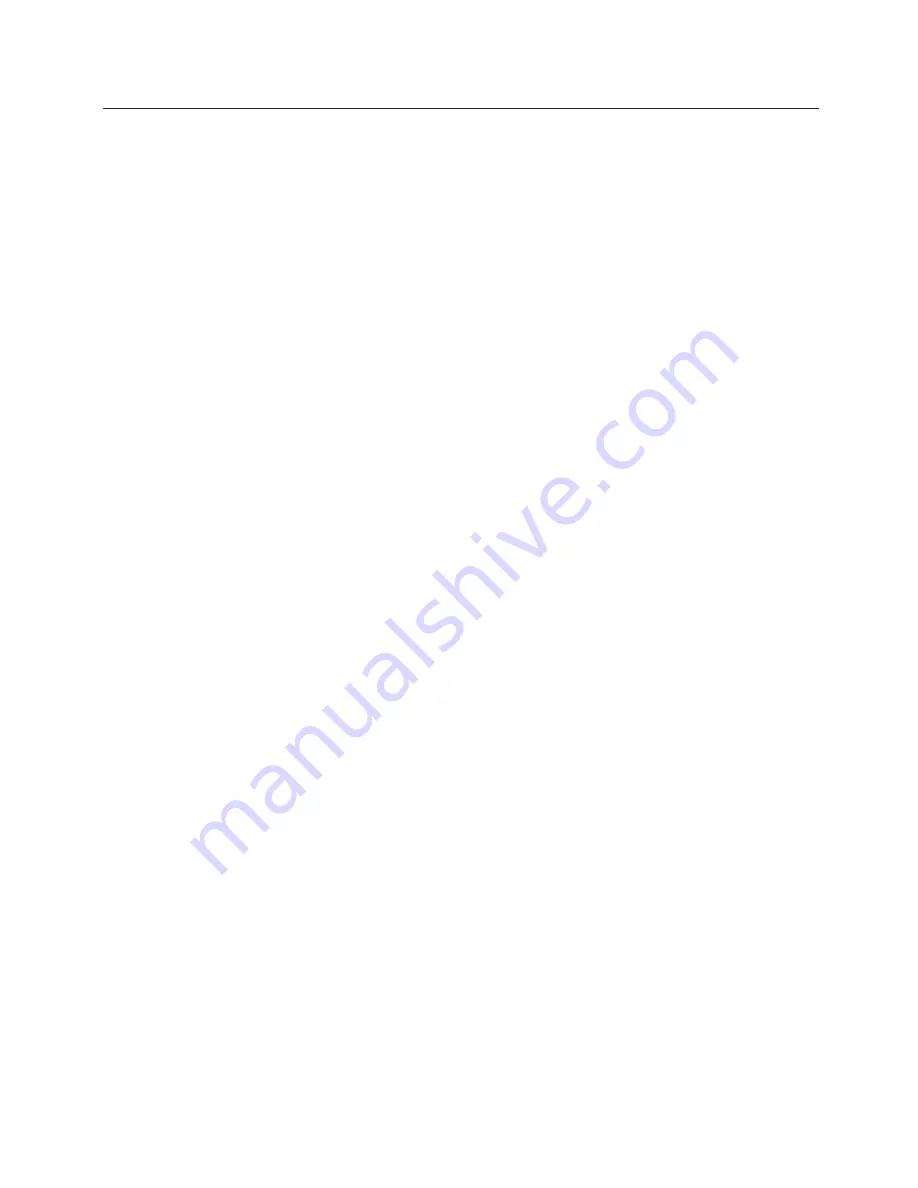
TABLE OF CONTENTS
GENERAL INFORMATION
SYMBOLS . . . . . . . . . . . . . . . . . . . . . . . . . . . . . . . . . . . . . . . . . . . . . . . . . . . . . . . . . . . . . . . . 1
IDENTIFICATION NUMBERS . . . . . . . . . . . . . . . . . . . . . . . . . . . . . . . . . . . . . . . . . . . . . . . . . 3
SPECIFICATIONS
GENERAL SPECIFICATIONS . . . . . . . . . . . . . . . . . . . . . . . . . . . . . . . . . . . . . . . . . . . . . . . . . 4
MAINTENANCE SPECIFICATIONS . . . . . . . . . . . . . . . . . . . . . . . . . . . . . . . . . . . . . . . . . . . . . 5
ENGINE . . . . . . . . . . . . . . . . . . . . . . . . . . . . . . . . . . . . . . . . . . . . . . . . . . . . . . . . . . . . . . . 6
JET UNIT . . . . . . . . . . . . . . . . . . . . . . . . . . . . . . . . . . . . . . . . . . . . . . . . . . . . . . . . . . . . . . 6
HULL AND HOOD . . . . . . . . . . . . . . . . . . . . . . . . . . . . . . . . . . . . . . . . . . . . . . . . . . . . . . . 7
ELECTRICAL . . . . . . . . . . . . . . . . . . . . . . . . . . . . . . . . . . . . . . . . . . . . . . . . . . . . . . . . . . . 7
PERIODIC INSPECTION AND ADJUSTMENT
MAINTENANCE INTERVAL CHART . . . . . . . . . . . . . . . . . . . . . . . . . . . . . . . . . . . . . . . . . . . . 9
ELECTRICAL SYSTEM
STEREO HARNESS . . . . . . . . . . . . . . . . . . . . . . . . . . . . . . . . . . . . . . . . . . . . . . . . . . . . . . . 10
STEREO HARNESS #5 REPLACEMENT . . . . . . . . . . . . . . . . . . . . . . . . . . . . . . . . . . . . . . . 11
METER PANEL BACK VIEW WIRING DIAGRAM . . . . . . . . . . . . . . . . . . . . . . . . . . . . . . . . . 12
METER PANEL BACK VIEW EXPLODED DIAGRAM . . . . . . . . . . . . . . . . . . . . . . . . . . . . . . . 13
OIL SWITCH . . . . . . . . . . . . . . . . . . . . . . . . . . . . . . . . . . . . . . . . . . . . . . . . . . . . . . . . . . . . . 14
FUEL GAUGE . . . . . . . . . . . . . . . . . . . . . . . . . . . . . . . . . . . . . . . . . . . . . . . . . . . . . . . . . . . . 14
FUEL LEVEL SENSOR/LOW OIL SWITCH . . . . . . . . . . . . . . . . . . . . . . . . . . . . . . . . . . . . . . 14
TROUBLE ANALYSIS
TROUBLE ANALYSIS . . . . . . . . . . . . . . . . . . . . . . . . . . . . . . . . . . . . . . . . . . . . . . . . . . . . . . 15
WIRING DIAGRAM . . . . . . . . . . . . . . . . . . . . . . . . . . . . . . . . . . . . . . . . . . . . . . . . . . . . . . . . 16
Summary of Contents for LST1200X1999
Page 1: ...LS2000 LX210 AR210 LIT 18616 SB 01 1999 2003 ALL LST1200 LS2000 MODELS ...
Page 2: ......
Page 3: ......
Page 4: ......
Page 5: ......
Page 6: ......
Page 7: ......
Page 8: ......
Page 9: ......
Page 10: ......
Page 11: ......
Page 12: ......
Page 13: ......
Page 14: ......
Page 15: ......
Page 16: ......
Page 17: ......
Page 18: ......
Page 19: ......
Page 20: ......
Page 21: ......
Page 22: ......
Page 23: ......
Page 24: ......
Page 25: ......
Page 26: ......
Page 27: ......
Page 28: ......
Page 29: ......
Page 30: ......
Page 31: ......
Page 32: ......
Page 33: ......
Page 34: ......
Page 35: ......
Page 36: ......
Page 37: ......
Page 38: ......
Page 39: ......
Page 40: ......
Page 41: ......
Page 42: ......
Page 43: ......
Page 44: ......
Page 45: ......
Page 46: ......
Page 47: ......
Page 48: ......
Page 49: ......
Page 50: ......
Page 51: ......
Page 52: ......
Page 53: ......
Page 54: ......
Page 55: ......
Page 56: ......
Page 57: ......
Page 58: ......
Page 59: ......
Page 60: ......
Page 61: ......
Page 62: ......
Page 63: ......
Page 64: ......
Page 65: ......
Page 66: ......
Page 67: ......
Page 68: ......
Page 69: ......
Page 70: ......
Page 71: ......
Page 72: ......
Page 73: ......
Page 74: ......
Page 75: ......
Page 76: ......
Page 77: ......
Page 78: ......
Page 79: ......
Page 80: ......
Page 81: ......
Page 82: ......
Page 83: ......
Page 84: ......
Page 85: ......
Page 86: ......
Page 87: ......
Page 88: ......
Page 89: ......
Page 90: ......
Page 91: ......
Page 92: ......
Page 93: ......
Page 94: ......
Page 95: ......
Page 96: ......
Page 97: ......
Page 98: ......
Page 99: ......
Page 100: ......
Page 101: ......
Page 102: ......
Page 103: ......
Page 104: ......
Page 105: ......
Page 106: ......
Page 107: ......
Page 108: ......
Page 109: ......
Page 110: ......
Page 111: ......
Page 112: ......
Page 113: ......
Page 114: ......
Page 115: ......
Page 116: ......
Page 117: ......
Page 118: ......
Page 119: ......
Page 120: ......
Page 121: ......
Page 122: ......
Page 123: ......
Page 124: ......
Page 125: ......
Page 126: ......
Page 127: ......
Page 128: ......
Page 129: ......
Page 130: ......
Page 131: ......
Page 132: ......
Page 133: ......
Page 134: ......
Page 135: ......
Page 136: ......
Page 137: ......
Page 138: ......
Page 139: ......
Page 140: ......
Page 141: ......
Page 142: ......
Page 143: ......
Page 144: ......
Page 145: ......
Page 146: ......
Page 147: ......
Page 148: ......
Page 149: ......
Page 150: ......
Page 151: ......
Page 152: ......
Page 153: ......
Page 154: ......
Page 155: ......
Page 156: ......
Page 157: ......
Page 158: ......
Page 159: ......
Page 160: ...2000 LST1200Y Supplementary Service Manual ...
Page 179: ...14 FUEL SYSTEM EXPLODED DIAGRAM FUEL SYSTEM x 4 FUEL ...
Page 181: ...16 FUEL PUMP EXPLODED DIAGRAM FUEL SYSTEM 4 FUEL ...
Page 184: ...19 ELECTRICAL SYSTEM x 7 ELEC ELECTRICAL SYSTEM WIRING DIAGRAM ...
Page 185: ...20 ELECTRICAL SYSTEM 7 ELEC HULL HARNESS ...
Page 187: ...22 ENGINE HARNESS ELECTRICAL SYSTEM 7 ELEC ...
Page 189: ...24 DECK HARNESS ELECTRICAL SYSTEM 7 ELEC ...
Page 191: ...26 ELECTRICAL SYSTEM 7 ELEC STEREO HARNESS ...
Page 199: ...34 BIMINI TOP HULL AND DECK 8 HULL DECK ...
Page 201: ...36 REMOTE CONTROL SYSTEM EXPLODED DIAGRAM HULL AND DECK 8 HULL DECK ...
Page 203: ...38 HATCH FITTINGS EXPLODED DIAGRAM HULL AND DECK 8 HULL DECK ...
Page 205: ...40 HELM POD ASSEMBLY EXPLODED DIAGRAM HULL AND DECK 8 HULL DECK ...
Page 207: ...2001 LST1200Z Supplementary Service Manual ...
Page 221: ...12 FUEL SYSTEM 4 FUEL FUEL SYSTEM EXPLODED DIAGRAM ...
Page 225: ...16 STEREO HARNESS ELECTRICAL SYSTEM 7 ELEC ...
Page 235: ... 2000 YAMAHA MOTOR CORPORATION USA LIT 18616 02 29 ...
Page 236: ...2002 LST1200A A A Supplementary Service Manual ...
Page 248: ...10 STEREO HARNESS ELECTRICAL SYSTEM 7 ELEC ...
Page 255: ... 2001 YAMAHA MOTOR CORPORATION USA LIT 18616 02 41 ...
Page 268: ...10 STEREO HARNESS ELECTRICAL SYSTEM 7 ELEC 4 2 3 ...
Page 277: ... 2003 YAMAHA MOTOR CORPORATION USA LIT 18616 03 41 ...