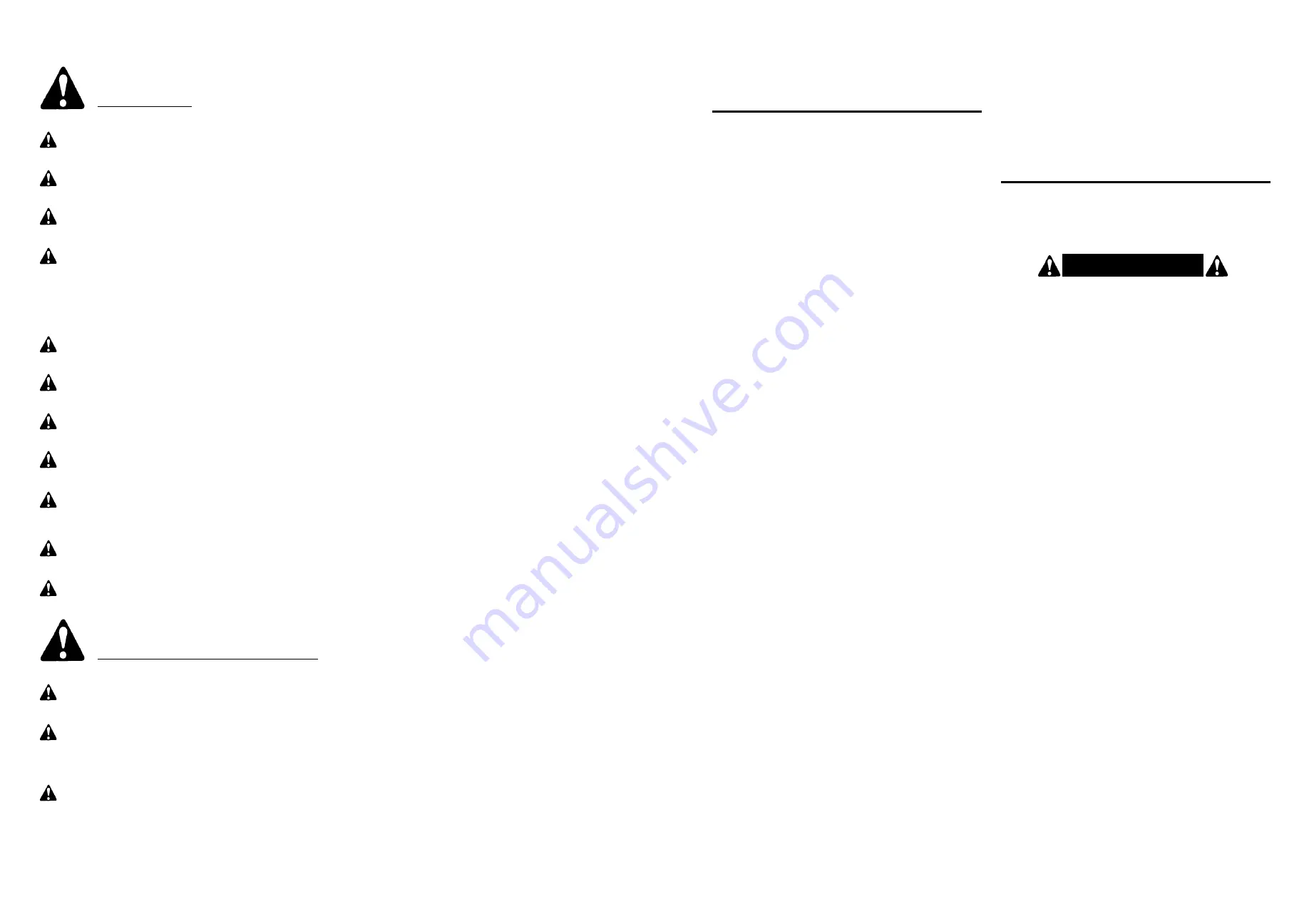
15
6
S A F E T Y I N S T R U C T I O N S
(continued)
Keep safety signs clean and legible at all times.
Replace safety signs that are missing or have become illegible.
Replaced parts that displayed a safety sign should also display the current sign.
Safety signs are available from your Distributor or Dealer Parts Department or the factory.
Be sure that the installation area is clean and dry.
Be sure temperature is above 50˚F (10˚C).
Decide on the exact position before you remove the backing paper.
Remove the smallest portion of the split backing paper.
Align the sign over the specified area and carefully press the small portion with the exposed sticky backing in
place.
Slowly peel back the remaining paper and carefully smooth the remaining portion of the sign in place.
Small air pockets can be pierced with a pin and smoothed out using the piece of sign backing paper.
Be certain the tractor or skid steer is in neutral or park position before starting engine.
Always shut off power unit and shift to “Park” or set brakes when leaving unit. Always lower bucket or
attachment to ground, relieve all hydraulic pressure. Remove key when leaving equipment unattended. Park
in level area.
Before operating equipment: if you have any questions regarding the proper assembly or operation, contact
your dealer or representative.
How to Install Safety Signs:
SAFETY SIGNS
STARTING AND STOPPING SAFETY
Remove the bucket from your front end loader. Check
your loader to make sure it is in good working order.
Check all frame mounting bolts to make sure they are
tight.
Loaders that attach to the tractor frame rails should
have a cross-tie installed for stability.
Refer to the “exploded view” of the Loader Fork on
page 20 of this manual.
Assemble the two lift brackets (Ref. #3) on the main
frame (Ref. #1) with the
5
/
8
” x 3” I.D. U-bolts. Leave the
U-bolts loose.
NOTE: The lift channel brackets are supplied with 1”
diameter pins to fit your loader. If your loader requires
1
1
/
8
” pins, it will be necessary for the hole diameter in the
channel brackets to be drilled out to 1
5
/
32
” (1.156”) and
ask your dealer to order 1
1
/
8
” diameter pins. The 1
1
/
8
” pins
are part #830318. Be sure to indicate if two or four 1
1
/
8
”
pins are required.
If your loader requires 1
1
/
4
” diameter pins, please ask
your dealer to order adapter bushings (part #830319). Be
sure to indicate how many adapter bushings are
required.
If your tractor loader has a bucket Quick Attach feature,
check with your dealer on the availability of adapter
brackets for your brand and model loader.
Connect the above assembly to the loader arms using
the bottom hole in the channel and attach the upper con-
trol cylinder to the top hole in the lift channels. Center the
main frame (side to side) with your loader arms and
tighten the four (4)
5
/
8
” x 3” U-Bolts.
The lower hole positions in the lift channels can be
used to obtain more angle movement. However, if the
frame becomes too parallel with the loader lift arms, the
loader may not have enough power (mechanical advan-
tage) to bring the frame back.
NOTE: The Ford Model 7109, 7209, 7210 and 7410
Loaders require special mounting brackets instead of the
standard lift channels supplied. Order #830330 for this
application.
NOTE: Generally, it is not recommended to have the tilt
cylinders located any closer than 10-12 inches to the
main loader lift arms. Check the spacing of mounting
pins on your loader bucket and use this as a guide.
If tilt cylinders are located too close to the loader arms,
they may go “over center” when fully extended. If this
happens, damage may occur to the cylinders and/or
mounting brackets.
NOTE: The Model VLF-7655 and VLF-7646 have
special quick-attach brackets on the frame. No lift
channel brackets are required.
I N S T R U C T I O N S
(continued)
A S S E M B LY –
T R A C T O R L O A D E R S
A S S E M B LY – SKID STEER AND
T R A C T O R L O A D E R S
Remove the bucket from your skid steer unit and con-
nect the main frame of the pallet fork to the universal
quick-attach coupler.
Raise the loader and main frame slightly so that the
bottom of the main frame is about one or two inches off
the ground. Engage tractor parking brake and shut off
the engine.
Remove the forkshaft from the main frame by remov-
ing the lock bolt on end of the forkshaft and slide it out
until about 12” remain through one end of the frame.
Place one fork locking collar on the shaft and place the
fork tine into position and slide the forkshaft through
them. Place another lock collar on the forkshaft and slide
into the center support until the shaft extends about 8”
past the center support.
Place another fork locking collar and place second fork
tine into position and continue sliding the forkshaft until it
is all the way through the second fork.
Slide the last locking collar on the fork shaft and then
continue sliding the forkshaft until it is through the last
shaft support.
Rotate the forkshaft until the clip on the end lines up
with the hole in the end support bracket. Replace the lock
bolt and tighten.
Slide the fork tines into the desired position and tight-
en the lock collars on each side of each fork tine.
ADJUSTING TINE WIDTH
1. Block up the forklift frame.
2. Loosen lock bolts and slide forklift tines to desired set-
ting. Each tine must be the same distance from the
center of the forklift. Tighten lock bolts.
IMPORTANT: Keep forklift tines adjusted to maxi-
mum width for better load stability.
To help prevent personal injury, stand clear of frame
and loader. Keep feet away from underside of main
frame.
C A U T I O N !