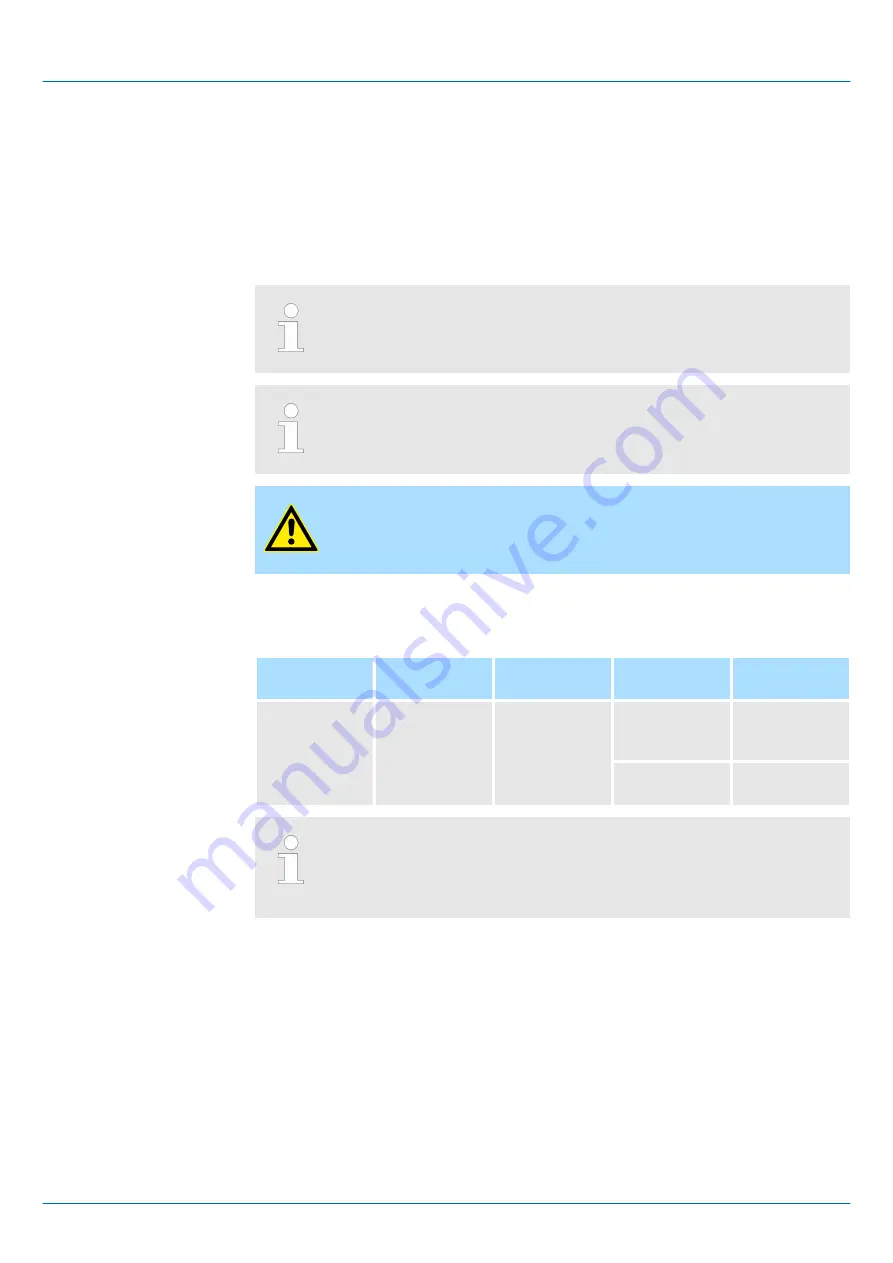
7.14 Forcing the Motor to Stop
7.14.1
Overview
You can force the Servomotor to stop for a signal from the host controller or an external
device.
To force the motor to stop, you must allocate the FSTP (Forced Stop Input) signal in
Pn516 = n.
X. You can specify one of the following stopping methods: dynamic
brake (DB), coasting to a stop, or decelerating to a stop.
Forcing the motor to stop is not designed to comply with any safety
standard. In this respect, it is different from the hard wire base block
(HWBB).
Panel Display and Digital Operator Display
When a forced stop is performed, the panel and the Digital Operator will
display FSTP.
CAUTION!
To prevent accidents that may result from contact faults or disconnec-
tions, use a normally closed switch for the Forced Stop Input signal.
7.14.2
FSTP (Forced Stop Input) Signal
Classification
Signal
Connector Pin
No.
Signal Status
Description
Input
FSTP
Must be allo-
cated.
ON (closed)
Drive is ena-
bled (normal
operation).
OFF (open)
The motor is
stopped.
You must allocate the FSTP signal to use it. Use Pn516 = n.
X
(FSTP (Forced Stop Input) Signal Allocation) to allocate the FSTP signal
to a connector pin. Refer to the following section for details.
Chap. 7.2.2 ‘Input Signal Allocations’ page 196
7.14.3
Stopping Method Selection for Forced Stops
Use Pn00A = n.
X
(Stopping Method for Forced Stops) to set the stopping method
for forced stops.
Sigma-7 Series SERVOPACKs
Application Functions
Forcing the Motor to Stop > Stopping Method Selection for Forced Stops
| | PROFINET Communications - SIEP YEUOC7P 02A Revision 0 | en |
258