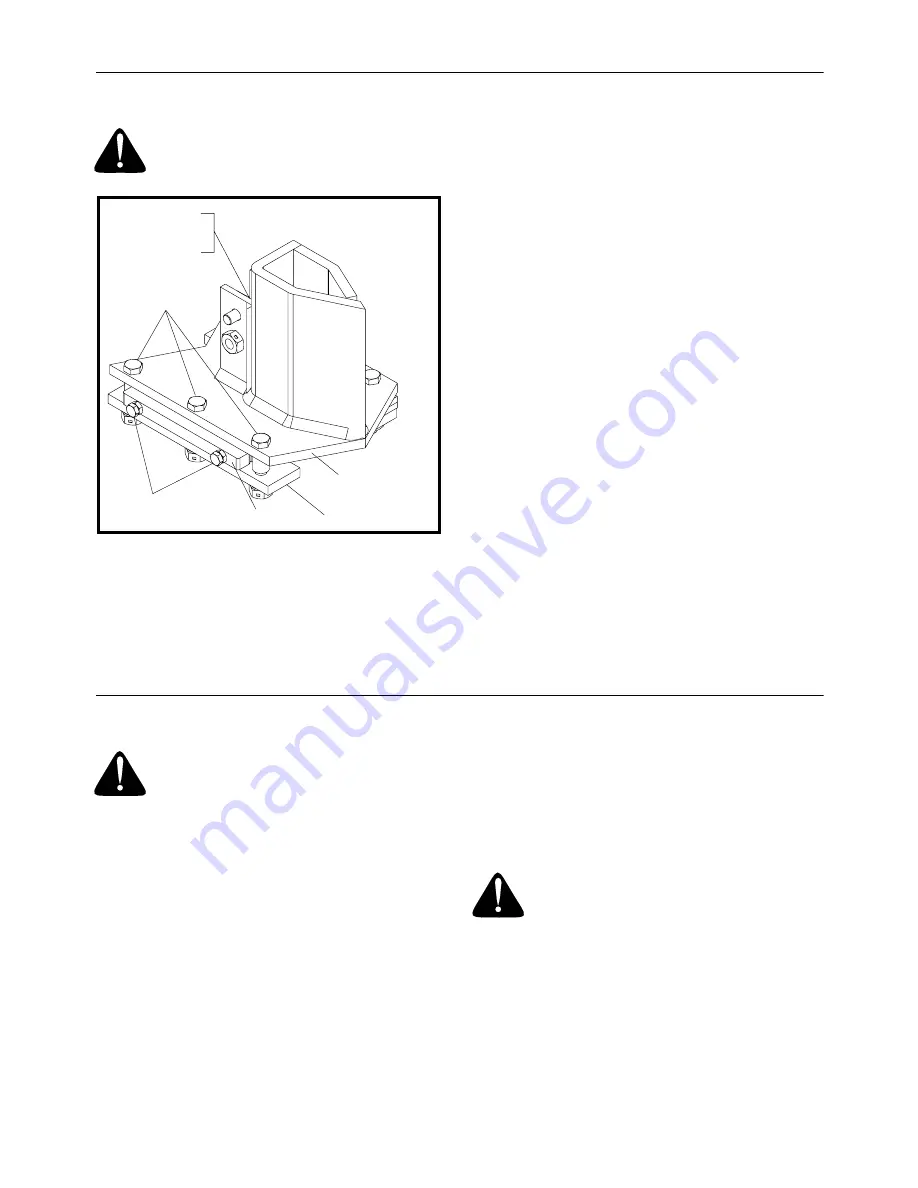
14
SECTION 11: ADJUSTMENTS
WARNING:
Always stop the engine
and disconnect the spark plug wire
before performing any adjustments.
Figure 6
WEDGE PLATE ADJUSTMENT
As normal wear occurs, periodically adjust the bolts
on the side of the wedge plate as follows to
eliminate the excess space between the wedge
plate and the beam. See Figure 6.
Adjust wedge plate as follows:
1.
Loosen the three hex bolts on top of the wedge
plate (beneath the splitting wedge).
2.
Loosen the jam nuts on the two adjustment
bolts on the side of the gib plate, located
beneath the splitting wedge. Turn the
adjustment bolts in until snug, then back them
off slowly until the wedge assembly will slide on
the beam.
3.
Tighten the jam nuts securely against the gib
plate to hold the adjustment bolts in this position.
4.
Retighten the three hex bolts on top of the
wedge plate
GIB PLATE ADJUSTMENT
Periodically remove and replace the “gibs” (spacers)
between the wedge plate and the back plate as
follows. See Figure 6.
NOTE:
If desired, the gibs may be rotated and/or
turned over for even wear.
1.
Remove the center bolt on top of the wedge
plate. Slide the gib plate out.
2.
Remove and replace the gibs. Reassemble the
gib plate, making certain flat washers are in
place under the gib plate.
3.
Readjust the bolts on the side of the wedge
plate as instructed above.
SECTION 12: MAINTENANCE
WARNING:
Always stop the engine
and disconnect the spark plug wire
before performing any maintenance or
repairs.
RESERVOIR FLUID
Check the hydraulic fluid level in the log splitter
reservoir tank before each use. Fluid level should
be 1-1/2" to 2" from the top of the tank.
Change the hydraulic fluid in the reservoir every 100
hours of operation. Disconnect the suction hose
from the bottom of the reservoir tank, and drain the
fluid into a suitable container. Refill using only
Dexron III automatic transmission fluid or 10W non-
foaming hydraulic fluid.
NOTE:
Drain the fluid and flush the reservoir tank
and hoses with kerosene whenever any repair work
is performed on the tank, hydraulic pump or valve.
Contaminants in the fluid will damage the hydraulic
components. (Should be performed by an
authorized service dealer.)
WARNING:
Use extreme caution
when working with kerosene, as it is an
extremely flammable fluid.
HYDRAULIC FILTER
Change the hydraulic filter every 50 hours of
operation. Use only a 10 micron hydraulic filter.
Order part number 723-0405.
Attached
To Cylinder
Gib Plate
Back Plate
Hex Bolts
Adjustment Bolts
Wedge Plate