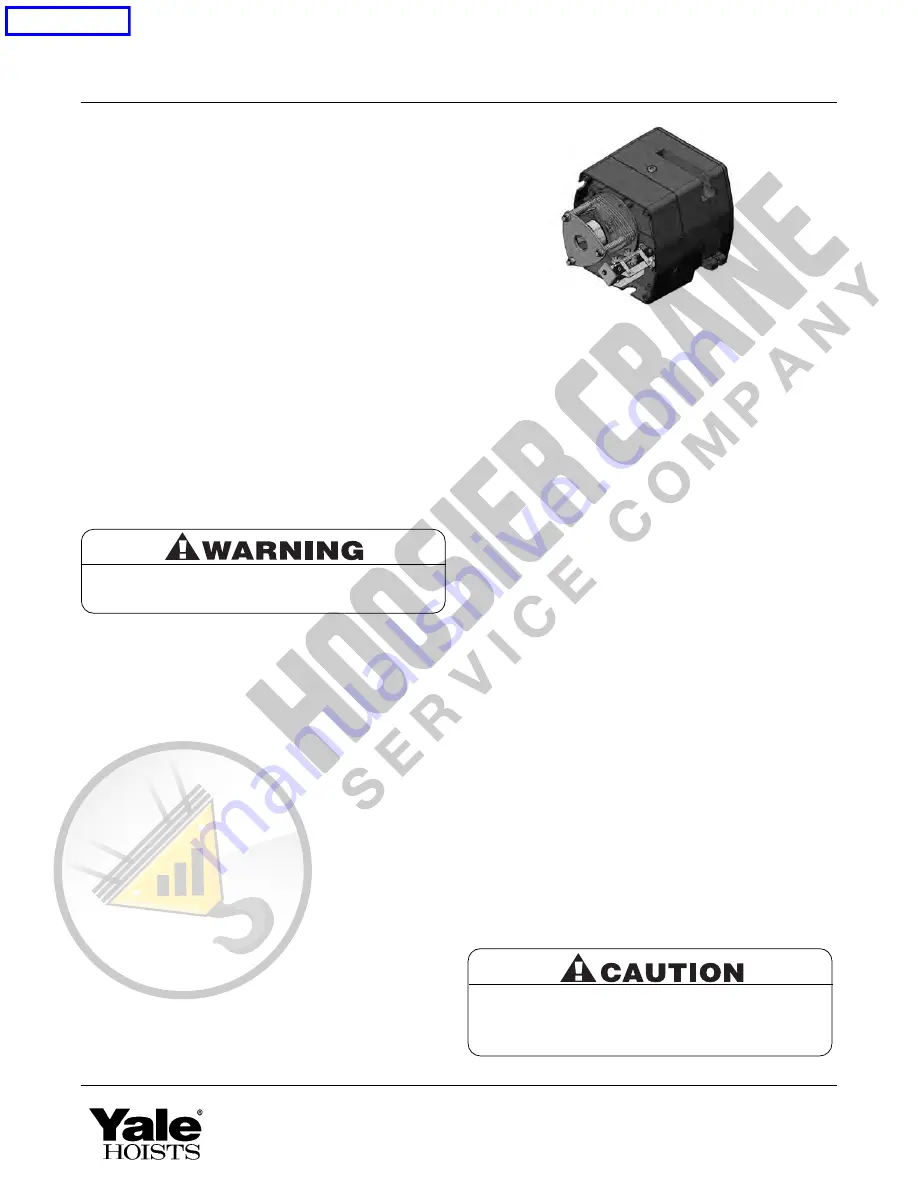
Bearings
All bearings except hook and idler sheave bearings are
lubricated at the factory and should not require additional
lubrication. Noisy or worn bearings should be replaced.
Limit Switch Shaft
Remove any dirt accumulation and spray with a general
purpose lubricant.
Hook Bearing
Apply a few drops of SAE 30 gear or motor oil around the edge
of the bearing.
Idler Sheave Bearing (Bushing)
Disassemble load block and apply a light coat of NLGI #2
grease, or equivalent, inside of bearing.
HOIST REPAIRS
1. For major repairs or when the hoist is to be sectioned in the
suspension area, it will be necessary to move the hoist to a
workbench or table.
2. For repairs which can be done by removing the electrical
cover only, the hoist need not be moved. Lowering the hoist
to a convenient working level is desirable.
NOTE: If you do not have an experienced mechanic to do your
repair work, we recommend that you send your hoist to an
approved service station for repairs. Use authorized repair
parts only.
The following repair instructions will help you in understanding
repair procedures, when related to the Replacement Parts
List starting on page 18. For clarity these are broken down
into areas.
Electrical Parts and Brake
1. Refer to Figures 15, 16 and 17. Remove the cover to access
the controls. Single-phase models also have a starting switch
and capacitor mounted on the panel as shown in Figure 16.
The terminal blocks and end clamps snap off of the rails on
the plate using a small screwdriver. DO NOT SLIDE THE END
CLAMPS.
The reversing contactor can be slid off the rail, but it must be
snapped on. Where the contactor fits the rail, one side has
springs or pads that apply pressure against the edge of the
rail. By pressing against that side at the base of the contactor,
you can snap the part on or off using a rotating action. Note
the numbers that label the terminals on the contactor and
orient the part as shown in Figures 9A-9D. Single-phase
contactors have a small jumper that is not present on the
3-phase (note the 3 and 5 terminals on the reversing
contactor in Figure 9A).
2. Remove the electrical panel by removing the stand-off
screws (See Figures 16 & 17). The limit switch and brake are
now accessible as shown in Figure 6.
3. Remove the transformer bolted to the back of the panel plate
if it requires replacement.
4. Refer to Figure 15 to disassemble the brake. See BRAKE
ADJUSTMENT on page 9 to properly set the brake.
5. Refer to Figures 20 and 21 to disassemble the limit switch.
See LIMIT SWITCH ADJUSTMENT on page 8 to properly
set the upper and lower limits of travel.
6. Refer to Figures 18 and 19 for repairs on the pushbutton
station. Also refer to the wiring diagram inside the electrical
cover or Figures 9A, 9B, 9C and 9D for wiring instructions.
Motor
Refer to Figures 12, 13 and 14.
The hoist motor is located on the opposite end to that of the
electrical parts, but the two are tied together with electrical
leads running through the housing.
1. If it is necessary to replace or repair the motor,
DISCONNECT THE HOIST FROM THE POWER SUPPLY
and remove the electrical cover.
2. Loosen the screw clamps on the terminal blocks and
reversing contactor to disconnect the motor leads
(See Figures 16 and 17).
3. Remove the four motor mounting bolts attaching the motor
to the housing. It will come loose at the motor coupling.
4. Inspect the motor coupling, motor shaft and all the bearings.
Replace as necessary.
5. Install new or repaired motor according to the wiring diagram
located inside the electrical cover or Figures 9A, 9B, 9C
and 9D.
Gearing
Refer to Figures 7, 12 and 22.
As disassembly is extensive for gearing, disconnect the hoist
and move it to a workbench.
1. Remove the electrical cover.
2. Remove the electrical panel.
3. Remove the brake assembly and the limit switch assembly.
4. Drain the oil from the transmission.
5. Remove the four screws that attach the transmission cover
to the gear housing and remove the transmission cover. The
limit switch drive shaft will come along with the cover.
10
Remove load and disconnect hoist from power supply
before starting to do any repairs or to take any
sections apart.
Figure 6 - Electrical Panel Removed
Do not disassemble or readjust the clutch, or replace
it with a clutch assembly from another hoist. Doing so
will void the warranty and may create an unsafe
condition. If replacement is needed due to wear or
loss of adjustment, always use a new clutch assembly.
Go To Index