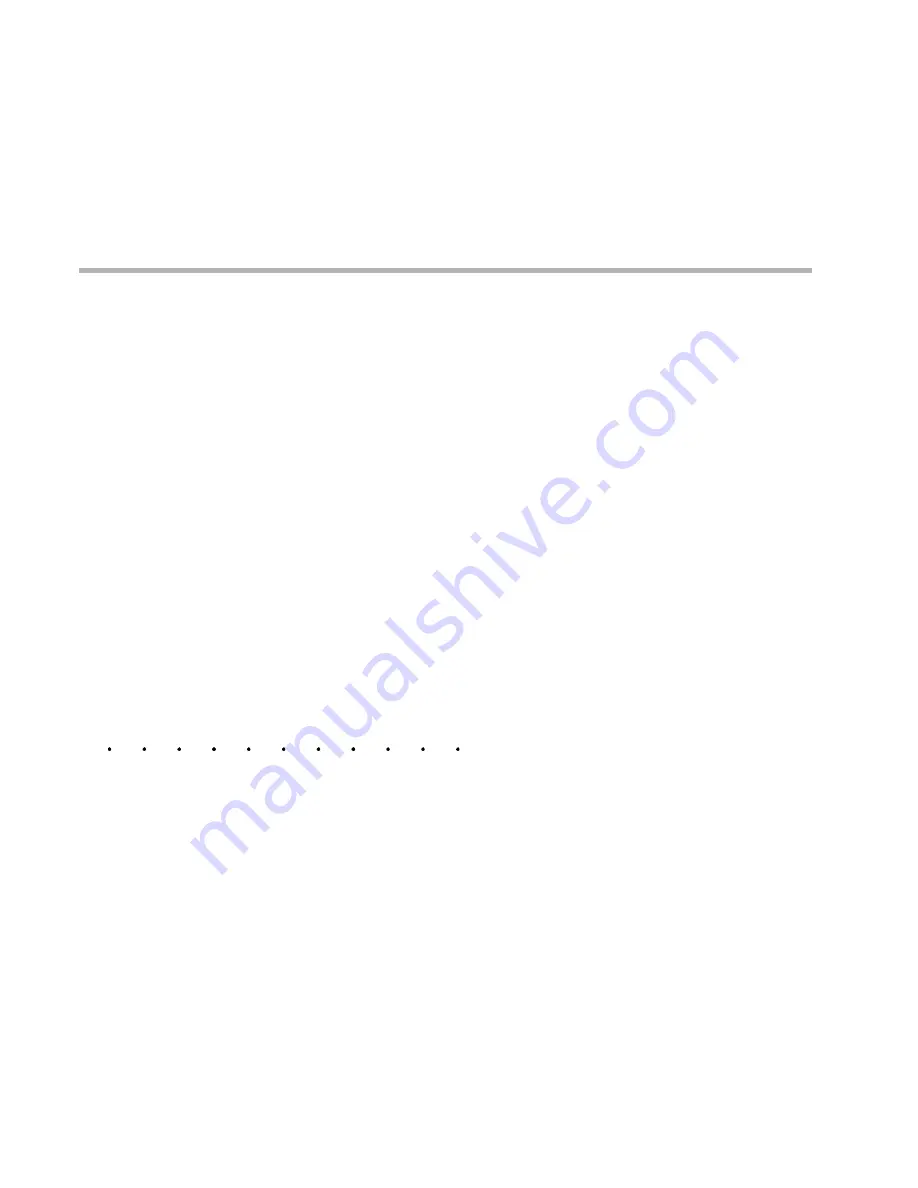
=UTGU\T# %?`UbQd_bµc7eYTUD)## "
#!
= #" "%1`bY\" "
&RPPXQLFDWLRQVDQG,2
The MedWeld 3005 communicates with automation equipment
using one of three integration schemes:
•
Remote I/O.
This transmits I/O via the “Blue Hose”
connection to a host PLC outside the weld control enclosure.
•
DeviceNet
, where I/O is transmitted to a DeviceNet drop
line and sent to a network via the PLC host.
•
Discrete I/O
. Inputs and outputs are directly wired into the
control’s enclosure.
The type of integration provided is determined by software
provided in the ladder logic for the PLC, as well as the physical
modules contained in the PLC chassis. These are detailed in
“Physical Description” on page 1-2.
The following sections describe each option and the I/O
provided.
/RFDODQG6DIHW\,2
When the MedWeld 3005 is part of a network (as with the Remote
I/O or DeviceNet integration), the WTC combination module
provides for local (discrete) control of certain critical inputs and
outputs.
These outputs are the same for both integration options. As
described in “Providing Local and Safety I/O” on page 2-3, the
connections to these I/O should be provided. These tell the
processor factors such as the status of the isolation contactor, the
control stop condition and fault conditions.
This I/O is in addition to the I/O mapping provided for remote
I/O and DeviceNet operation.
Summary of Contents for MedWeld 3005
Page 2: ...YY UTGU T UbQd_bµc 7eYTU V_b D 1 bY ...
Page 84: ...3_ e YSQdY_ c Q T 9 UTGU T UbQd_bµc 7eYTU D 1 bY ...
Page 110: ...GU T CSXUTe Uc UTGU T UbQd_bµc 7eYTU D 1 bY ...
Page 126: ...1TfQ SUT C_VdgQbU 6UQdebUc UTGU T UbQd_bµc 7eYTU D 1 bY ...
Page 144: ...CUde QbQ UdUbc UTGU T UbQd_bµc 7eYTU D 1 bY ...