2-03 = 0.0 s
b2-03 = 0.5 s
Increase b2-02 if
needed
Load Inertia (n8-55)
Increase the load inertia ratio.
Note:
Setting this value too high can cause
overcompensation and motor oscillation.
0
Close to the actual
load inertia ratio
Stalling or oscillation
occur when load is
applied during constant
speed
Pull-In Current
Compensation Time
Constant (for PM
Motors) (n8-47)
Reduce n8-47 if hunting occurs during constant speed.
5.0 s
Reduce in
increments
of 0.2 s
Pull-In Current (for PM
Motors) (n8-48)
Increase the pull-in current in n8-48.
30%
Increase in
increments of 5%
Load Inertia (n8-55)
Increase the load inertia ratio.
0
Close to the actual
load inertia ratio
Hunting or oscillation
occur
Speed Feedback
Detection Control Gain
(for PM Motors) (n8-47)
Reduce the speed feedback detection gain in n8-45.
0.8
Increase in
increments 0.05
STo fault trips when the
load is not excessively
high
Motor Induction
Voltage Constant 1/2
(Ke) (for PM Motors)
(E5-09 or E5-24)
• Check and adjust the induced voltage constant.
• Check the motor nameplate and the data sheet or
contact the motor manufacturer.
Depends on drive
capacity and motor
code
Refer to the motor
data sheet or the
nameplate.
Stalling or STo occurs at
high speed as the output
voltage becomes
saturated
Output Voltage Limit
(for PM Motors) (n8-62) Set the value of the input voltage to parameter n8-62.
200 Vac
(200 V class)
400 Vac
(400 V class)
575 Vac
(600 V class)
Set equal to input
voltage
Oscillation at constant
output when U6-02
displays -10% or more.
Output Voltage Limit
Proportional Gain (for
PM Motors) (n8-63)
Decrease the output voltage limit proportional gain
(n8-63).
Note:
The speed response will be slow if the
setting is too low.
1.00
0.10 to 1.00
Decrease in
decrements of 0.1
6.2 Motor Performance Fine-Tuning
YASKAWA ELECTRIC SIEP C710636 04D U1000 Industrial MATRIX Drive Technical Manual
359
6
Troubleshooting
Summary of Contents for U1000 iQpump Drive
Page 705: ......