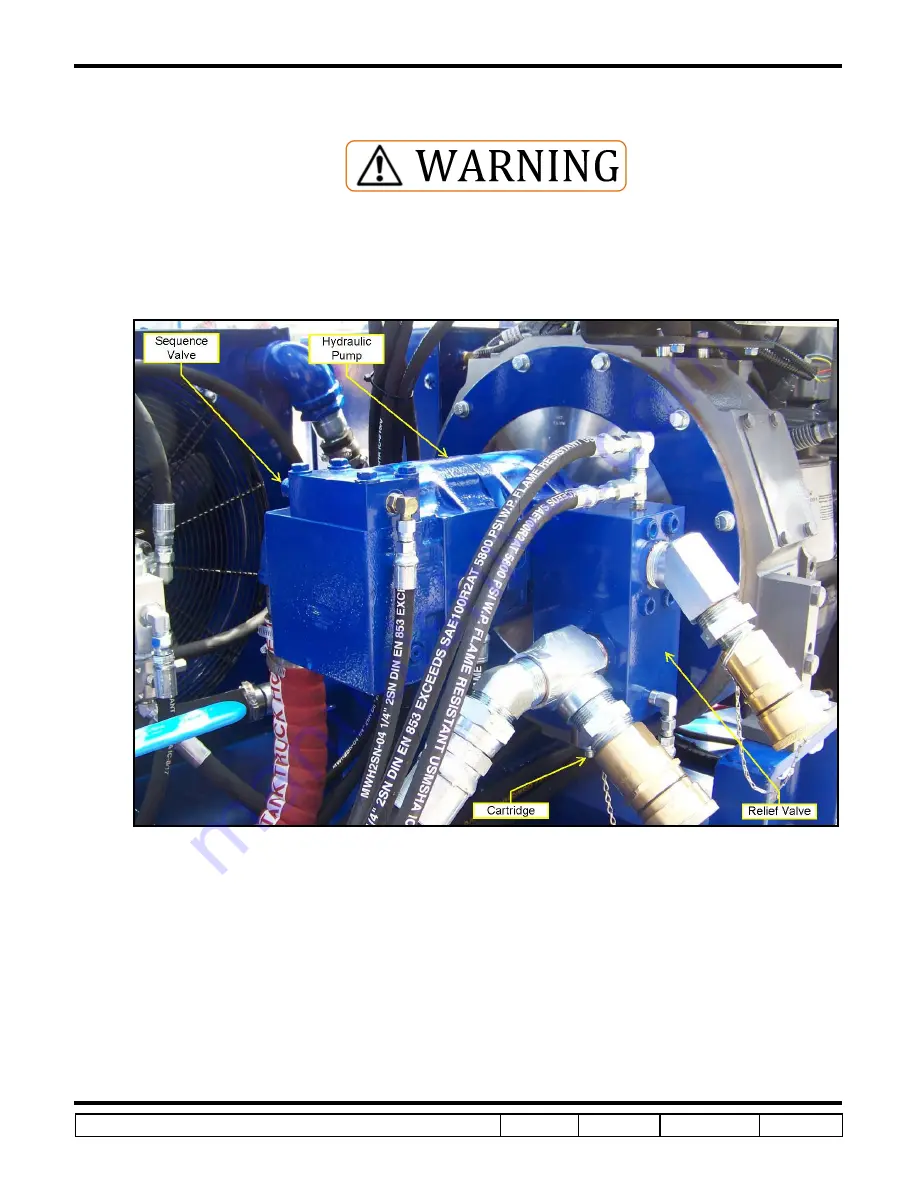
Model 30000-S DHPU Manual
Rev. 0
JRK
17SEP12
Page 18
adjusted in the field. However, the following procedure can be used to set a replacement
cartridge in the field.
DO NOT ATTEMPT TO ADJUST THE PUMP SEQUENCE VALVE WHILE THE UNIT IS
RUNNING.
DO NOT INCREASE THE SEQUENCE VALVE SETTING PAST 1500 PSI.
Figure 10: System Relief and Pump Sequence Valves
The pump's sequence valve can be seen in the previous picture. With the unit off, remove
the cap from the end of the cartridge stem. To adjust the valve setting, loosen the jam nut on
the cartridge valve stem. Turn the screw clockwise to increase the pressure setting and
counter clockwise to reduce the setting. Lock the jam nut back down after adjusting the
valve setting. Upon completion, tighten the cap back onto the cartridge stem.
To check the valve setting, block the pressure port by disconnecting the pressure line at the
quick disconnect. Loosen the jam nut on the system pressure relief valve (RV-1). Lower RV-
1's pressure setting all the way by turning the set screw counter-clockwise. Next, start the
power unit. Increase the system pressure by turning the RV-1 set screw clockwise. Around