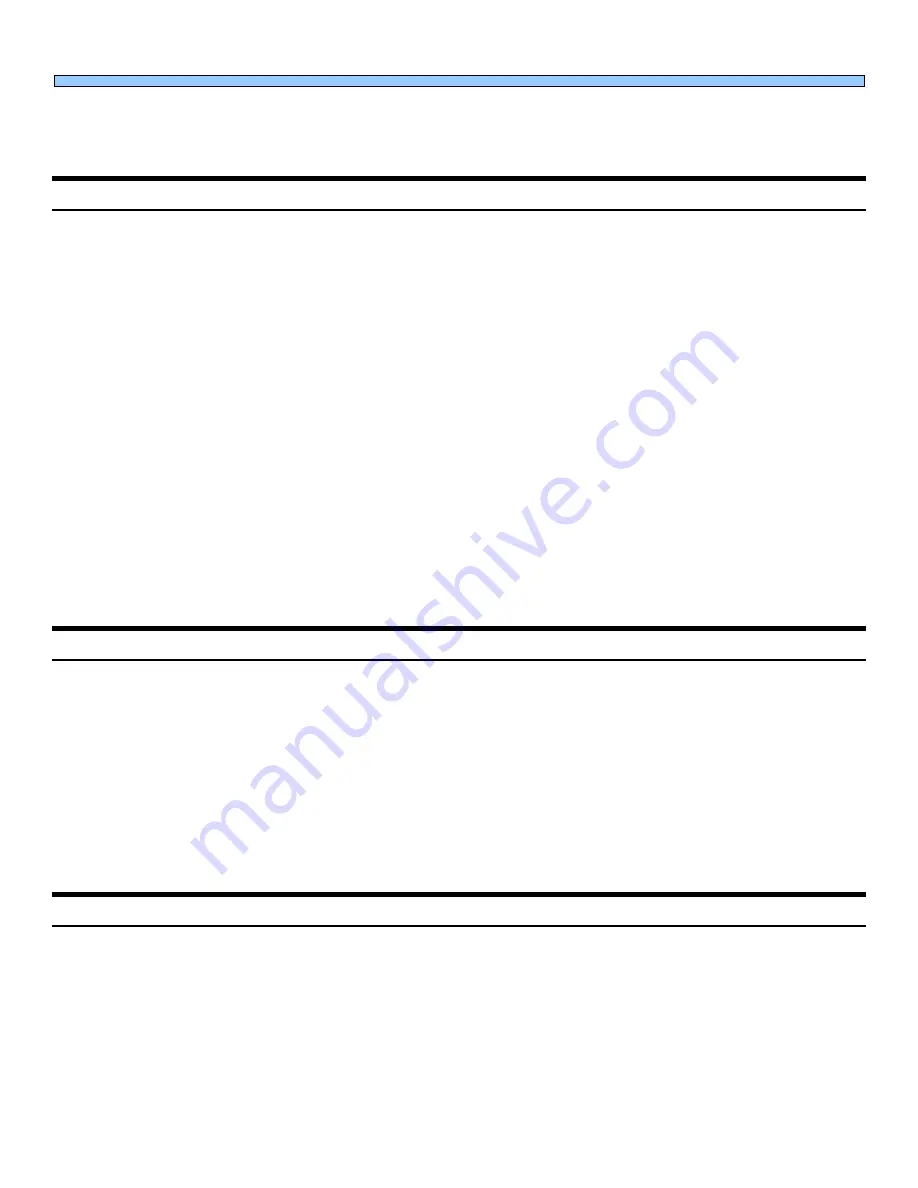
For more information on Genuine Xerox Supplies, call 1-800-822-2200 in the USA and 1800-668-0133 in Canada
9
equipped with an interposer since they do not have to pass through the fusing unit. Residual fuser oil
may, however, still lead to feeding and registration difficulties.
Pre-print ed Form s and Print ing Ink s
Choosing the correct ink is the first step in designing forms that will function well in Xerox printers.
The forms should be printed with inks that cure well, are not tacky, and do not offset (transfer from a
printed sheet onto other surfaces). In choosing an ink, form printers must consider the conditions to
which the forms will be exposed while passing through the printer, taking into consideration the heat,
pressure, and dwell time during which the pre-printed paper is subjected to both.
In the past, good performance has been reported when using inks of the oxidative type, those that
are cured using ultraviolet (UV) light, and laser-safe inks. Oxidative inks may require several days to
harden satisfactorily, laser inks usually cure within 24 hours, and UV inks change immediately from
liquid to solid upon exposure to an ultraviolet light source. Special care must be taken to ensure that
pre-printed materials, for use in laser printers, use inks that do not offset. It is recommended that you
work closely with suppliers to verify that requirements are understood and met.
Drying agents are sometimes sprayed on printed sheets as they exit the printing press in an effort to
reduce the possibility of offsetting onto one another. These materials (typically powders) can become
contaminants when carried through Xerox printers. You should avoid using forms that have been
sprayed with these materials.
Always test the application before running production as liability ultimately lies in the hands of the
customer.
GBC
and VeloBind
Papers
GBC paper is a 19-hole drilled paper ready for binding using the spiral wound GBC binding system.
VeloBind paper is an 11-hole drilled paper used for comb binding.
The guidelines for loading and running jobs using GBC or VeloBind papers are the same as those for
other drilled papers. Misfeeds may occur more often with GBC and VeloBind papers than with
recommended drilled papers due to interlocking of the sheets caused by dull punches. Paper jams
caused by plugs (the pieces cut out of the paper to create the holes) may be more frequent. Stacking
of GBC and VeloBind papers in the paper tray will not be as good as when using plain paper
because of possible interference of the punched holes in adjacent sheets. It is also important to note
that image quality will be highly dependent upon paper stock quality.
Papers w it h a Tex t ured Finish
Papers with a textured finish have a surface contour, gloss, and appearance that affects toner
placement and image quality. One common example is paper with a linen finish. The smoothness or
roughness of the paper surface will significantly affect the results of the printed output.
Papers with a textured finish can be run on the DocuColor 5000AP with reasonable print quality but
will show the linen pattern. The peaks and valleys created by the textured finish may create areas
where toner cannot reach.