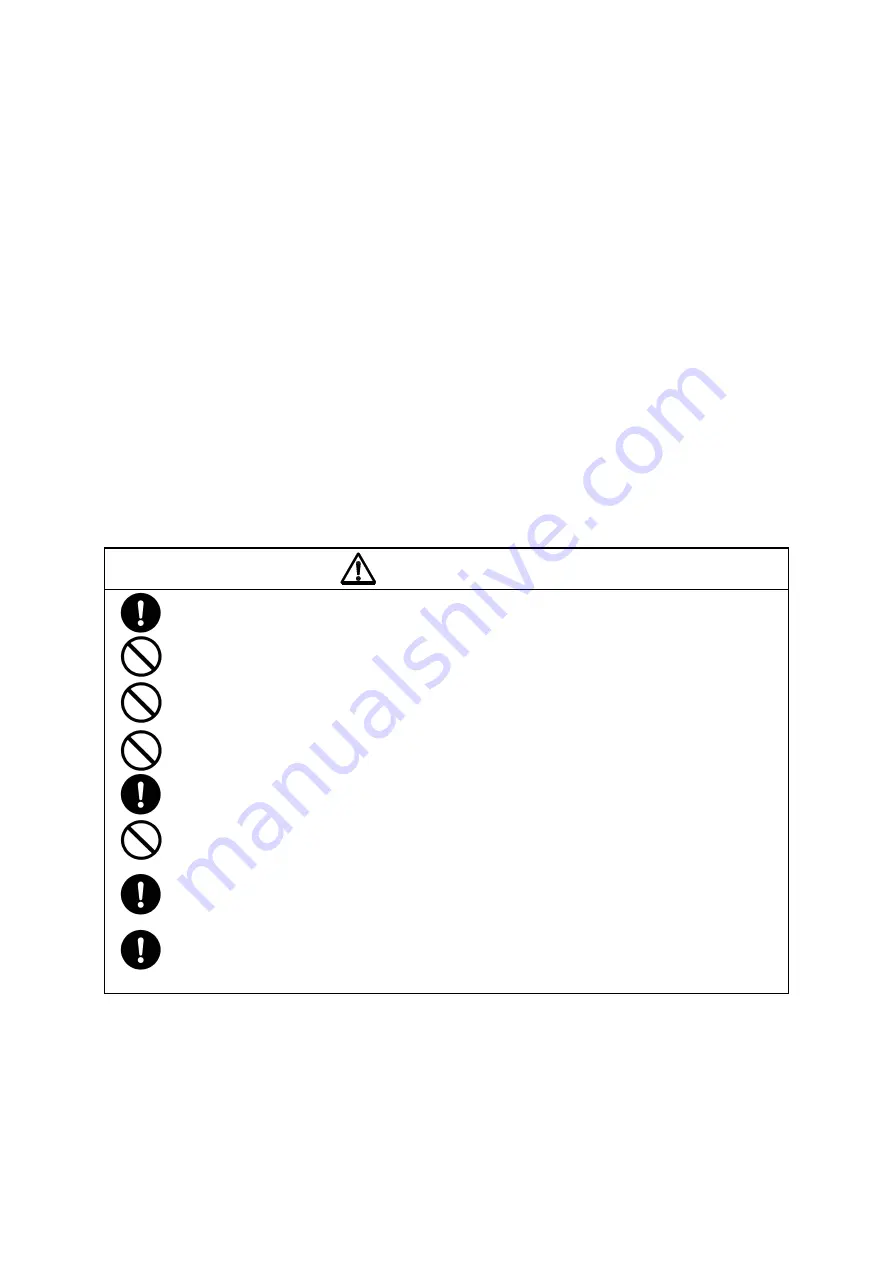
7
3.2 Placement of drum
1
)
Adjust the lift control switch to “DOWN” before turning on air supply.
2
)
Gradually increase lift air pressure up to 0.4MPa by adjusting the lift air regulator knob. Then adjust the lift
control switch to “UP” to raise the lift to the full height.
3
)
Turn the air release plug on the inductor plate 3-4 times counterclockwise to loosen it.
4
)
Place a drum right under the inductor plate. Turn the switch to “DOWN” to lower the lift. Turn the switch to
“STOP” when the inductor plate has reached 2-3 cm above a drum. Then, readjust the position of a drum.
5
)
Again, set the lift control switch to “DOWN”. The inductor plate will automatically stop when it reaches the brim of
the drum.
6
)
Press the “PRESS” button with the lift control switch set to “DOWN”. The inductor plate will be gradually pressed
into a drum while air is being released from the air release hole. Keep holding the “PRESS” button until material
comes out of the hole. Stop pressing the button and secure the plug.
7
)
In the event material doesn’t come out of the hole even though the button is held down, please follow the
following procedure:
①
Close the air release plug on the inductor plate.
②
Close the valve on the piping to prevent material from being discharged.
③
Open the bleeder valve by turning it 3-4 times for releasing air.
④
Open the air valve for the pump and increase air pressure gradually with the pump air regulator. The pump
will start operating at approx. 0.05MPa. Adjust the pump air regulator to set pump speed to 5-8 seconds per
cycle.
⑤
Keep pressing the “PRESS” button until material comes out of the bleeder valve.
⑥
Once material comes out, close the bleeder valve. Then, close the air valve for pump and set the pump air
regulator to 0MPa.
3.3 Operation
CAUTION
-
Material, if containing air bubbles, may gush out when discharged. Put a plastic bag over the
material outlet to receive spurting material.
-
Do not exceed the maximum operating pressure of the pump (0.7MPa). Overpressure may cause a
product failure resulting in serious personal injury and/or property damage.
-
Do not exceed the maximum operating pressure of the lift (0.4MPa). Overpressure may cause a
product failure resulting in serious personal injury and/or property damage.
-
Keep your hand away from the three studs connecting the air motor and lower pump. Fingers can
get caught in the reciprocating plunger.
-
If a defect occurs during lift operation, immediately stop the lift by adjusting the lift control switch to
“STOP”.
-
Do not push the “AIR” button when the lift control switch is set to “STOP” to prevent excessive
pressure in a drum.
-
Leave the lift control switch “DOWN” until a drum becomes empty. A suction failure may be caused
by setting the switch to “STOP”. Also, if the “AIR” button is pushed when there is still material in a
drum, air bubbles will be produced in material.
-
When the lift stops due to a foreign object caught in the sliding part, be sure to move the lift to the
opposite direction BEFORE removing an object. The lift may suddenly start moving if a foreign
object is removed directly.