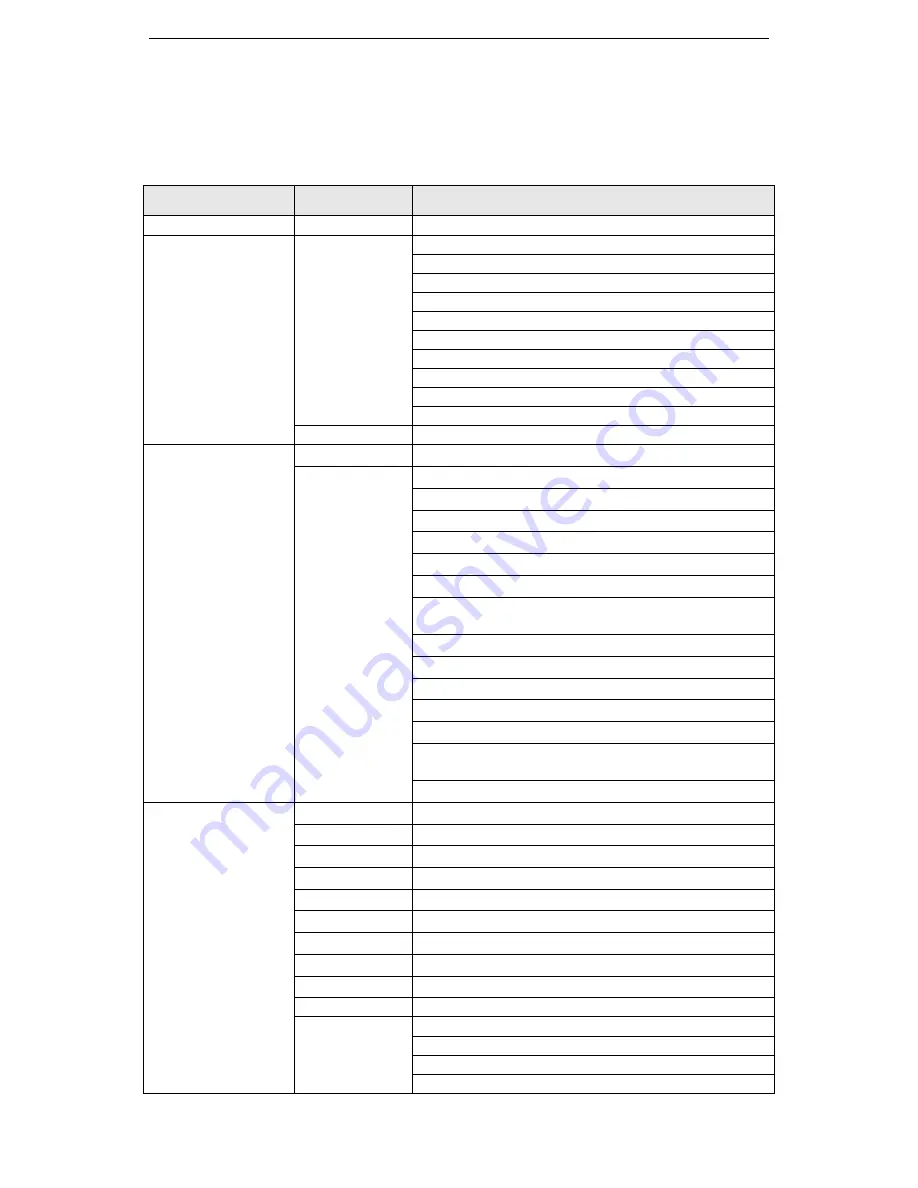
V5 series inverter
95
sent. The receiving device will calculate the CRC again and compare to the received CRC value. If the
two value are not the same, discard this frame and receive the next frame.
7-3-3.Communication parameter
Name
Parameter address
Function
Internal parameters setting
GGnnH
GG stands for parameter group, nn stands for parameter No.
Command for inverter
(06H)
2000H
0001H: Running command (Forward)
0002H: Forward command
0003H: Reverse command
0004H
:
Jog command (Forward)
0005H: Jog forward command
0006H: Jog reverse command
0007H: Decerlate stop command
0008H: Emergency stop command
0009H: Jog stop command
000AH: Fault reset command
2001H
Set frequency via serial port
Monitor inverter status
(03H)
2100H
Read inverter fault code
2101H
Read inverter status
BIT0: stop sign, 0: Stop; 1: Run
BIT1: 1: under voltage; 0: normal
BIT2: forward/reverse sign,1: forward; 0: reverse
BIT3: jog sign 1: jog; 0: not jog
BIT4: close loop control selection, 1: close loop; 0: not close loop
BIT5: swing frequency sign1: swing frequency 0: no swing fre-
quency
BIT6: PLC running flag, 1: PLC running , 0: no
BIT7: Multi-speed running flag of terminals, 1: Multi-speed; 0: no
BIT8: Common running flag, 1: common running; 0: no
BIT9: Main frequency from communication interface, 1: yes; 0: no
BIT10: Main frequency from analog input, 1: yes; 0: no
BIT11: Running command from communication interface, 1: yes;
0: no
BIT12: Password protection for parameters, 1: yes; 0: no
2102H
Read inverter setting frequency
2103H
Read inverter output frequency
2104H
Read inverter output current
2105H
Read inverter bus voltage
2106H
Read inverter output voltage
2107H
Read motor speed
2108H
Read module temperature
2109H
Read VI analog input
210AH
Read CI analog input
210BH
Read inverter software version
210CH
I/O terminal status
Bit0: X1
Bit1: X2
Bit2: X3