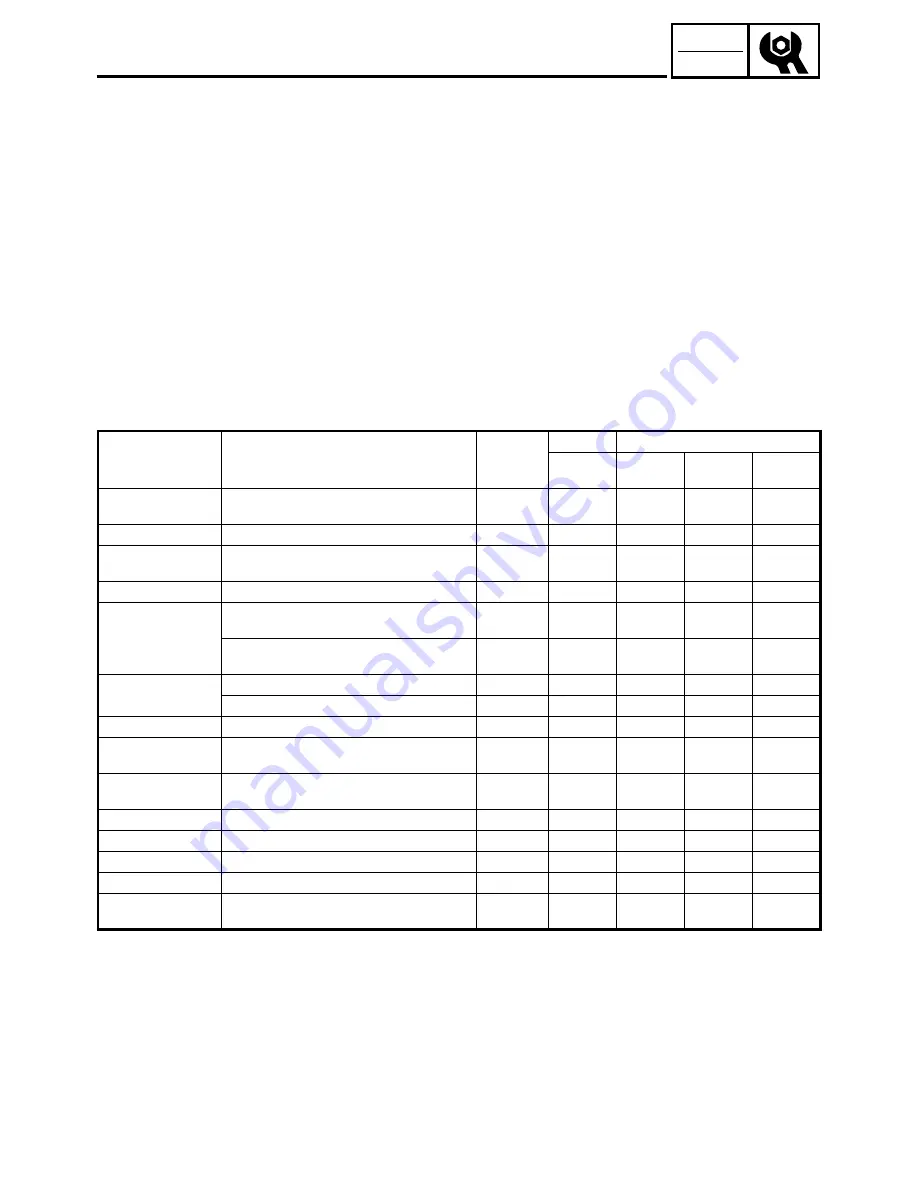
2-1
INSP
ADJ
INTRODUCTION/MAINTENANCE INTERVALS CHART/
PERIODIC MAINTENANCE/LUBRICATION INTERVALS
PERIODIC INSPECTIONS AND ADJUSTMENTS
INTRODUCTION
This chapter includes all information necessary to perform recommended inspections and adjust-
ments. These preventive maintenance procedures, if followed, will ensure more reliable machine
operation and a longer service life. The need for costly overhaul work will be greatly reduced. This
information applies to machines already in service as well as new machines that are being prepared
for sale. All service technicians should be familiar with this entire chapter.
MAINTENANCE INTERVALS CHART
Proper periodic maintenance is important. Especially important are the maintenance services
related to emissions control. These controls not only function to ensure cleaner air but are also vital
to proper engine operation and maximum performance. In the following maintenance tables, the
services related to emissions control are indicated as “*” in the chart.
PERIODIC MAINTENANCE/LUBRICATION INTERVALS
*: Related to emission control system.
Item
Remarks
Pre-Opera-
tion check
(daily)
Initial
Every
1 month or
20 Hr
3 months
or 50 Hr
6 months
or 100 Hr
12 months
or 300 Hr
*Spark plug
Check condition, adjust gap and clean.
Replace if necessary.
●
*Valve clearance
Check and adjust when engine is cold.
●
*Crankcase breather
system
Check breather hose for cracks or damage.
Replace if necessary.
●
*Idle speed
Check and adjust engine idle speed.
●
*Exhaust system
Check for leakage.
Retighten or replace gasket if necessary.
●
Check muffler screen and spark arrester.
Clean/replace if necessary.
●
Engine oil
Check oil level.
●
Replace.
●
●
*Air filter
Clean. Replace if necessary.
●
Fuel filter
Clean fuel cock and fuel tank filter.
Replace if necessary.
●
Fuel line
Check fuel hose for cracks or damage.
Replace if necessary.
●
*Choke knob
Check choke operation.
●
Cooling system
Check for fan damage.
●
Starting system
Check recoil starter operation.
●
*Decarbonization
More frequently if necessary.
●
Fittings/fasteners
Check all fittings and fasteners.
Correct if necessary.
●
Summary of Contents for EF2800i - Inverter Generator
Page 1: ...SERVICE MANUAL EF2800i LIT 19616 00 92 7VU 28197 10 310115 ...
Page 2: ......
Page 8: ......
Page 28: ......
Page 101: ......
Page 102: ...PRINTED ON RECYCLED PAPER PRINTED IN USA YAMAHA MOTOR CO LTD E ...