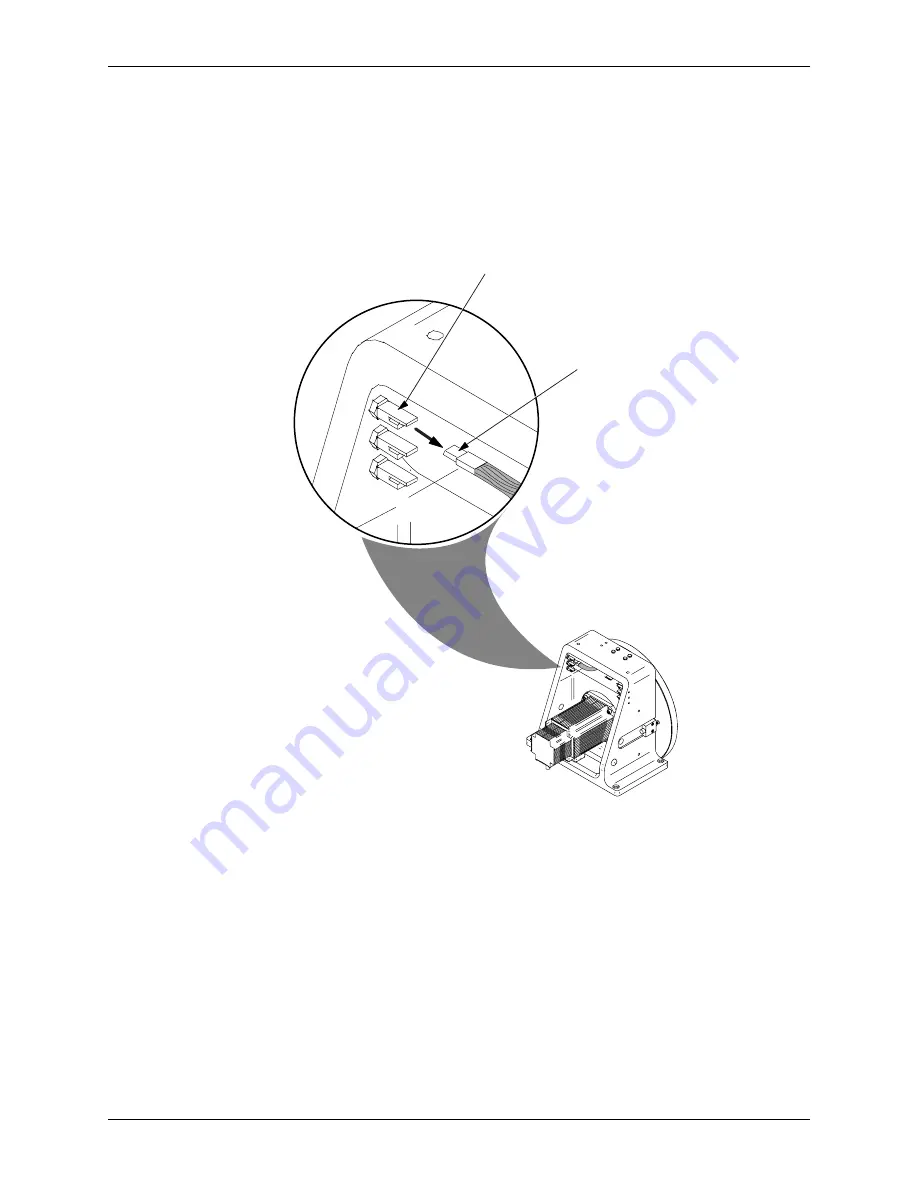
MAINTENANCE
MH-Series with MotoMount Positioner Manual
7-2
MOTO
MAN
7.3
Weld Ground Brush Replacement – Type I
7.3.1
MH75/150/450/1500
To replace the grounding brush(s) proceed as follows:
1. Shut down cell using main disconnect.
2. Use a flathead screwdriver to disconnect the brush cable(s) from the ground
Figure 7-1 Brush Cable Removal
3. Release the spring tensioner on the back of the brush by squeezing both black
spring levers and pulling away from the faceplate.
4. Reach in and steady the brush case with one hand.
5. Use a 7/16-in wrench to loosen and remove the two screws on top of the
housing (see Figure 7-2) that retains the case.
GROUND POST
GROUND BRUSH
CABLE