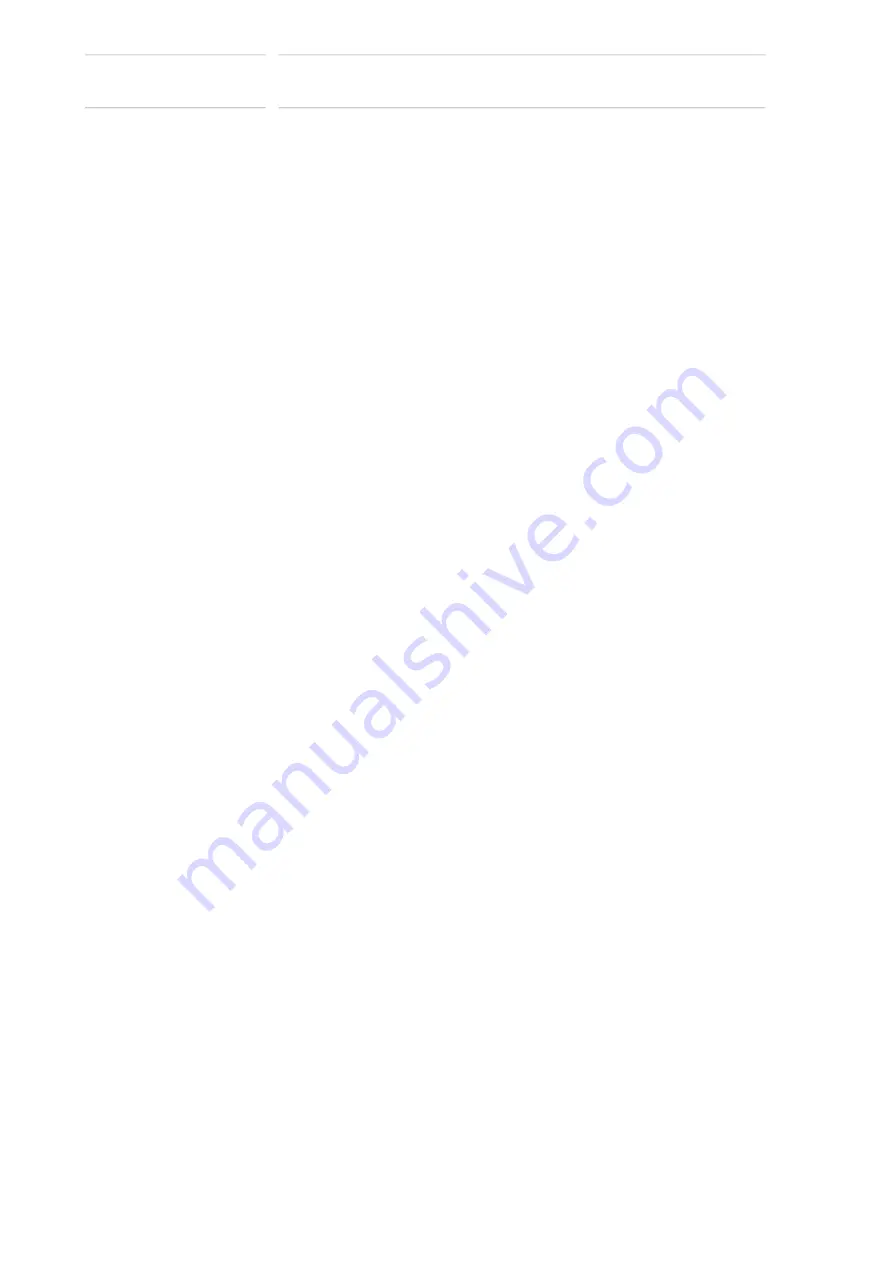
C-25
183523-1CD
183523-1CD
Appendix C
U
RM2-755-RDR Postioner
Tool Center Point (TCP)
The Tool Center Point (TCP) defines the tip of the current tool as defined
relative to the tool flange. For example, for a welding robot, the TCP will
generally be defined at the tip of the welding gun. After defining and
configuring the TCP, the robot motion will be defined relative to this frame
(i.e., rotation in the Rx direction would cause rotation around the X-axis
and positions will be taught in this frame.
Tool Control Point
Tool Coordinates
When the tool attached to the Manipulator moves, so does its tool
coordinate system in reference to a fixed coordinate system, for example,
world coordinates. In general, the tool coordinates do not align with the
world XYZ coordinates.
Tool Frame
A coordinate system attached to the end-effector of a Manipulator (relative
to the base frame).
Total Index Time
Sum of the main axis sweep time and the secondary axis sweep times
Tooling Envelope
Volume in which the tooling can be present when rotated on its own axis
Tooling Fixture
Tooling designed for the application to be mounted on a Positioner axis
where parts will be loaded and processed
Tooling Plate
Plate used to attach tooling to motomounts
Tooling Sweep
Time necessary to rotate tooling between positions
Trajectory Generation (Calculation)
The computation of motion functions that allow the movement of joints in a smooth
controlled manner.
Transducer
A device that converts energy from one form to another. Generally, a
device that converts an input signal into an output signal of a different
form. It can also be thought of as a device which converts static signals
detected in the environment (such as pressure) into an electrical signal
that is sent to a Manipulator's control system.
U
Uptime
A period of time in which a robot or production line is operating or
available to operate, as opposed to downtime.
101 of 104