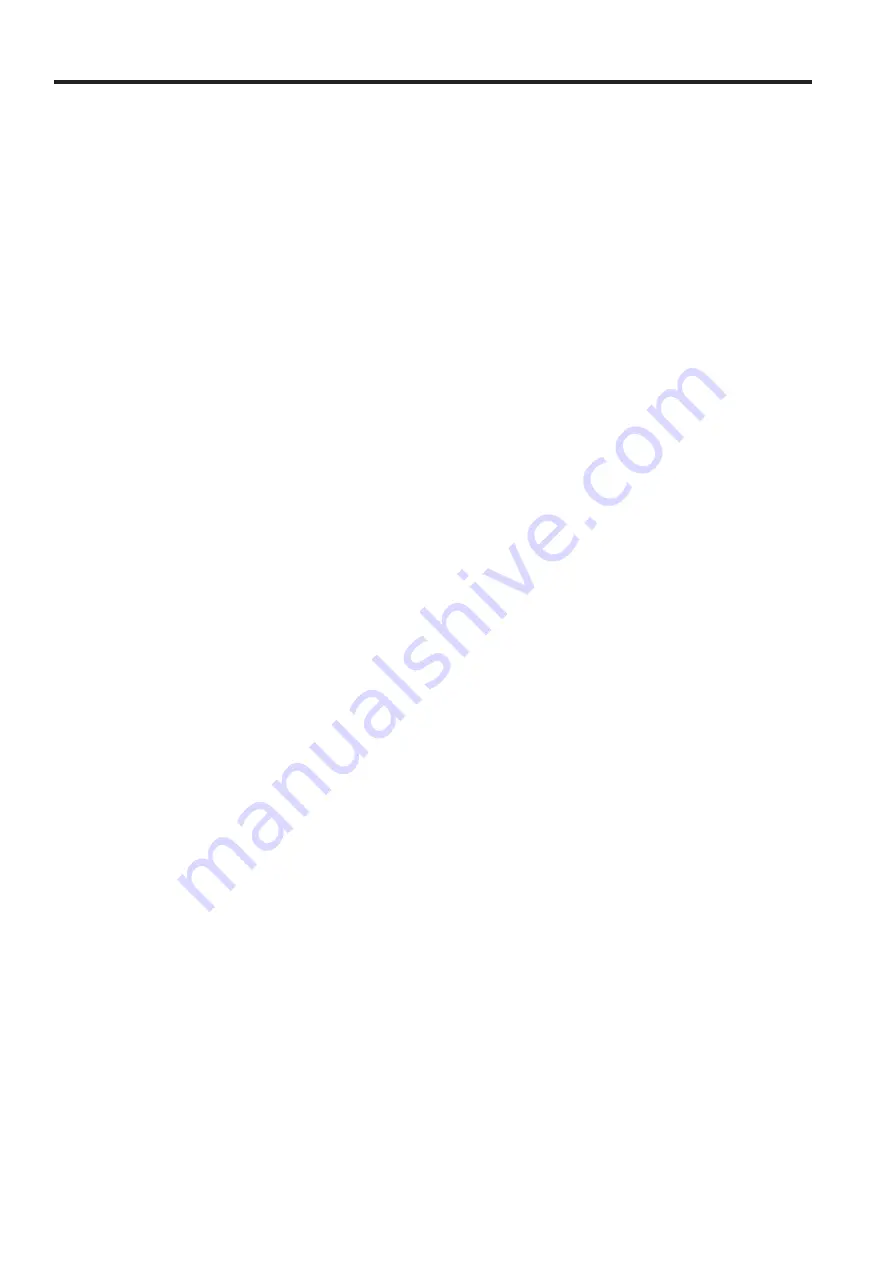
16
SERVICING
CERAMIC PLUNGER REMOVAL
1. Remove seal retainer (B) from each plunger rod.
See figure 10 page 19
.
2. Using a 10 mm hex tool, loosen the plunger
retainer bolt (E) on each plunger rod.
3. Remove the ceramic plunger (C) and washer (D)
from each chamber. Depending on the model
pump, there may be a copper retainer gasket on
each plunger retainer. Replace the copper plunger
retainer gasket with an NBR seal washer.
4. Visually inspect the crankcase oil seals (A) for
deterioration or leaks.
5. Examine washers (D) and replace if cut or worn.
6. Examine plunger seal retainers (B) for damage and
replace as needed.
7. Examine the ceramic plungers (C) for scoring,
scale buildup, chips or cracks and replace as
needed. The ceramic plungers (C) do not need to
be replaced with every seal servicing.
NOTE:
Examine the manifold chamber walls, seal
chambers, and valve chambers for scale buildup
or damage, clean if needed.
See figure 9, page 18
.
Clean the manifold throughly.
VALVE ASSEMBLY REPLACEMENT
1. Examine spring retainers (F and J) for internal wear
or breaks in the structure and replace as needed.
See figure 8, page 18
.
2. Examine springs (D) for fatigue or breaks and
replace as needed.
3. Examine valves (C and I) and seats (E) for grooves,
pitting or wear and replace as needed.
4. Examine o-ring (B) for cuts or wear and replace
as needed.
5. Lubricate with silicon grease and install new o-ring
(K) onto large outside diameter of discharge spring
retainer (J). Depending on model of pump, you
may need to reinstall the backup-ring prior to the
o-ring.
6. Place seat (E) on work surface with small diameter
side up.
7. Place valve (I) onto seat (E) with concave side
down.
8. Place spring (D) on valve (I).
9. Install spring retainer (F) with deep stepped end
over spring (D) and snap onto seat (E).
10. Snap discharge valve assembly onto the inlet
valve assembly and press into valve chamber until
completely seated.
11. Lubricate with silicon grease and install new O-ring
(B) onto each valve plug (A).
12. Apply thin coat Loctite 242 to threads of each
valve plug (A) and thread in hand tight. Torque to
specs per chart.
SOAP INJECTOR ASSEMBLY
REPLACEMENT
1. Examine O-rings, check valves, and spring for
fatigue or breaks and replace as needed.
See
figure 15, page 20
.
2. Install O-ring inside the soap nozzle.
3. Install ball bearing inside soap nozzle.
4. Install spring inside soap nozzle.
5. Attatch soap nozzle onto soap injector assembly.
6. Install O-ring (P) inside soap injector chamber.
7. Install check valve (Q) and check valve with O-ring
(R) inside soap injector chamber.
8. Install spring (S) inside soap injector chamber.
9. Install O-ring (T) onto soap injector assembly.
10. Attatch soap injector assembly (U) to soap injector
chamber.
UNLOADER REPLACEMENT
1. If seat (N) is worn or damaged, press new seat
into unloader chamber until squarely seated.
See
figure 15, page 20
.
2. Examine piston stem (H), washer (I), valve retainer
(K) and valve (M) for grooves, pitting or wear and
replace as needed. Examine o-rings (J and L) and
back-up ring (X) for cuts or wear and replace as
needed.
3. Lubricate and install o-ring (G) and back-up ring
(X) over slotted head of piston stem, then position
back-up ring on top of o-ring.
4. Lubricate and install o-rings (L) on valve retainer
(K).
5. Install washer (I) and then valve retainer (K) with
o-rings onto piston stem (H). Apply Locktite 242
to threads of piston stem (H) and screw valve (M)
onto piston stem (H).
6. Lower complete piston stem and valve assembly
into unloader chamber with valve facing downward.
7. Examine piston retainer (E) for damaged threads
or wear and replace as needed. Examine o-ring
(F) for cuts or wear and replace as needed.
8. Apply Locktite 242 to threads of lower portion of
piston retainer (E) into unloader body by turning
in a clockwise direction and then tighten with
wrench.