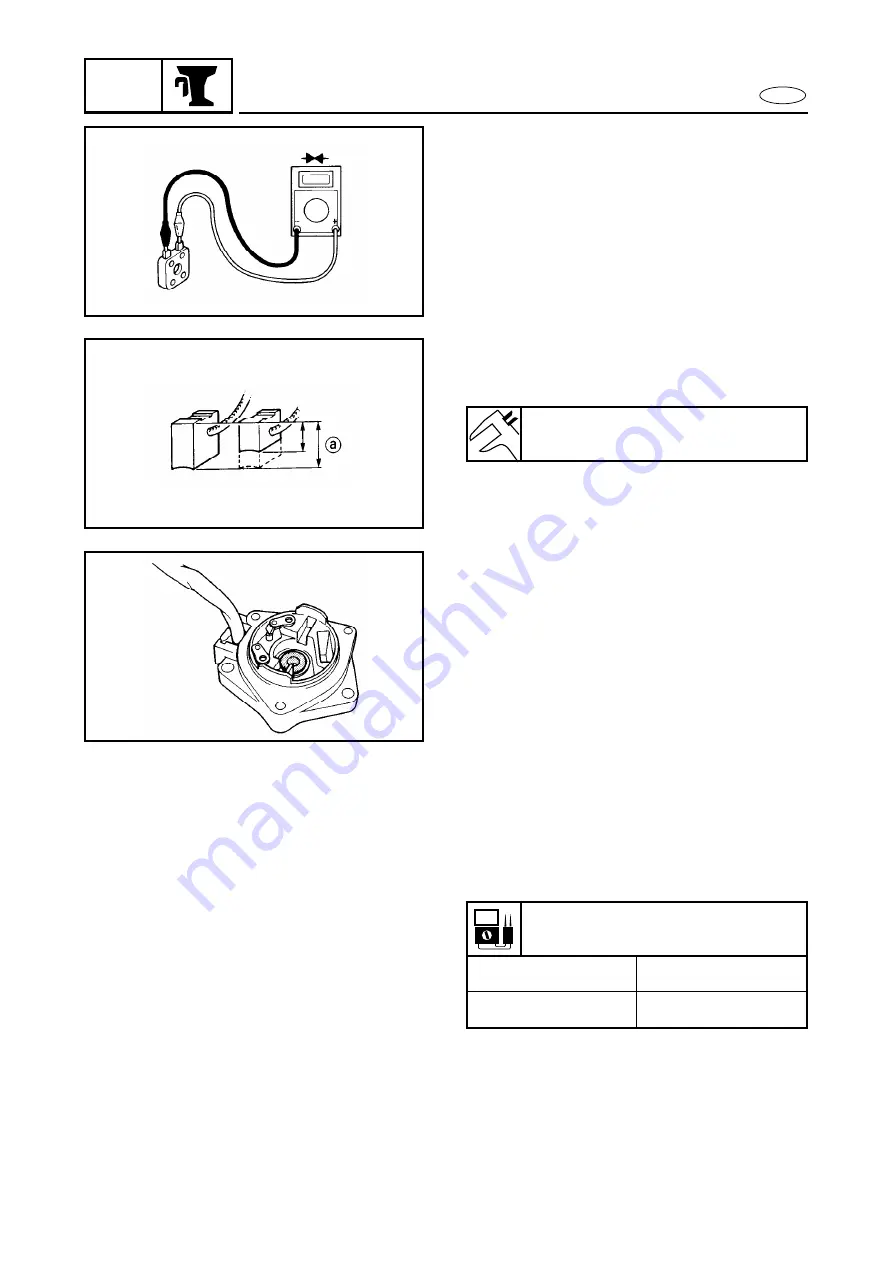
7-38
BRKT
E
PTT MOTOR
5. Inspect:
●
Circuit breaker
Discontinuity
→
Replace.
6. Inspect:
●
Lead wire
Discontinuity
→
Replace.
7. Measure:
●
Brush length
a
Out of specification
→
Replace.
Brush length
a
:
Limit 3.5 mm (0.14 in)
8. Inspect:
●
Base
Crack/Damage
→
Replace.
9. Inspect:
●
Stator bushing
●
Base bushing
Wear/Damage
→
Replace the stator
or the base.
10. Inspect:
●
Base oil seal
Wear/Damage
→
Replace.
Motor assembly
1. Check:
●
Motor operation
Out of specification
→
Repair.
Motor operation:
Blue (+), Green (–)
Clockwise
Green (+), Blue (–)
Counterclockwise
Summary of Contents for 40ER
Page 1: ...LIT 18616 01 81 290320 SERVICE MANUAL 40V 50H WORLD WIDE 40W 50W USA CANADA ...
Page 8: ......
Page 16: ...1 7 GEN INFO E SPECIAL TOOLS ...
Page 18: ...1 9 GEN INFO E SPECIAL TOOLS ...
Page 20: ......
Page 33: ...2 12 SPEC E MAINTENANCE SPECIFICATIONS ...
Page 34: ...2 13 SPEC E MAINTENANCE SPECIFICATIONS DIMENSION 1 ...
Page 36: ...2 15 SPEC E MAINTENANCE SPECIFICATIONS DIMENSION 2 MANUAL TILT MODEL HYDRO TILT PTT MODEL ...
Page 40: ......
Page 58: ...4 5 FUEL E CARBURETOR REMOVAL CARBURETOR REMOVAL EXPLODED DIAGRAM ...
Page 60: ...4 7 FUEL E CARBURETOR CARBURETOR EXPLODED DIAGRAM ...
Page 64: ...4 11 FUEL E PRIME STARTER PRIME STARTER EXPLODED DIAGRAM ...
Page 67: ...4 14 FUEL E PRIME STARTER ...
Page 68: ...4 15 FUEL E OIL TANK OIL TANK EXPLODED DIAGRAM ...
Page 72: ...4 19 FUEL E OIL PUMP OIL PUMP EXPLODED DIAGRAM ...
Page 76: ...5 1 POWR E POWER UNIT REMOVAL POWER UNIT REMOVAL EXPLODED DIAGRAM ...
Page 78: ...5 3 POWR E RECOIL STARTER RECOIL STARTER EXPLODED DIAGRAM ...
Page 83: ...5 8 POWR E RECOIL STARTER ...
Page 87: ...5 12 POWR E FLYWHEEL MAGNETO AND MAGNETO BASE ...
Page 88: ...5 13 POWR E ELECTRICAL UNIT REMOVAL ELECTRICAL UNIT REMOVAL EXPLODED DIAGRAM Å ...
Page 90: ...5 15 POWR E ELECTRICAL UNIT ELECTRICAL UNIT EXPLODED DIAGRAM ...
Page 92: ...5 17 POWR E REED VALVE AND CHECK VALVE REED VALVE AND CHECK VALVE EXPLODED DIAGRAM ...
Page 95: ...5 20 POWR E REED VALVE AND CHECK VALVE ...
Page 100: ...5 25 POWR E CRANKCASE AND CYLINDER BODY CRANKCASE AND CYLINDER BODY EXPLODED DIAGRAM ...
Page 102: ...5 27 POWR E CRANKCASE AND CYLINDER BODY EXPLODED DIAGRAM ...
Page 106: ...5 31 POWR E CRANK SHAFT AND PISTON CRANK SHAFT AND PISTON EXPLODED DIAGRAM ...
Page 113: ......
Page 116: ...6 1 LOWR E LOWER UNIT REMOVAL LOWER UNIT REMOVAL EXPLODED DIAGRAM ...
Page 118: ...6 3 LOWR E WATER PUMP WATER PUMP EXPLODED DIAGRAM ...
Page 120: ...6 5 LOWR E PROPELLER SHAFT AND REVERSE GEAR PROPELLER SHAFT AND REVERSE GEAR EXPLODED DIAGRAM ...
Page 125: ...6 10 LOWR E PROPELLER SHAFT AND REVERSE GEAR ...
Page 128: ...6 13 LOWR E DRIVE SHAFT FORWARD GEAR AND SHIFT ROD EXPLODED DIAGRAM ...
Page 145: ......
Page 148: ...7 1 BRKT E TILLER HANDLE REMOVAL TILLER HANDLE REMOVAL EXPLODED DIAGRAM ...
Page 150: ...7 3 BRKT E TILLER HANDLE TILLER HANDLE EXPLODED DIAGRAM ...
Page 152: ...7 5 BRKT E TILLER HANDLE EXPLODED DIAGRAM ...
Page 154: ...7 7 BRKT E LINK ASS Y DISASSEMBLY LINK ASS Y DISASSEMBLY EXPLODED DIAGRAM ...
Page 158: ...7 11 BRKT E UPPER CASE REMOVAL UPPER CASE REMOVAL EXPLODED DIAGRAM ...
Page 160: ...7 13 BRKT E UPPER CASE AND EXHAUST MANIFOLD UPPER CASE AND EXHAUST MANIFOLD EXPLODED DIAGRAM ...
Page 162: ...7 15 BRKT E CLAMP BRACKET CLAMP BRACKET Manual tilt EXPLODED DIAGRAM ...
Page 164: ...7 17 BRKT E CLAMP BRACKET CLAMP BRACKET Hydro tilt Power trim and tilt EXPLODED DIAGRAM ...
Page 166: ...7 19 BRKT E STEERING BRACKET STEERING BRACKET EXPLODED DIAGRAM ...
Page 168: ...7 21 BRKT E SWIVEL BRACKET SWIVEL BRACKET EXPLODED DIAGRAM ...
Page 170: ...7 23 BRKT E SWIVEL BRACKET DISASSEMBLY SWIVEL BRACKET DISASSEMBLY EXPLODED DIAGRAM ...
Page 172: ...7 25 BRKT E TILT UNIT REMOVAL TILT UNIT REMOVAL EXPLODED DIAGRAM ...
Page 176: ...7 29 BRKT E TILT CYLINDER TILT CYLINDER EXPLODED DIAGRAM ...
Page 180: ...7 33 BRKT E PUMP HOUSING PUMP HOUSING EXPLODED DIAGRAM ...
Page 182: ...7 35 BRKT E PTT MOTOR PTT MOTOR EXPLODED DIAGRAM ...
Page 209: ...8 22 ELEC E STARTING SYSTEM ...
Page 210: ...8 23 ELEC E STARTER MOTOR STARTER MOTOR EXPLODED DIAGRAM ...
Page 224: ...YAMAHA MOTOR Corporation USA Printed in U S A Printed on recycled paper ...