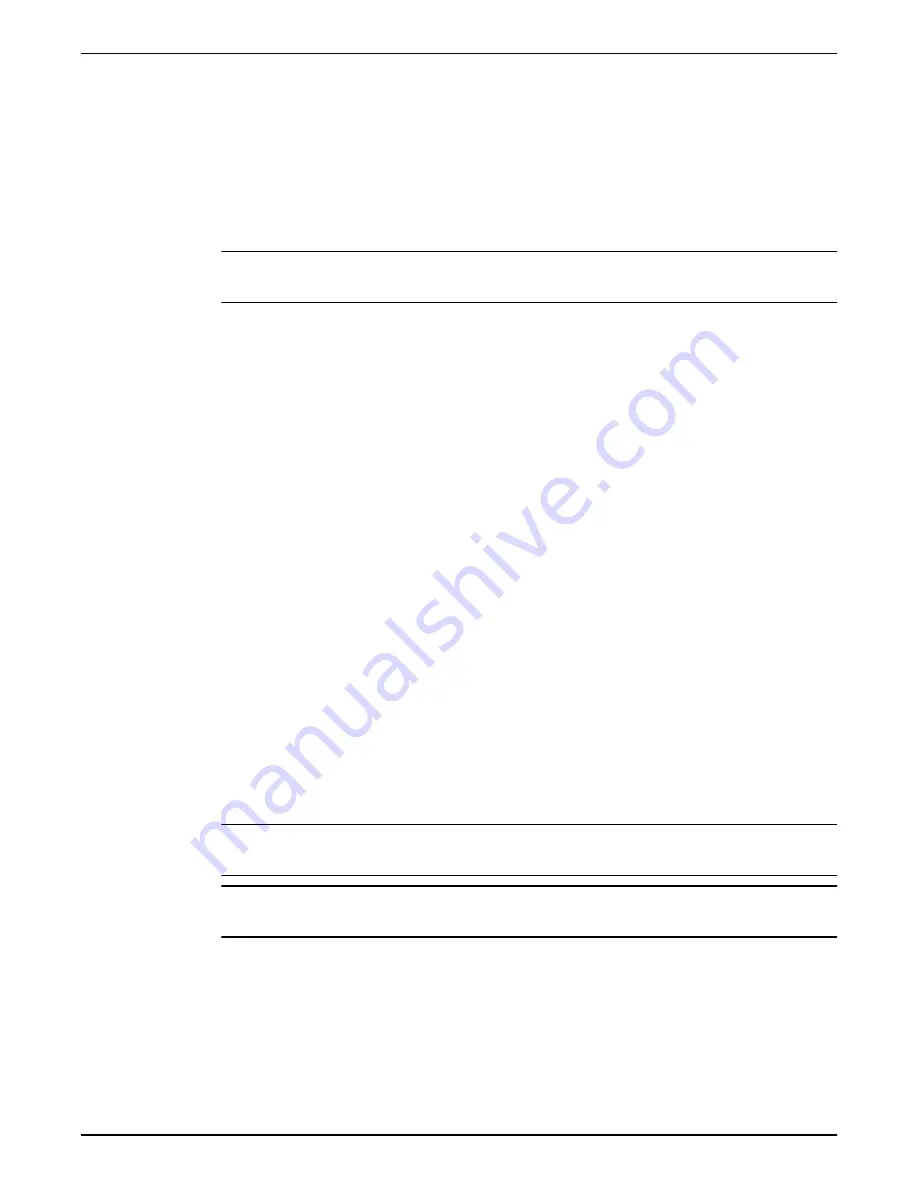
2.3 Temperature ranges for transportation, handling and storage
Handling at freezing temperature
At temperatures below freezing, the product and all installation equipment, including the
lifting gear, must be handled with extreme care.
Make sure that the product is warmed up to a temperature above the freezing point
before starting up. Avoid rotating the impeller/propeller by hand at temperatures below
the freezing point. The recommended method to warm the unit up is to submerge it in the
liquid which will be pumped or mixed.
NOTICE:
Never use a naked flame to thaw the unit.
Unit in as-delivered condition
If the unit is still in the condition in which it left the factory - all packing materials are
undisturbed - then the acceptable temperature range during transportation, handling and
storage is: –50°C (–58ºF) to +60°C (+140ºF).
If the unit has been exposed to freezing temperatures, then allow it to reach the ambient
temperature of the sump before operating.
Lifting the unit out of liquid
The unit is normally protected from freezing while operating or immersed in liquid, but
the impeller/propeller and the shaft seal may freeze if the unit is lifted out of the liquid
into a surrounding temperature below freezing.
Follow these guidelines to avoid freezing damage:
1. Empty all pumped liquid, if applicable.
2. Check all liquids used for lubrication or cooling, both oil and water-glycol mixtures, for
the presence of unacceptable amounts of water. Change if needed.
Water-glycol mixtures: Units equipped with an internal closed-loop cooling system are
filled with a mixture of water and 30% glycol. This mixture remains a flowing liquid at
temperatures down to –13°C (9°F). Below –13°C (9°F), the viscosity increases such that the
glycol mixture will lose its flow properties. However, the glycol-water mixture will not
solidify completely and thus cannot harm the product.
2.4 Storage guidelines
Storage location
The product must be stored in a covered and dry location free from heat, dirt, and
vibrations.
NOTICE:
Protect the product against humidity, heat sources, and mechanical damage.
NOTICE:
Do not place heavy weights on the packed product.
Long-term storage
If the unit is stored more than six months, then the following apply:
• Before operating the unit after storage, it must be inspected with special attention to
the seals and the cable entry.
• The impeller/propeller must be rotated every other month to prevent the seals from
sticking together.
2 Transportation and Storage
2008 Ready 8, 8S Installation, Operation, and Maintenance
7
Summary of Contents for Flygt 2008 Ready 8
Page 1: ...Installation Operation and Maintenance 898397_4 0 2008 Ready 8 8S...
Page 2: ......
Page 43: ......