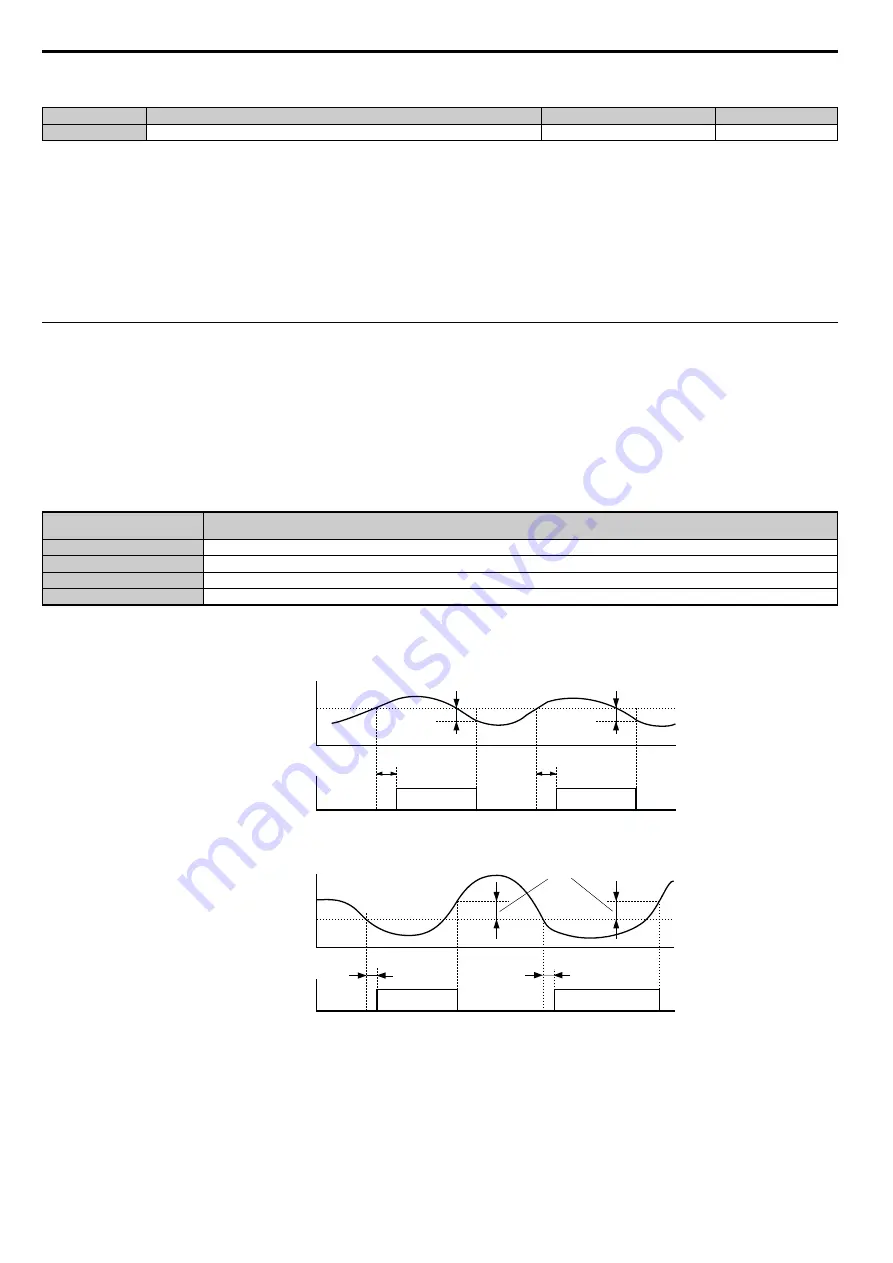
5.8 L: Protection Functions
226
YASKAWA ELECTRIC SIEP C710616 30B YASKAWA AC Drive T1000A Technical Manual
n
L5-05: Fault Reset Operation Selection
Setting 0: Count successful restarts
The drive will continuously attempt to restart. If it restarts successfully, the restart counter is increased. This operation is
repeated each time a fault occurs until the counter reaches the value set in L5-01.
Setting 1: Count restart attempts
The drive will try to restart using the time interval set in parameter L5-04. A record is kept of the number of attempts to
restart to the drive, regardless of whether or not those attempts were successful. When the number of attempted restarts
exceeds the value set to L5-01, the drive gives up trying to restart.
u
L6: Torque Detection
The drive provides two independent torque detection functions that trigger an alarm or fault signal. Make sure an
overtorque alarm will be displayed when necessary in applications that may be damaged from excessive torque. They are
set up using the L6-
parameters. To indicate the underload or overload condition to an external device, digital
outputs should be programmed as shown below.
Note:
The drive can notify the user that an overtorque situation has been reached. This is particularly useful in applications where
overtorque can damage connected machinery. Use the torque detection for this purpose. Use undertorque detection to discover
application problems.
show the function of overtorque and undertorque detection.
Figure 5.86
Figure 5.86 Overtorque Detection Operation
Figure 5.87
Figure 5.87 Undertorque Detection Operation
Note: 1.
The torque detection function uses a hysteresis of 10% of the drive rated output current and motor rated torque.
2.
In V/f, V/f w/PG and OLV/PM, the level is set as a percentage of the drive rated output current. In OLV, CLV, AOLV/PM and CLV/
PM, it is set as a percentage of the motor rated torque.
An analog input signal can be used to set the detection level of torque detection 1 (L6-01).
Analog Input Terminal Settings on page 204
for details on assigning a function to an analog input.
No.
Name
Setting Range
Default
L5-05
Fault Reset Operation Selection
0 or 1
0
H2-01, H2-02, H2-03
Setting
Description
B
Torque detection 1, N.O. (output closes when overload or underload is detected)
17
Torque detection 1, N.C. (output opens when overload or underload is detected
18
Torque detection 2, N.O. (output close when overload or underload is detected)
19
Torque detection 2, N.C. (output opens when overload or underload is detected)
Motor current / torque
L6-02/05
10 % hysteresis
Torque detection 1 (NO)
or
Torque detection 2 (NO)
L6-03/06
ON
L6-03/06
10 % hysteresis
ON
Motor current / torque
L6-02/05
10 % hysteresis
Torque detection 1 (NO)
or
Torque detection 2 (NO)
L6-03/06
ON
L6-03/06
ON