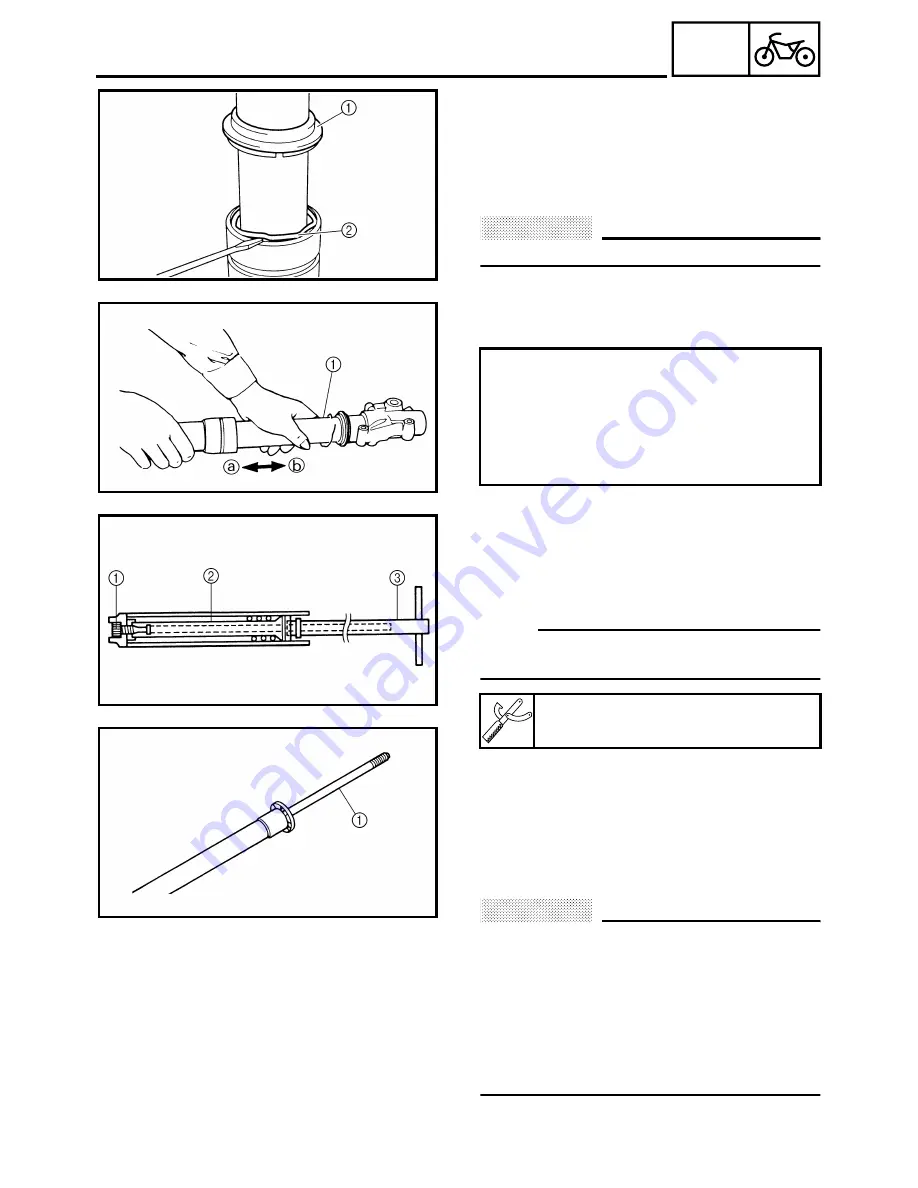
5 - 30
CHAS
EC553201
Inner tube
1. Remove:
●
Dust seal
1
●
Stopper ring
2
Using slotted-head screwdriver.
ACHTUNG:
CAUTION:
Take care not to scratch the inner tube.
2. Remove:
●
Inner tube
1
Oil seal removal steps:
●
Push in slowly
a
the inner tube just before
it bottoms out and then pull it back quickly
b
.
●
Repeat this step until the inner tube can
be pulled out from the outer tube.
EC553311
Damper rod
1. Remove:
●
Base valve
1
●
Damper rod
2
NOTE:
Use a damper rod holder
3
to lock the damper
rod.
EC554000
INSPECTION
EC554100
Damper rod
1. Inspect:
●
Damper rod
1
Bend/damage
→
Replace damper rod.
ACHTUNG:
CAUTION:
The front fork with a built-in piston rod has
a very sophisticated internal construction
and is particularly sensitive to foreign
material.
Use enough care not to allow any foreign
material to come in when the oil is replaced
or when the front fork is disassembled and
reassembled.
Damper rod holder:
YM-1423/90890-01423
FRONT FORK
Summary of Contents for WR450F(R)
Page 1: ...LIT 11626 16 43 WR450FR 5TJ 28199 10 OWNER S SERVICE MANUAL ...
Page 2: ......
Page 5: ......
Page 12: ...MEMO ...