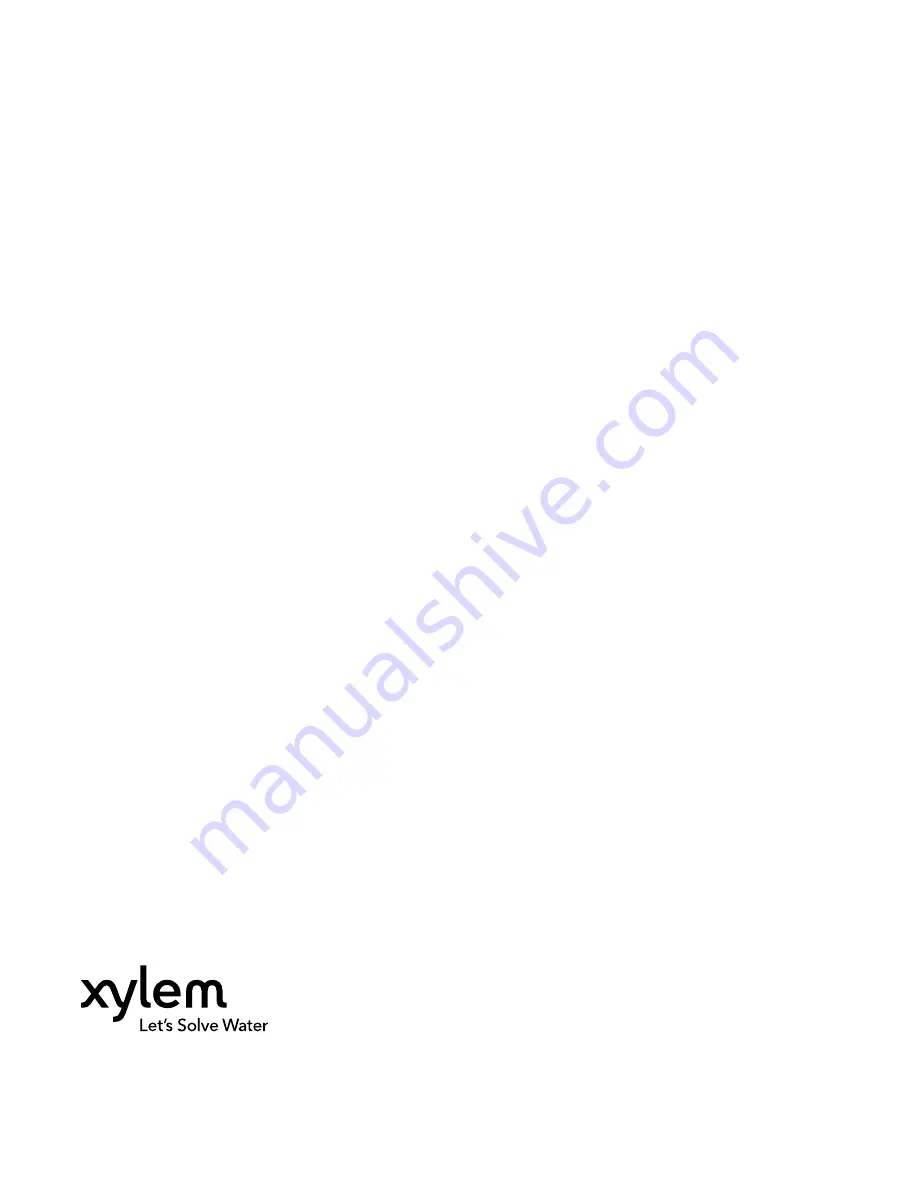
Xylem |’zīl
ə
m|
1) The tissue in plants that brings water upward from the roots;
2) a leading global water technology company.
We’re a global team unified in a common purpose: creating advanced
technology solutions to the world’s water challenges. Developing new
technologies that will improve the way water is used, conserved, and re-used in
the future is central to our work. Our products and services move, treat, analyze,
monitor and return water to the environment, in public utility, industrial,
residential and commercial building services settings. Xylem also provides a
leading portfolio of smart metering, network technologies and advanced
analytics solutions for water, electric and gas utilities. In more than 150 countries,
we have strong, long-standing relationships with customers who know us for our
powerful combination of leading product brands and applications expertise with
a strong focus on developing comprehensive, sustainable solutions.
For more information on how Xylem can help you, go to www.xylem.com
Visit our Web site for the latest version of this document
and more information
.
The original instruction is in English. All non-English
instructions are translations of the original instruction.
©
2019 Xylem Inc
P7000005_en-US_e-MPA, e-MPR, e-MPD Horizontal Multistage Pump
Summary of Contents for e-MPA
Page 1: ...INSTRUCTION MANUAL P7000005 e MPA e MPR e MPD Horizontal Multistage Pump ...
Page 2: ......
Page 42: ......
Page 43: ......