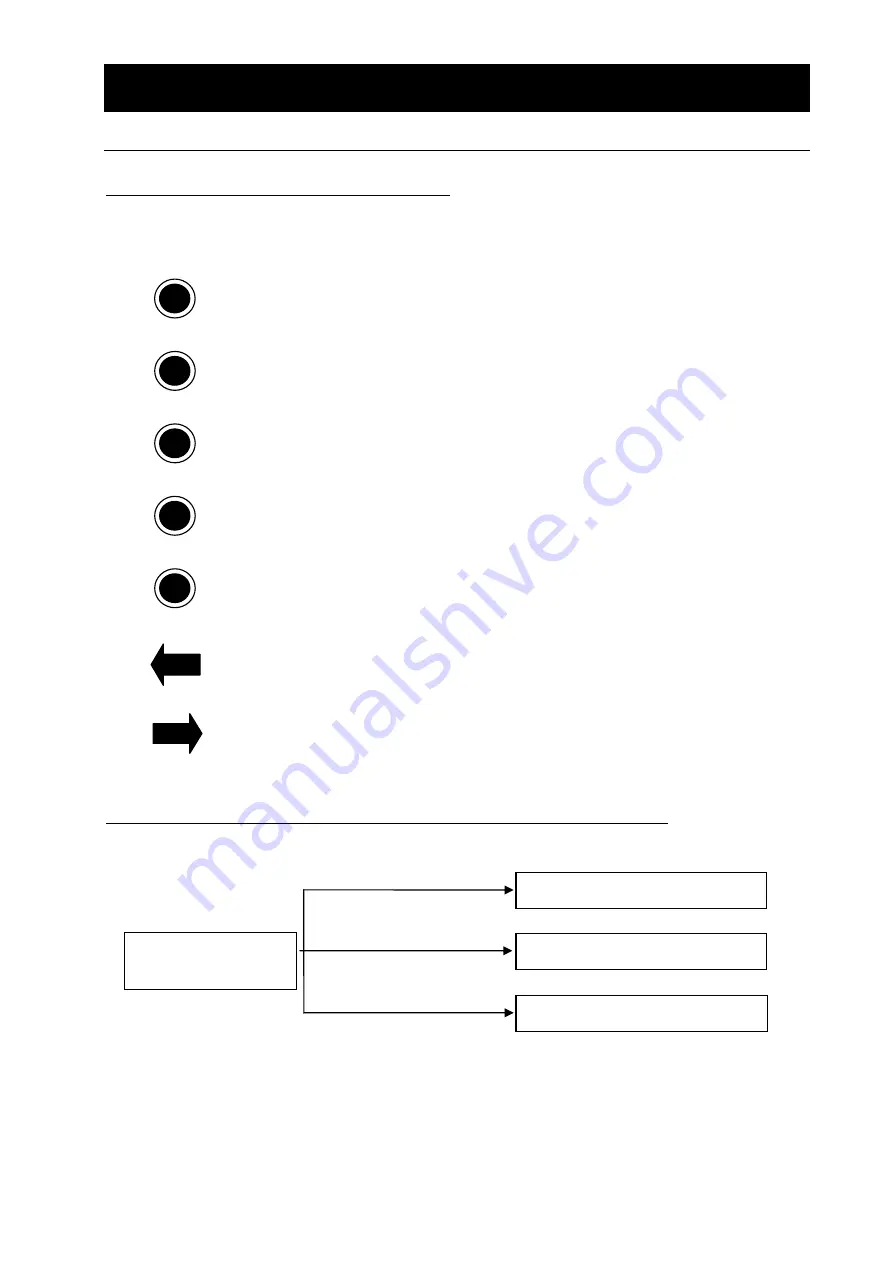
28
4. Operating procedures
Operating method
of GB210A/GB210B
KEY PANEL Description of indication lamps
You can confirm the operating statuses of switches one the KEY PANEL by checking whether a
specific lamp is on or off.
Each lamp will be turned on at the upper right corner on the KEY PANEL.
Lamp on: Indicates that the spray nozzle is attached.
Lamp blink: Indicates that a spray nozzle is not attached.
You can control temperature by setting a temperature on the outlet side
temperature controller while the lamp is on.
*
The lamp is on only when GB210A specifications is used.
You can control temperature by setting a temperature on the inlet side
temperature controller while the lamp is on.
*
The lamp is on only when GB210A specifications is used.
When the lamp is on, the blower is in operation.
When the lamp is on, the blower is in operation.
When the lamp is on, the liquid sending pump is operating in the normal
direction.
When the lamp is on, the liquid sending pump is operating in the normal
direction.
When you want to stop processing of a sample or the nozzle is clogged
Stop sending liquid with the following operations in “Operation method of GB210B".
If you want to process another sample, collect contents in the product container, clean it following
the maintenance procedures (P33 and following pages “6. Maintenance method”), and then operate
the unit with another sample.
PUMP
REV
FWD
PUMP
Heate
Blowe
Outlet
Nozzle
Granulation procedures
(
6
)~(
9
)
Stop processing of
samples
Granulation procedures
(
6
)~(
9
)
Spray drying operation
(
8
)~(
12
)
Granulation operation
Drying of moist powder
Spray drying operation
Summary of Contents for PULVIS MINI SPRAY GB210A
Page 39: ...37 8 When a trouble occurs Confirmation of GB210A manual and language selection display ...
Page 40: ...38 8 When a trouble occurs Confirmation of GB210A manual and language selection display ...
Page 41: ...39 8 When a trouble occurs Confirmation of GB210B manual and language selection display ...
Page 42: ...40 8 When a trouble occurs Confirmation of GB210B manual and language selection display ...