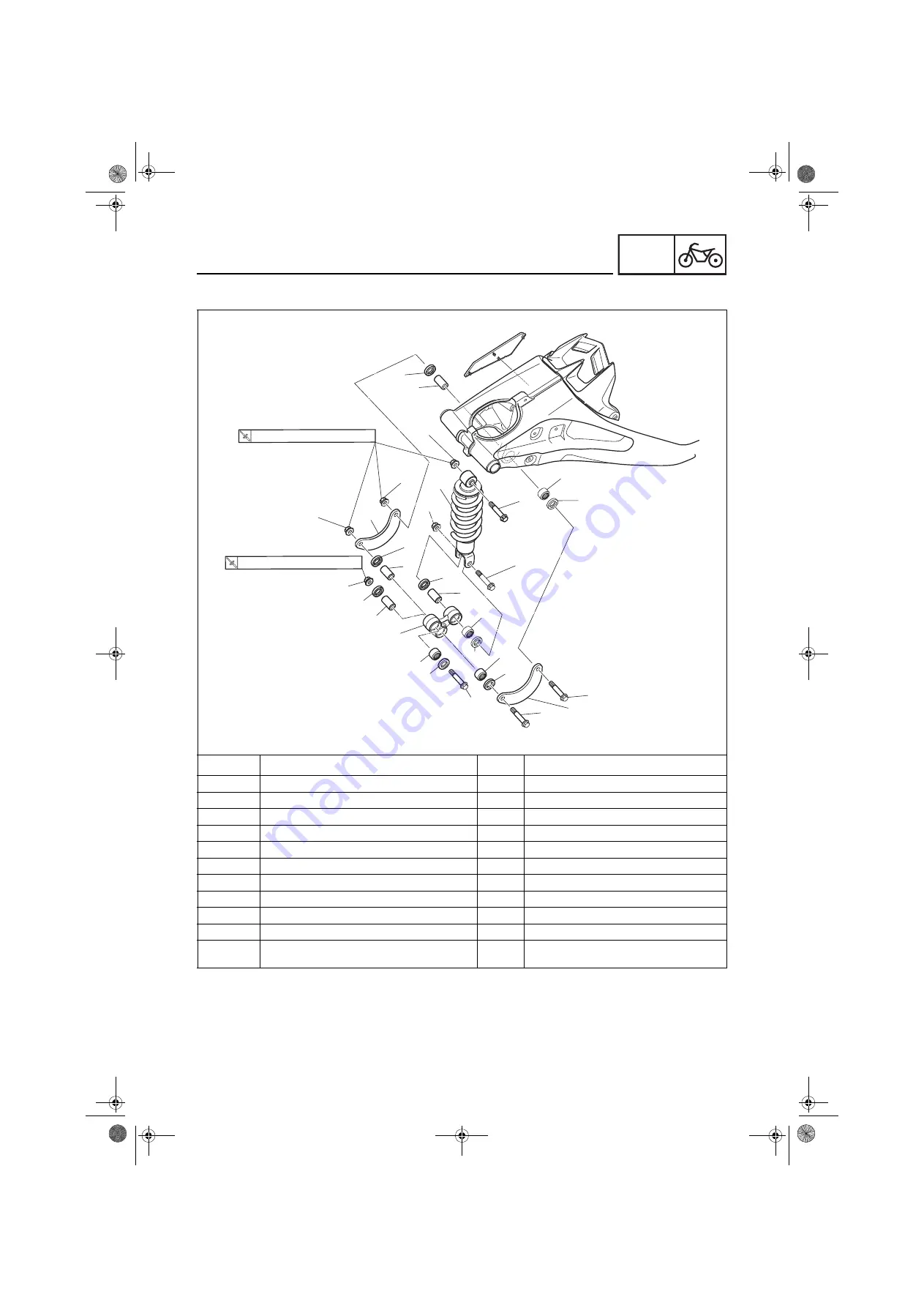
4-79
REAR SHOCK ABSORBER ASSEMBLY
CHAS
EAS20036
REAR SHOCK ABSORBER ASSEMBLY
Removing the rear shock absorber assembly
Order
Job/Parts to remove
Q’ty
Remarks
1
Rear shock absorber assembly lower nut/bolt
1/1
2
Rear shock absorber assembly upper nut/bolt
1/1
3
Connecting arm nut/bolt
2/2
M10
×
63 mm
4
Relay arm along with connecting arm
1
5
Rear shock absorber assembly
1
6
Relay arm nut/bolt
1/1
7
Connecting arm
2
8
Spacer
4
9
Oil seal
8
10
Bearing
4
For installation, reverse the removal proce-
dure.
8
1
2
3
3
4
3
1
2
5
6
6
7
8
9
7
8
8
9
9
9
9
10
10
10
10
9
9
9
3
NOTE
: Apply “Lithium-soap-based grease” on part serial number :- 1,2,3,6,8,9,10
44
(4.4 kgf·m, 32 lb·ft)
N·m
44
(4.4 kgf·m, 32 lb·ft)
N·m
BCWF8197E0.book Page 79 Thursday, November 18, 2021 9:18 AM
Summary of Contents for R15 2022
Page 6: ...BCWF8197E0 book Page 2 Thursday November 18 2021 9 18 AM...
Page 56: ...1 49 GEN INFO SPECIAL TOOLS BCWF8197E0 book Page 49 Thursday November 18 2021 9 18 AM...
Page 109: ...2 52 CABLE ROUTING SPEC ABS System BCWF8197E0 book Page 52 Thursday November 18 2021 9 18 AM...
Page 142: ...3 30 ELECTRICAL SYSTEM CHK ADJ BCWF8197E0 book Page 30 Thursday November 18 2021 9 18 AM...
Page 308: ...5 71 TRANSMISSION ENG BCWF8197E0 book Page 71 Thursday November 18 2021 9 18 AM...
Page 330: ...7 11 THROTTLE BODY FI BCWF8197E0 book Page 11 Thursday November 18 2021 9 18 AM...
Page 333: ...BCWF8197E0 book Page 2 Thursday November 18 2021 9 18 AM...
Page 344: ...8 11 CHARGING SYSTEM ELEC BCWF8197E0 book Page 11 Thursday November 18 2021 9 18 AM...
Page 348: ...8 15 LIGHTING SYSTEM ELEC BCWF8197E0 book Page 15 Thursday November 18 2021 9 18 AM...
Page 360: ...8 27 COOLING SYSTEM ELEC BCWF8197E0 book Page 27 Thursday November 18 2021 9 18 AM...
Page 488: ...8 155 ELECTRICAL COMPONENTS ELEC BCWF8197E0 book Page 155 Thursday November 18 2021 9 18 AM...
Page 495: ...BCWF8197E0 book Page 1 Thursday November 18 2021 9 18 AM...
Page 496: ...1Y245 SM 01 1578 10 21 E BCW F8197 E0 BCWF8197E0 book Page 2 Thursday November 18 2021 9 18 AM...