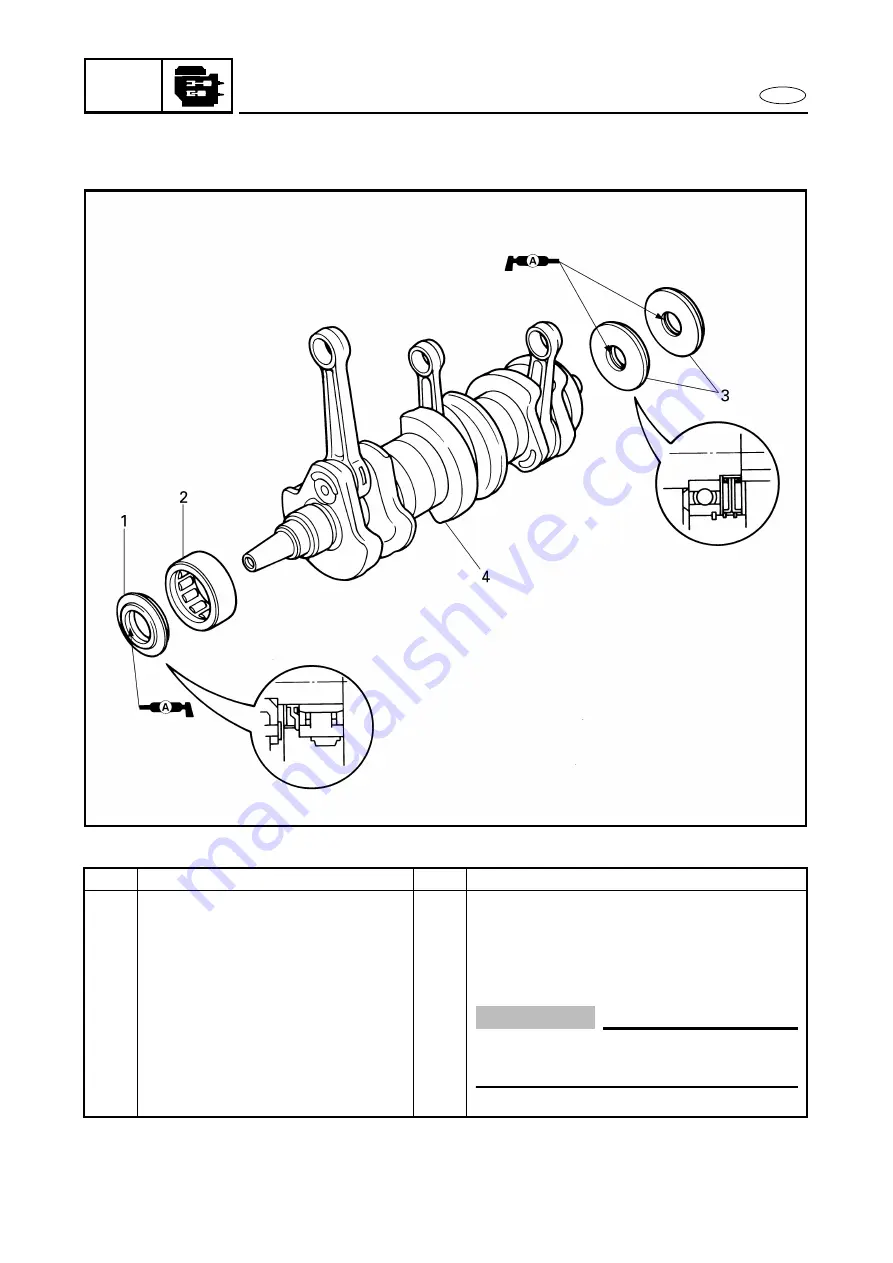
5-45
POWR
E
CRANKSHAFT
CRANKSHAFT
EXPLODED DIAGRAM
REMOVAL AND INSTALLATION CHART
Step
Procedure/Part name
Q’ty
Service points
CRANKSHAFT REMOVAL
Follow the left “Step” for removal.
Crankcase
Refer to “CRANKCASE”.
1
Oil seal
1
2
Bearing
1
3
Oil seal
2
4
Crankshaft assembly
1
CAUTION:
Install the bearing locating pins into the
gloves in the crankcase body.
Reverse the removal steps for installation.