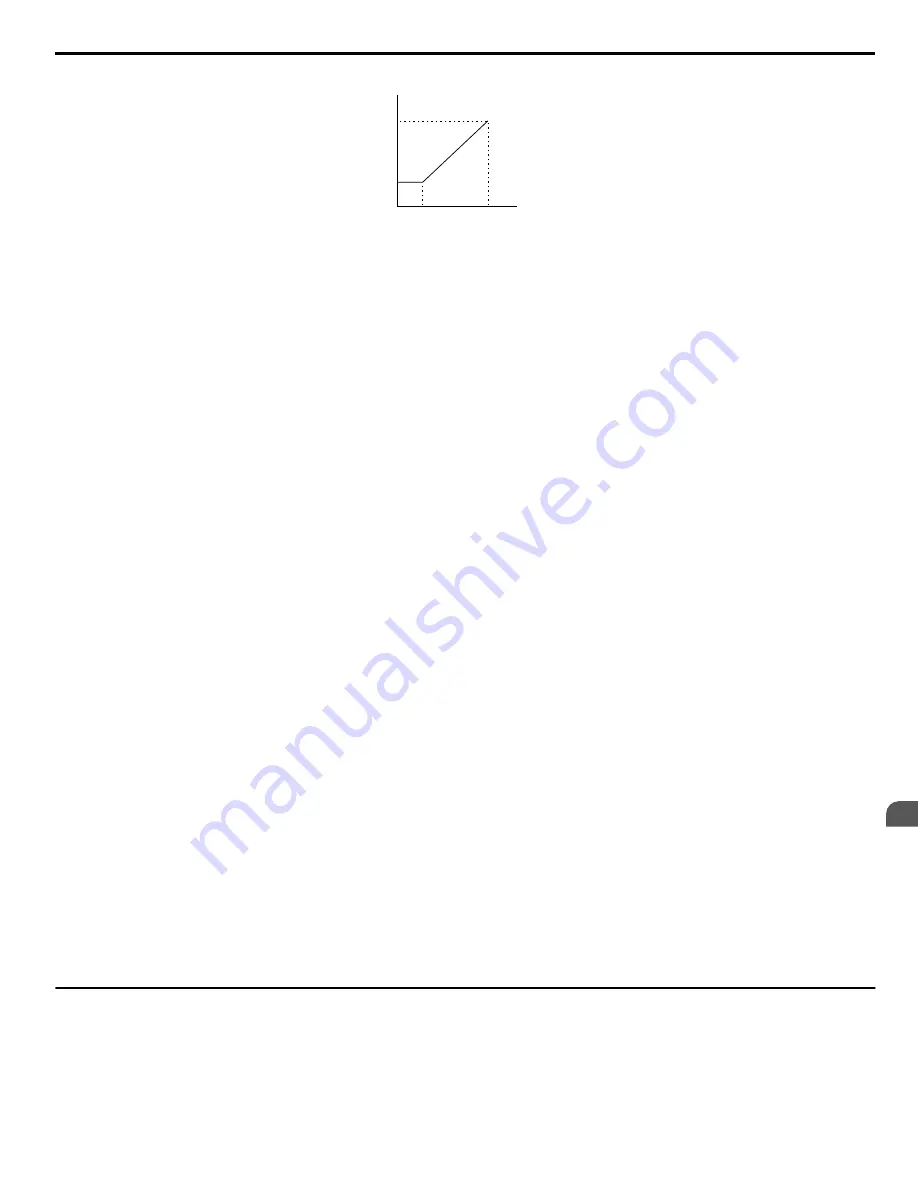
Stall Prevention Level during Run
30%
100%
Analog Input Level
30%
100%
0
Figure 5.83 Stall Prevention During Run Using an Analog Input Terminal
Setting 9: Output Frequency Lower Limit Level
The user can adjust the lower limit of the output frequency using an analog input signal.
Setting B: PID Feedback
Supplies the PID feedback value. This setting requires PID operation to be enabled in b5-01.
Setting C: PID Setpoint
Supplies the PID setpoint value and makes the frequency reference selected in parameter b1-01 no longer the PID setpoint.
PID operation to be enabled in b5-01 to use this setting.
Refer to PID Setpoint Input Methods on page 207
Setting D: Frequency Bias
The input value of an analog input set to this function will be added to the frequency reference. This function can be used with
any frequency reference source.
Setting E: Motor Temperature
In addition to motor overload fault detection oL1, it is possible to use a Positive Temperature Coefficient (PTC) thermistor
for motor insulation protection.
Refer to Motor Protection Using a Positive Temperature Coefficient (PTC) Thermistor on
for a detailed explanation.
Setting F, 1F: Through Mode
When set to F or 1F, an input does not affect any drive function, but the input level can still be read out by a PLC via a
communication option or MEMOBUS/Modbus communications.
Setting 10, 11, 12, 15: Forward, Reverse, Regenerative, General Torque Limit (OLV, CLV, AOLV/PM, CLV/PM)
These functions set a torque limit using analog inputs for different operating conditions.
Refer to L7: Torque Limit on page
for details.
Setting 13: Torque Limit Using Torque Reference/Speed Limit
Sets the torque reference (when in Torque Control) or the torque limit (when in Speed Control).
Reference, Speed Limit, and Torque Compensation Values on page 245
Setting 14: Torque Compensation
Sets a torque compensation value when using Torque Control.
Refer to Setting the Torque Reference, Speed Limit, and
Torque Compensation Values on page 245
Setting 16: Differential PID Feedback
If an analog value is set for this function, the PID controller is set for differential feedback. The difference of the PID feedback
input value and the differential feedback input value builds the feedback value used to calculate the PID input.
Feedback Input Methods on page 207
.
Setting 30, 31, 32: DriveWorksEZ Analog Inputs 1, 2, and 3
These settings are for DriveWorksEZ functions. Normally there is no need to change or apply these settings.
u
H4: Multi-Function Analog Outputs
These parameters assign functions to analog output terminals FM and AM for monitoring a specific aspect of drive
performance.
5.7 H: Terminal Functions
YASKAWA ELECTRIC SIEP C710636 04D U1000 Industrial MATRIX Drive Technical Manual
303
5
Parameter Details
Summary of Contents for U1000 iQpump Drive
Page 705: ......