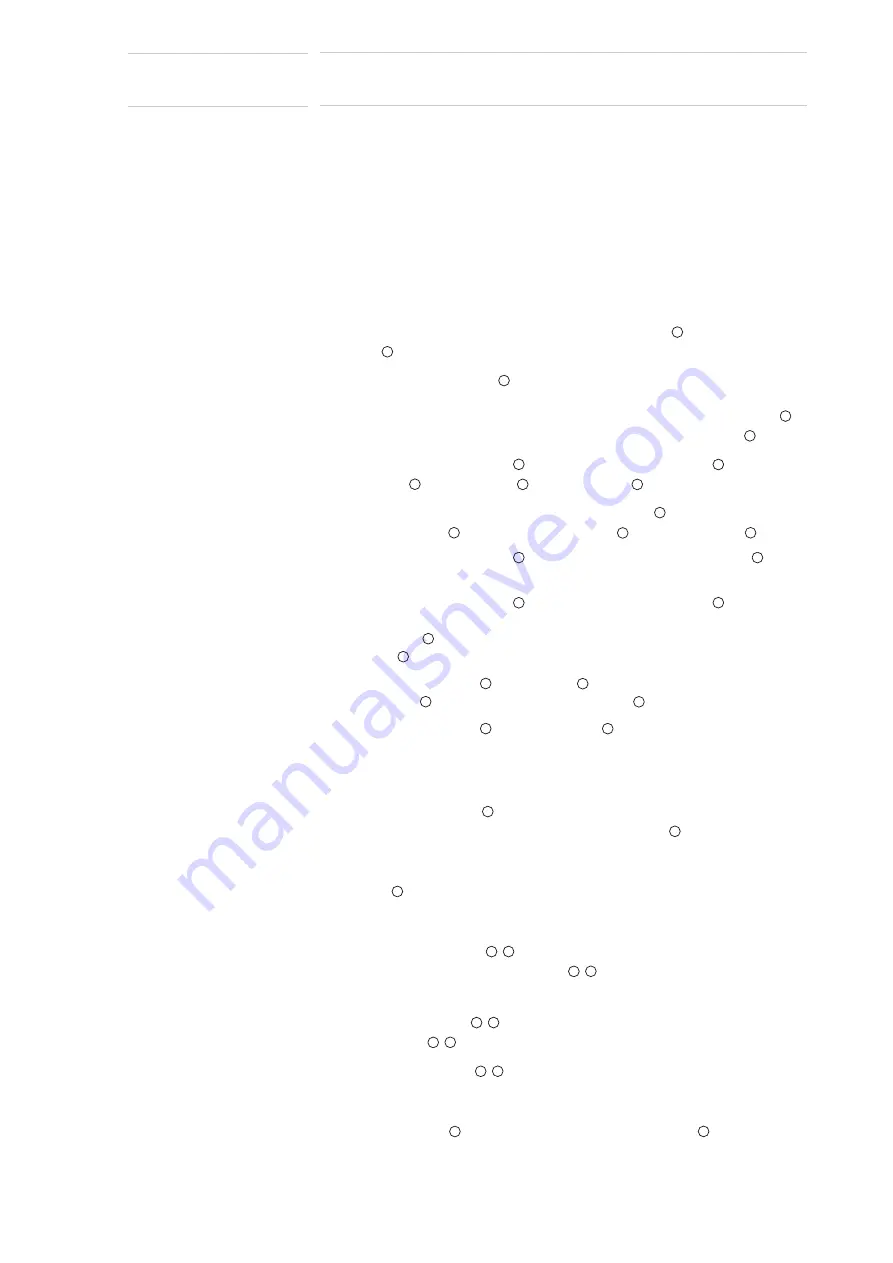
6-4
176183-1CD
HW1483638
6
Disassembly and Reassembly of Speed Reducer
6.2 Disassembly and Reassembly of L-Axis Speed Reducer
MH5S
(II)
/MH5F
6.2
Disassembly and Reassembly of L-Axis Speed Reducer
• Refer to
Fig. 6-2 “Disassembly & Reassembly of the L-Axis Speed
.
Disassembly
1. Turn OFF the DX100/DX200/FS100 power supply.
2. Connect the backup batteries with the L-, U-, R-, B- and T-axes
motors. After disconnect all the cables connected to the internal wiring
harness, pull out the internal wiring harness to the S-head side. (Refer
to
3. Unscrew the hexagon socket button head screws
and remove the
cover
4. Remove the timing belt
Reassembly of L- and U-Axis Timing Belts”
Because the L-arm cannot keep its posture without the timing belt
,
be sure to support the L-arm before removing the timing belt
.
5. Unscrew the GT-SA bolts
. Then remove the housing
, the wave
generator
, the bearings
and the pulley
with the removal tap.
6. Unscrew the hexagon socket head cap screws
from the removed
wave generator
and remove the pulley
and the housing
.
7. Unscrew the GT-SA bolts
. Then remove the circular spline
with
the removal tap.
8. Unscrew the GT-SA bolts
. Then remove the housing
with the
removal tap. Because the L-arm and the S-head are detached without
the housing
, be sure to support the L-arm before removing the
housing
.
9. Remove the bearing
, the oil seal
and the hexagon socket head
cap screws
. Then remove the
flex spline
.
10. Remove the bearing
and the oil seal
.
11. Remove old sealing from each parts.
Reassembly
1. Mount the
flex spline
on the S-head. At this time, apply Harmonic
Grease SK-1A to the inside wall of the flex spline
in thickness of
5mm or so.
2. Attach the conical spring washers to the hexagon socket head cap
screws
and apply ThreeBond 1206C to the thread parts. Then
tighten them with the tightening torque shown in
Speed Reducer Parts Checklist”
.
3. Press fit the bearings
into the S-head. Apply ThreeBond 1206C
to the outside wall of the bearings
and LOCTITE 638 to the
matching face with the S-head. Smooth the surplus sealing or
adhesive with a spatula. However, be careful not to spread the sealing
inside the bearings
. (When replace the speed reducer, replace
the bearings
too.)
4. Press fit the oil seal
into the S-head. (Before the press fit,
remove the sealing adhering to the S-head so that the sealing does
not adhere to the oil seal when press fit into the bearing.)
5. Put the housing
through the L-arm and the bearing
and connect
the S-head with the L-arm.
14
13
15
15
15
6
9
3
16
8
7
3
8
9
4
1
12
11
11
11
17
18
5
2
10
19
2
2
5
10 17
10 17
10 17
10 17
18 19
11
10
51 of 99