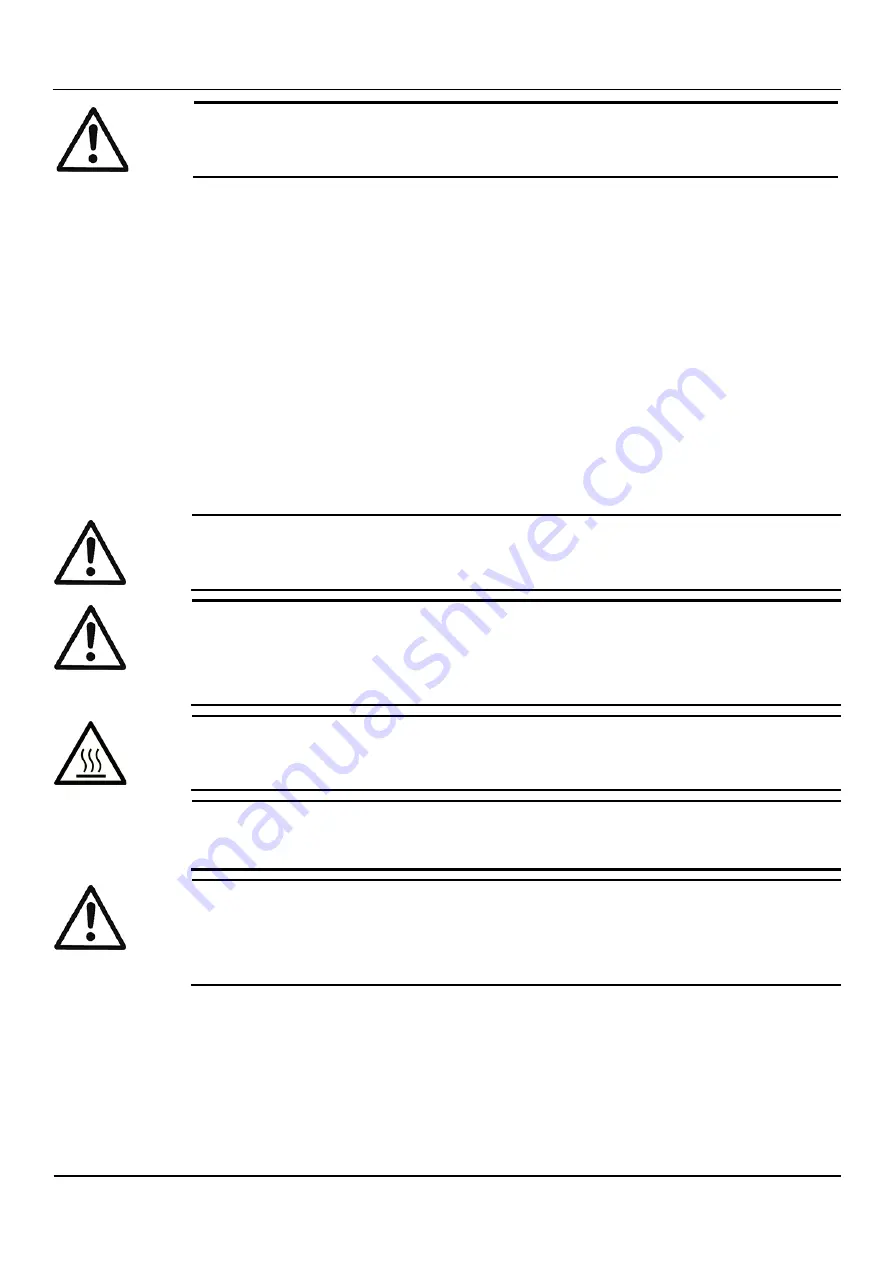
en – Original instructions
e-IXP(A), e-IXPC(A), e-IXPF(A) – Additional Installation, Operation and Maintenance Manual
21
DANGER: Explosion due to static charge
Ensure that the base plate is earthed correctly.
Reducing vibrations
The motor and the flow of liquid in the piping can generate vibrations, which may be amplified
from the possible incorrect installation of the unit and the piping. See
page 21.
4.2.4
Frame installation
•
The frame must be rigid and must not vibrate during operation
•
The contact surface of the pump and motor feet support bases must be as level as possible
•
Position the pump and the motor at a distance that allows the coupling to be fitted
•
Ensure a gap of 4-6 mm (0.16-0.24 in) between the frame and the motor to allow for vertical
adjustment in case of replacement.
•
Make sure that the pump and the motor are securely attached to the frame.
4.3
Hydraulic connection
4.3.1
Precautions
WARNING:
The piping system must be sized to ensure safety at the maximum operating pressure and
temperature.
WARNING: Danger of hot and/or toxic liquid escaping from non-sealed piping system
connections
Support the piping system independently to prevent them from weighing on the unit. Secure
the piping system to the unit ports making sure to comply with the permitted forces and
torques. Install appropriate gaskets between the unit and the piping system.
WARNING: Hot surface hazard
If the temperature exceeds 60°C (140°F), isolate the unit before touching it.
f
NOTE:
When carrying out welding activities never use the unit for grounding: risk of pitting damage
to the bearings.
CAUTION: Residues from welding work or other impurities in the pipes lead to pump damage
The type and the duration of the cleaning activity during the flush and pickling operations must
be in accordance with the used casing and sealing materials.
Use a filter with 0.5 mm mesh and 0.25 mm wire diameter made of corrosion-resistant material.
Insert a filter with a section three times that of the pipeline.