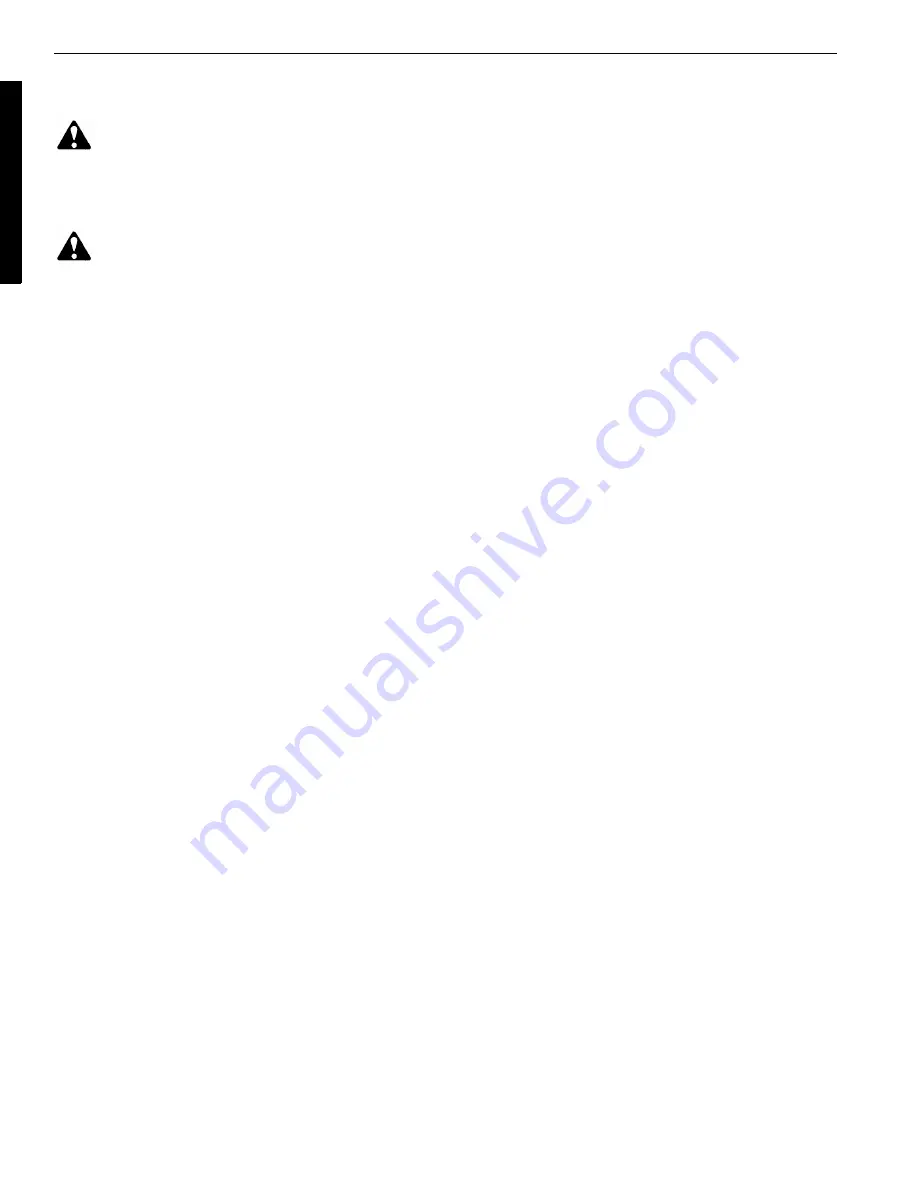
WSM U15, U15-3 Service
I-S-4
B.Safety precautions for servicing, disassembly and reassembly
Safety precautions for servicing
Most accidents during servicing arise from carelessness. Please remember that Safety involves both the
welfare of the employees and improved work efficiency.
Safety precautions for Disassembly and reassembly
Machines must be diassembled and assembled efficiently and safely.
It is very important to thoroughly understand the construction and function of the machine, to make all appro-
priate preparations, and start operations according to the specified working procedures.
a. Safety measures before starting work
(1)Work clothes
1. Wear specified work cap and clothed.
(Under no circumstances may workers wear
undershirts only.)
Cuffs must be kept buttoned, and any tears
must be mended.)
2. Wear safety shoes.
3. Do not wear cotton gloves when working on
the internal section of engine, reduction
gears or hydrauricunits for repair or others,
or when using a hammer. Wear leather
gloves, however, when hoisting wires.
(2)Inspecting equipment and tools
1. Prepare equipment (cranes, fork lifts, tool,
etc.) required for servicing and inspect for
any problems before starting work.
2. Hammer heads (metal parts) must be firmly
secured to their handles.
3. Check hosting tools (wire ropes, hoisting
chains, etc.) before use.
(3)Keep workshop in order
1. Secure appropriate space needed for disas-
sembly to the job.
2. Secure a clean, safe place for arranging dis-
assembled parts.
3. Store volatile substances (gasoline, light oil,
thinner, oily articles, etc.) in appropriate con-
tainers at selected locations to prevent fire
hazards.
b. Safety measures during work
(1)Protectors
1. Wear goggles when using chisels for chip-
ping.
2. Use appropriate protectors during welding.
3. Wear a helmet when working with a crane or
at elevated locations.
(2)Team work
1. When working with two or more people,
divide the work and maintain close commu-
nication.
2. Clane work must be carried out using prede-
termined signals.
(3)Disassembly and assembly
1. Do not wear gloves when using hammers.
2. Use rods of the specified soft material for
removing pins. Do not use a hammer as a
pad.
3. Do not place fingers in holes when center-
ing.
4. Heavy parts must be adequately supported
before removingbolts.
(4)Cranes
1. In principle, use a crane for objects heavier
than 44lb (20kg).
2. Crane operation and hoisting must be per-
formed only by qualified personal.
3. Pay careful attention to the center of gravity
when hoisting, and do not stand under the
lifted objects.
(5)Others
1. To work under a jacked-up carrier, be sure to
place wood pieces under it.
2. When charging batteris, make sure there
are no open flames in the immediate vicinity.
3. All electric tools must be grounded.
4. Before welding the machine, remove the
battery.
• When removing the battery, be sure to dis-
connect negative (-) cord first.
• When mounting the battery, be sure tp
connect the positive (+) cord first.