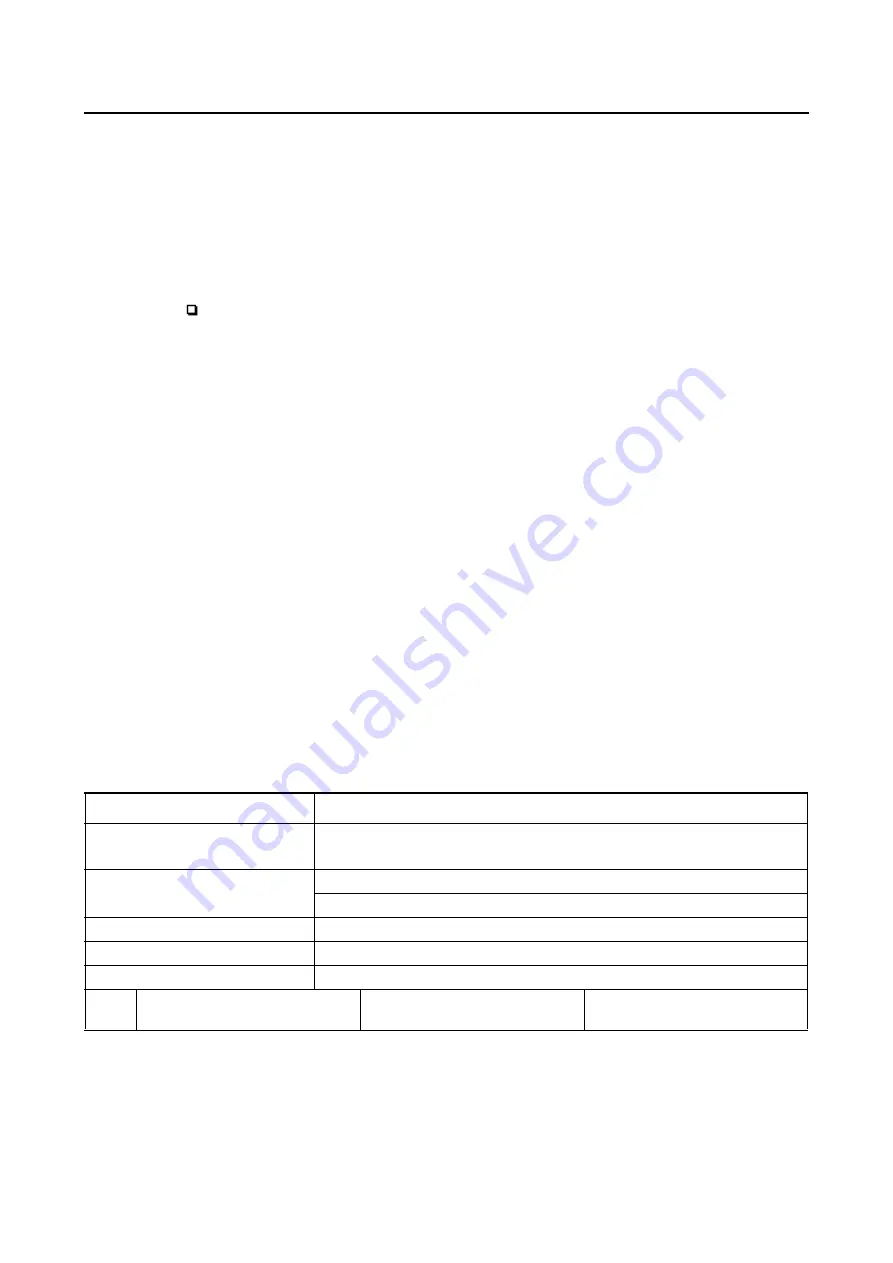
FUEL INJECTION SYSTEM
9-35
5. Item
The item names of the detected malfunction are displayed.
6. Condition
The current conditions are displayed. (Detected/Recovered)
7. Symptom
The symptoms of the detected malfunction are displayed.
8. Diagnosis code
The diagnosis codes related to the detected malfunction are displayed.
9. FFD (only for models that can display freeze frame data)
The mark “ ” is displayed when the freeze frame data is available.
10.ECU conduction time (hour: minute: second)
The total ECU conduction time (total hours the vehicle’s main switch was ON) when the malfunction
was detected is displayed.
11.Number of main switch operation after detection
The number of times the main switch was turned on between the malfunction detection and code
reading is displayed.
12.Number of occurrences
The number of malfunction occurrences between the malfunction detection and code reading is dis-
played.
EBS30281
TROUBLESHOOTING DETAILS (FUEL INJECTION SYSTEM)
This section describes the measures per fault code number displayed on the Yamaha diagnostic tool
or multi-function meter display. Check and service the items or components that are the probable cause
of the malfunction following the order given.
After the check and service of the malfunctioning part has been completed, reset the Yamaha diagnos-
tic tool or multi-function meter display according to the “Confirmation of service completion”.
Fault code No.:
Fault code number displayed on the Yamaha diagnostic tool or multi-function meter when the engine
failed to work normally.
Diagnostic code No.:
Diagnostic code number to be used when the diagnostic mode is operated.
Refer to “SELF-DIAGNOSTIC FUNCTION AND DIAGNOSTIC CODE TABLE” on page 10-7.
Fault code No. 12
Fault code No.
12
Item
Crankshaft position sensor: no normal signals are received from the
crankshaft position sensor.
Fail-safe system
Unable to start engine
Unable to drive vehicle
Diagnostic code No.
—
Indicated
—
Procedure
—
Item
Probable cause of malfunc-
tion and check
Maintenance job
Confirmation of service com-
pletion
Summary of Contents for 2016 Grizzly yfm700gplg
Page 6: ......
Page 8: ......
Page 11: ...IDENTIFICATION 1 2 ...
Page 37: ...ENGINE SPECIFICATIONS 2 6 Air induction system Solenoid resistance 18 22 Ω ...
Page 58: ...LUBRICATION SYSTEM CHART AND DIAGRAMS 2 27 EBS30023 LUBRICATION DIAGRAMS 6 7 8 9 3 4 3 2 1 5 ...
Page 60: ...LUBRICATION SYSTEM CHART AND DIAGRAMS 2 29 1 2 3 4 5 ...
Page 62: ...COOLING SYSTEM DIAGRAMS 2 31 EBS20021 COOLING SYSTEM DIAGRAMS 1 2 3 10 9 8 6 7 5 4 ...
Page 78: ...CABLE ROUTING 2 47 Front and rear brake hoses F 3 F 3 F 3 3 I G H 4 4 B C D 2 E D 2 A 1 ...
Page 80: ...CABLE ROUTING 2 49 ...
Page 83: ......
Page 119: ...PERIODIC MAINTENANCE 3 36 A Headlight left and right B Handle mounted light b a 1 A b a 1 B ...
Page 120: ...PERIODIC MAINTENANCE 3 37 ...
Page 197: ...REAR ARMS AND REAR SHOCK ABSORBER ASSEMBLIES 4 74 7 9 8 9 7 3 5 4 5 3 6 2 10 10 1 ...
Page 198: ...REAR ARMS AND REAR SHOCK ABSORBER ASSEMBLIES 4 75 ...
Page 203: ...ENGINE INSPECTION 5 2 Top cover Refer to GENERAL CHASSIS 2 on page 4 6 ...
Page 244: ...ELECTRIC STARTER 5 43 a b b 1 2 3 ...
Page 316: ...AIR INDUCTION SYSTEM 7 9 EBS20057 AIR INDUCTION SYSTEM 3 4 1 2 3 4 1 2 ...
Page 352: ...REAR CONSTANT VELOCITY SHAFT ASSEMBLIES FINAL DRIVE ASSEMBLY AND REAR DRIVE SHAFT 8 31 ...
Page 355: ......
Page 365: ...ELECTRIC STARTING SYSTEM 9 10 ...
Page 369: ...CHARGING SYSTEM 9 14 ...
Page 417: ...FUEL PUMP SYSTEM 9 62 ...
Page 434: ...ELECTRICAL COMPONENTS 9 79 1 2 3 5 7 8 9 10 11 12 13 14 15 16 17 18 19 4 6 ...
Page 454: ...ELECTRICAL COMPONENTS 9 99 ...
Page 468: ......
Page 469: ......
Page 470: ......