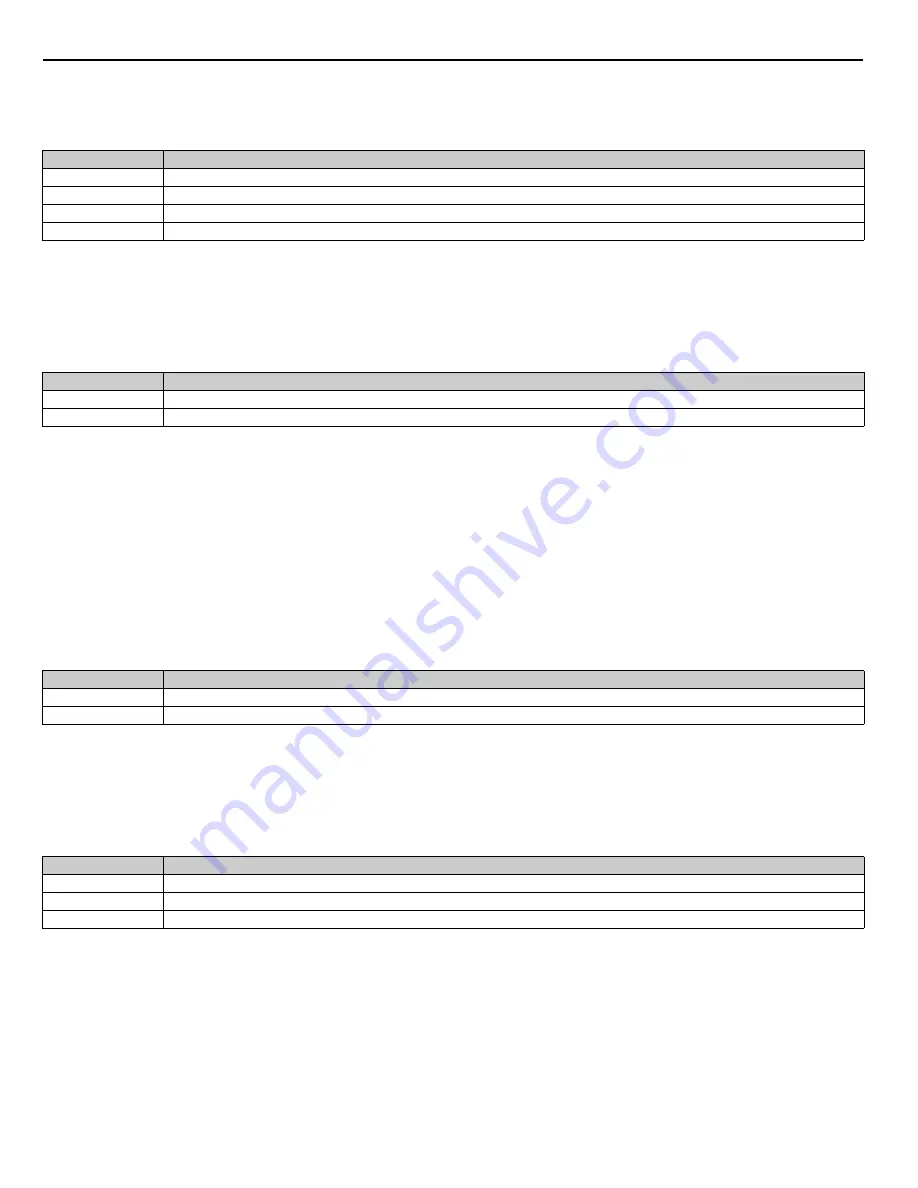
94
YASKAWA
TM.iQp.02 iQpump Drive Programming Manual
It may be necessary to avoid the 19.2 K baud setting if frequent serial communications errors occur at that baud rate.
■
H5-04 Stopping Method after Communication Error
The setting of parameter H5-04 will determine the Drive’s reaction to a serial communications fault such as the CE fault. The iQpump
drive can be programmed to either ramp to a stop in the time specified by C1-02 (H5-04 = “0: Ramp to stop”), coast to a stop (H5-04 =
1), ramp to a stop at the special fast stopping time specified by C1-09 (H5-04 = “2: Fast-Stop”), or continue operating using the
commands received before the serial communication fault and flashing an alarm on the digital operator (H5-04 = “3: Alarm Only”).
■
H5-05 Communications Error Detection Selection
The iQpump drive can be configured by parameter H5-05 to recognize a CE fault whenever serial communications time-out. If H5-05 =
“1: Enabled,” the iQpump drive will fault if serial communication responses are not received within a set period of time determined by
parameter H5-09. iQpump drive power should be cycled after a change is made to this parameter.
■
H5-06 Drive Transit Wait Time
Setting Range:
5 to 65 ms
Factory Default: 5 ms
Parameter H5-06 will set the delay time between the receiving of a message from the master and the sending of a response from the
iQpump drive back to the master. The iQpump drive power should be cycled after a change is made to this parameter.
■
H5-07 RTS Control Selection
RTS or Request To Send control is a method of flow control applied to messaging in serial communications. Parameter H5-07 configures
whether the iQpump drive will implement RTS messaging all the time (H5-07 = “0: Disabled”) or only when sending (H5-07 = “1:
Enabled”). It is recommended to set H5-07 = “0: Disabled,” when using RS-485 and set H5-07 = “1: Enabled,” when using RS-422. The
iQpump drive power should be cycled after a change is made to this parameter.
■
H5-08 Communication Protocol Selection
Since the iQpump drive is capable of using MEMOBUS, Metasys N2, or Apogee FLN communications via the RS-485/422 terminals,
parameter H5-08 must be programmed to specify to the iQpump drive which format is being used. iQpump drive power should be cycled
after a change is made to this parameter.
Setting
Description
0
Ramp to Stop
1
Coast to Stop
2
Fast-Stop
3
Alarm Only (
factory default
)
Setting
Description
0
Disabled
1
Enabled (
factory default
)
Setting
Description
0
Disabled (RTS is always on)
1
Enabled (RTS turns on only when sending) (
factory default
)
Setting
Description
0
Memobus (Modbus) (
factory default
)
1
N2 (Metasys)
2
FLN (APOGEE)
Summary of Contents for CIMR-P7U-2011-107
Page 1: ...iQpump Drive Programming Manual Document Number TM iQp 02 ...
Page 204: ...204 YASKAWA TM iQp 02 iQpump Drive Programming Manual THIS PAGE INTENTIONALLY LEFT BLANK ...
Page 208: ...208 YASKAWA TM iQp 02 iQpump Drive Programming Manual THIS PAGE INTENTIONALLY LEFT BLANK ...
Page 209: ...YASKAWA TM iQp 02 iQpump Drive Programming Manual 209 THIS PAGE INTENTIONALLY LEFT BLANK ...